Printing the Unfinished Block P: Mastering additive manufacturing step by step
Salil Bapat, a research scientist at the Manufacturing and Materials Research Laboratories (MMRL), taught the course ME 496: Introduction to Additive Manufacturing Processes, Equipment, and Fundamentals to undergraduate students this past fall.
“Metal additive manufacturing is one of those new and cutting-edge manufacturing techniques that many students looking for hands-on experience are able to get at MMRL,” Bapat said.
Students in ME 496 were given the challenge of creating an Unfinished Block P with computer-aided design (CAD). The objective was to make the sample lighter and conserve as much material as they could. The catch: they could only alter the base, and the P should still be able to stand. It also needed to easily empty out any excess stainless steel powder after the printing process.
Once the student teams created their CAD drawings, they were given to John DePriest, manufacturing technician at MMRL, where he 3D-printed the structures on a Renishaw AM 400 machine.
MMRL is one of the newer labs at Purdue, hosting the latest in manufacturing machinery and processes while innovating in laser machining, particle coating, roll-to-roll printing, processing and evaluation, and more – all in collaboration with industry and government partners.
One of the lab’s most notable offerings is the ability to 3D print metal through two different approaches. The first approach, called “laser powder bed fusion,” has the machine spread a thin layer of metal powder along a plate and then use a high intensity laser to run over each layer of deposited powder, causing it to fuse together. It then repeats this process layer after layer until the sample is complete. The other approach is “directed energy deposition,” in which powder is shot through a nozzle and at the same time a concentric laser fuses the powder as it deposits. Typically, these processes are done with steels, superalloys, nickel-based alloys, and even reactive powders like titanium, aluminum, and magnesium alloys.
