From nano to macro: Nanoscale 3D printing that is fast, smooth, and scalable
Additive manufacturing – also called 3D printing – has revolutionized many fields, and has spurred researchers to investigate manufacturing techniques at the micro- and nano-scale. One such technique is multi-photon lithography, where a volume of resin is exposed to a series of focused high-intensity laser pulses, which causes the resin at the focal point to solidify almost instantly. By moving the laser and/or the resin, 3D shapes can be built.
In a new paper published in Light: Science & Applications, a Purdue team led by Xianfan Xu, the James J. and Carol L. Shuttleworth Professor of Mechanical Engineering, has combined multi-photon lithography with spatiotemporal focusing of femtosecond laser pulses to demonstrate rapid, continuous printing of complex 3D structures.
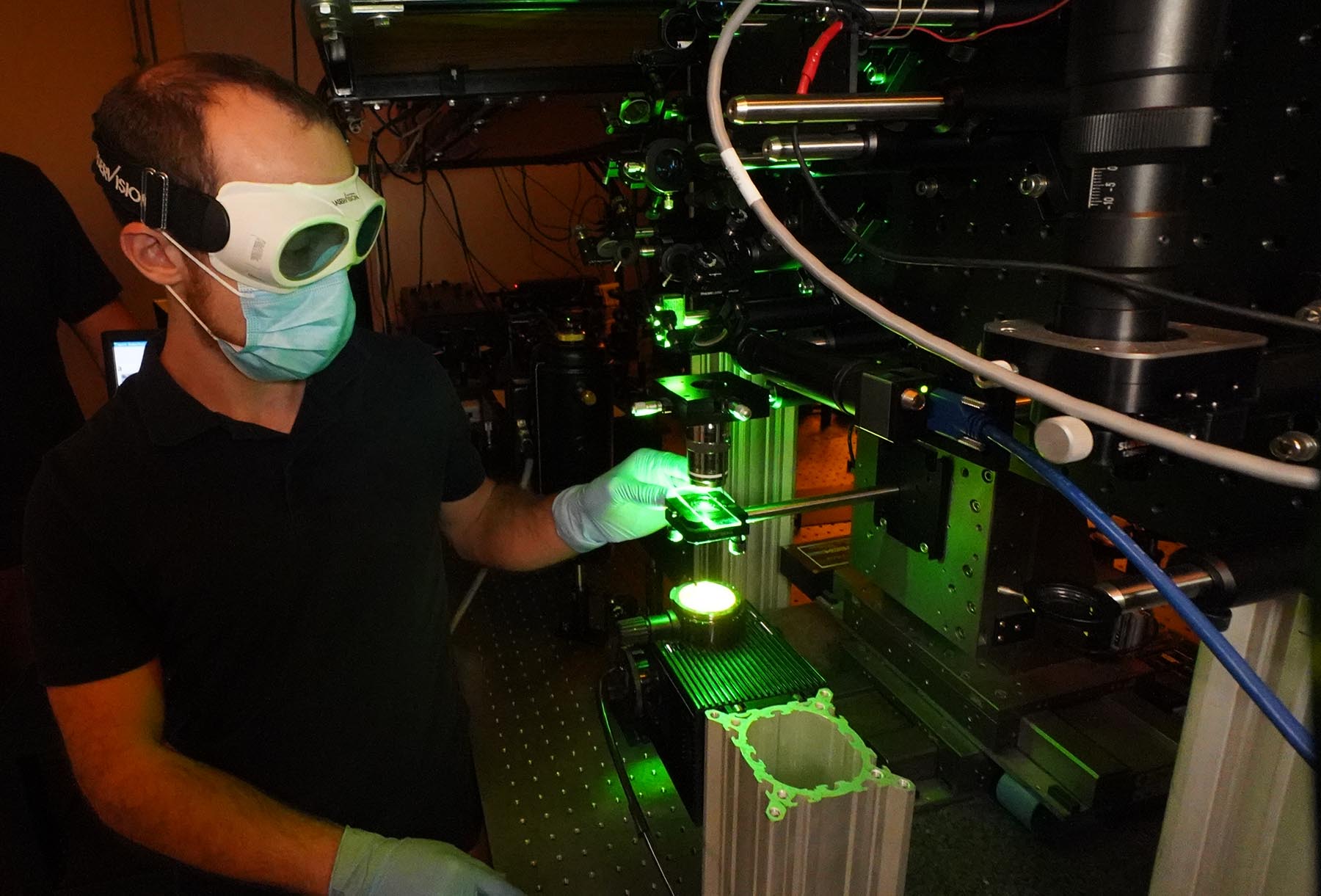
“Multi-photon lithography has been studied for more than 20 years,” said Paul Somers, PhD student in Mechanical Engineering, and lead author of the paper. “It has great potential, but it’s still slow. Our goal is to speed it up and scale it up, so that it can be used to manufacture useful structures with high speed and high fidelity.”