“I always ask students whether they’re familiar with polymer-based 3D printing, and most are,” said Bapat. “A lot of students aren’t familiar with metal printing and that’s what we are trying to change here. With metal printing, you’re able to create more complex design geometries than you are with filament-based polymer printing.”
“The class introduced many new printing technologies to me such as directed energy deposition (DED), material, and binder jetting,” explained Seth Schaefer, mechanical engineering student at Purdue. “Our team created a lattice structure and was able to remove 41% of the overall weight, with about 76% of the base material removed.”
The designs below showcase some of the team’s attempts at the challenge.

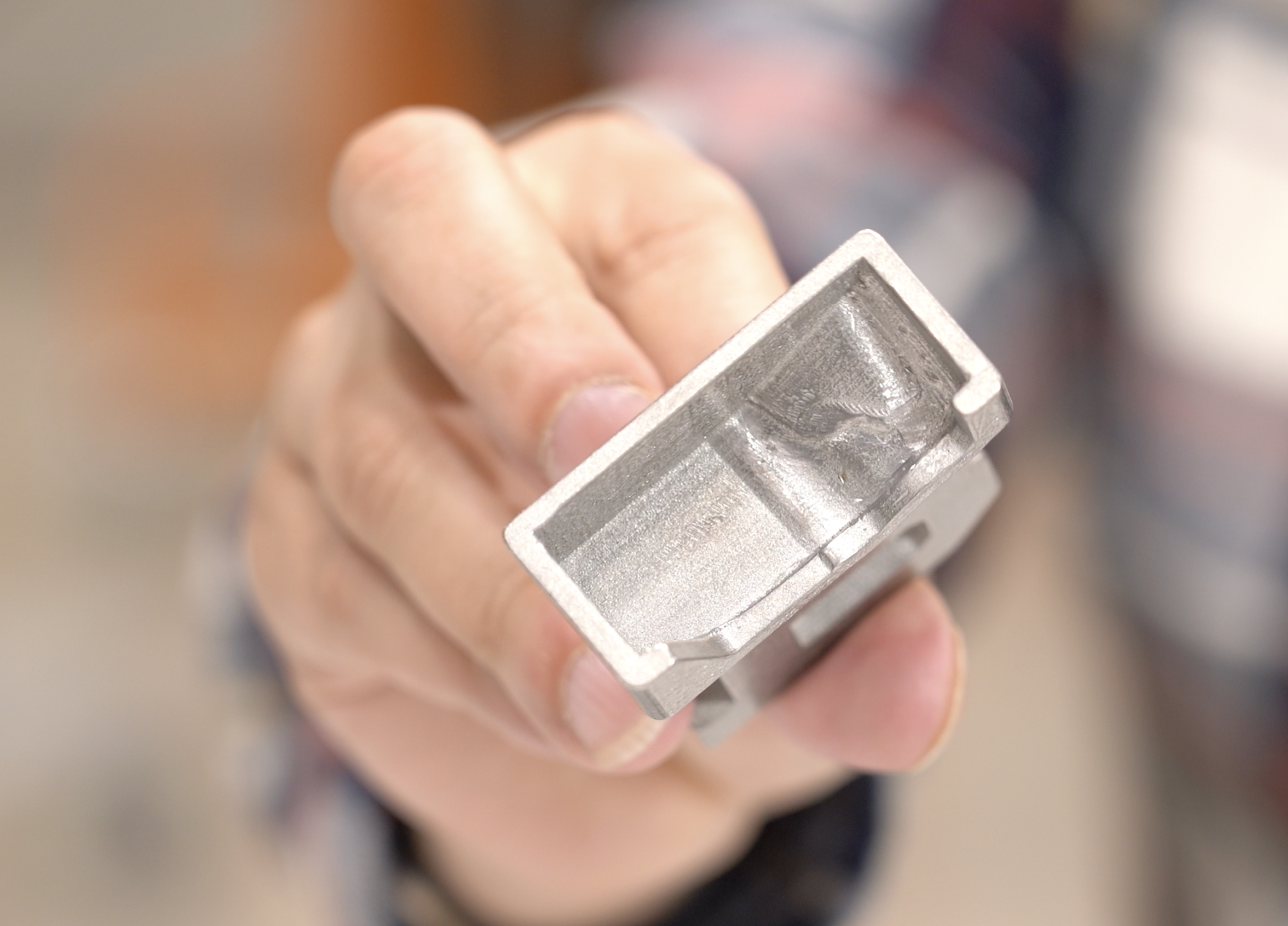
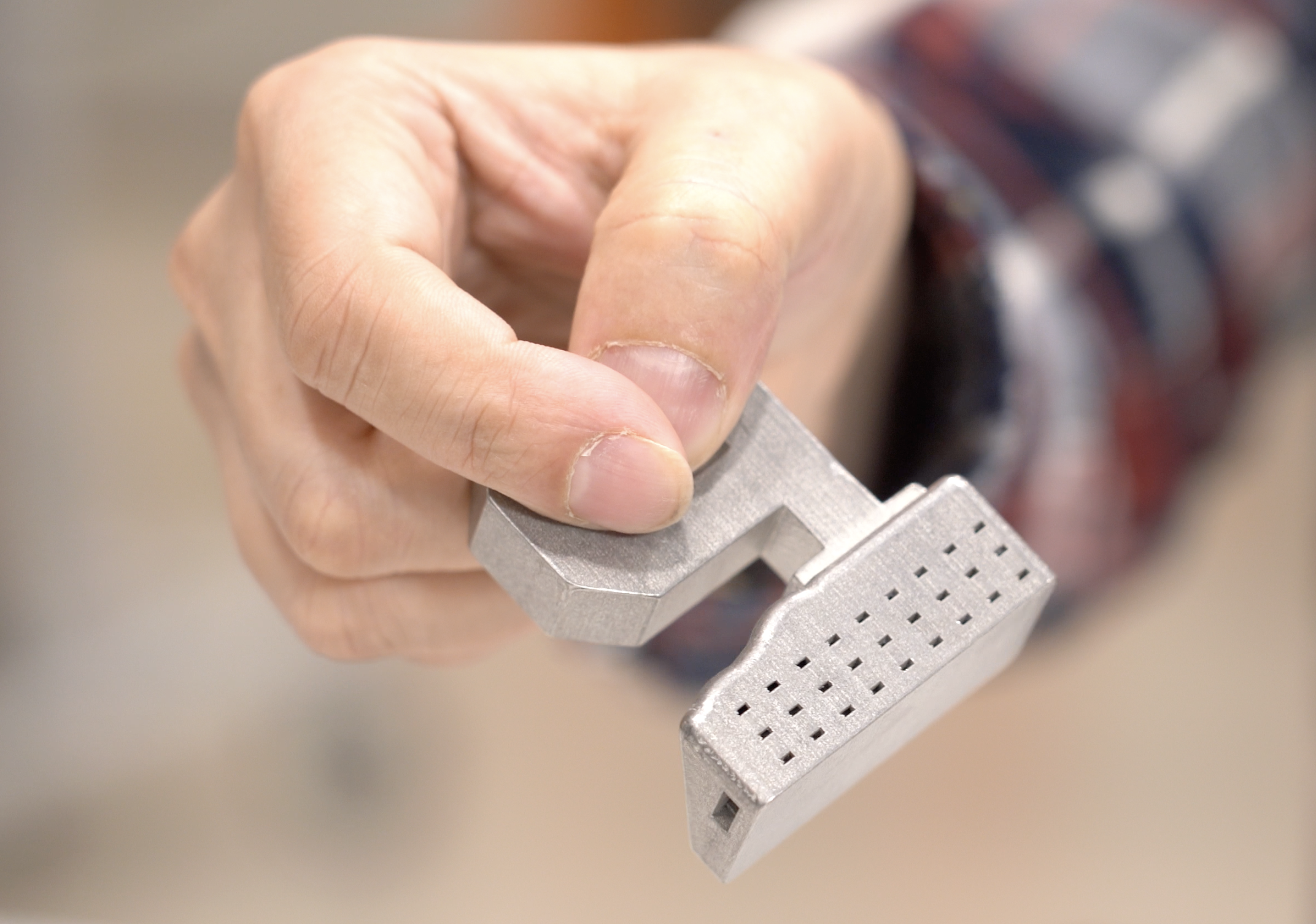
“The class was a great introduction to the science and technology behind additive manufacturing,” said Taj Donthineni, mechanical engineering student at Purdue, “Getting the chance to design a part to print was a unique and memorable experience.”
“A big goal of this class was to create awareness among students, not only in terms of what different metal additive manufacturing techniques there are but also what tools are available to them on campus,” said Bapat.
“This hands-on experience will help students in things like their senior design projects or in any job or internship they acquire,” Bapat explained. “No matter where you go, there’s a good chance you’ll encounter additive manufacturing processes.”
See the Unfinished P mini-sculptures for yourself! The samples are located in a display case in the atrium of the ME building on Purdue’s West Lafayette campus.
Manufacturing and Materials Research Laboratories (MMRL): https://engineering.purdue.edu/MMRL
Source: Salil Bapat, bapat0@purdue.edu
Writer: Julia Davis, juliadavis@purdue.edu