To achieve this goal, they use spatiotemporal focusing. A digital micro-mirror device (an array of tiny mirrors controlled by a computer) separates the laser into multiple wavelengths of light and then recombines them, which accurately pinpoints the area of the resin they want to solidify. With this technique, they can print an entire 2D layer instantly, while physically moving the platform up and printing another horizontal layer.
“You see this with typical 3D printers, where it deposits a layer of plastic, and then moves up to deposit another layer, leaving you with jagged edges,” Somers said. “But our technique is continuous. The platform doesn’t stop and start; it moves continuously, so rather than distinct layers, it’s one smooth shape all the way up. This allows us to print much faster, with no layering artifacts, and make complex shapes that traditional 3D printing can’t do.”
They demonstrated this technique by printing complex rounded shapes like a trefoil knot, and a replica of the Cloud Gate sculpture in Chicago – each printed in less than a second, with no jagged edges or other artifacts.

Because of the size of their mirror array, the layer size was restricted to 25 microns by 44 microns. To counter this restriction, they combined multiple tiny structures into one larger structure. In one printing session, they printed more than 74,000 of the tiny shapes into a 42 x 42 x 42 unit cube, nearly 1 millimeter in width. This demonstrated that multi-photon lithography has the potential to build highly complex structures, with customized designs, in a practical time frame.
“Imagine a doctor wants to bio-engineer a custom scaffolding for tissue cells to grow on,” Somers said. “With this technique, we can rapidly build multiple nanostructures into a complex macroscale object. We can achieve the same detailed properties of the nanostructures, but build them into objects that are useful in the real world, in a practical timeframe.”
“To make nanomanufacturing practical, we have to optimize time and scale,” Xu said. “Creating a single nanostructure in a lab, over several days, just doesn’t scale. With this technique, we can make nanoscale 3D printing practical for biomedicine, microrobotics, optics, consumer products, and more.”
The team also includes Liang Pan, Associate Professor of Mechanical Engineering; and Bryan Boudouris, Professor of Chemical Engineering. All research takes place at the Birck Nanotechnology Center. This work was supported by the National Science Foundation through their Scalable Nanomanufacturing Program, award number 1634832.
Writer: Jared Pike, jaredpike@purdue.edu, 765-496-0374
Source: Xianfan Xu, xxu@purdue.edu, 765-494-5639
ABSTRACT
Paul Somers, Zihao Liang, Jason E. Johnson, Bryan W. Boudouris, Liang Pan, Xianfan Xu
There is demand for scaling up 3D printing throughput, especially for the multi-photon 3D printing process that provides sub-micrometer structuring capabilities required in diverse fields. In this work, high-speed projection multi-photon printing is combined with spatiotemporal focusing for fabrication of 3D structures in a rapid, layer-by-layer, and continuous manner. Spatiotemporal focusing confines printing to thin layers, thereby achieving print thicknesses on the micron and submicron scale. Through projection of dynamically varying patterns with no pause between patterns, a continuous fabrication process is established. A numerical model for computing spatiotemporal focusing and imaging is also presented which is verified by optical imaging and printing results. Complex 3D structures with smooth features are fabricated, with millimeter scale printing realized at a rate above 10-3 mm3 s-1. This method is further scalable, indicating its potential to make fabrications of 3D structures with micro/nanoscale features in a practical time scale a reality.