Swimming microrobots achieve record speeds, thanks to microscale 3D printing
“We’ve been working on mobile microrobots for about 10 to 15 years – how to design them, how to make them, and how to control them, and ultimately how to use them,” said David Cappelleri, Professor of Mechanical Engineering. “Because these robots are very small, we can’t attach a battery or any other kind of internal power source. So we power them externally, using magnetic fields.”
Cappelleri’s team have built microrobots that can tumble through a live colon, and they are also working on robots that can deliver a targeted medication payload. Their next challenge? Swimming robots.
“We are now developing some more advanced microrobot prototypes,” said Cappelleri, “where they aren’t just rigid objects, but can deform and change and adapt to their environment.”
Their team’s most recent microrobots include a hard magnetic head, and a soft hydrogel tail in a helix shape – mimicking the swimming behavior seen in bacteria, sperm, and other biological phenomena. Utilizing 3D printing to manufacture the tail with alternating soft-and-hard regions of hydrogel, they’ve enabled adaptive behavior for the robots, based on different fluid environments. They call it the Helical Adaptive Multi-material MicroRobot (HAMMR).
Their research has been published in IEEE Robotics and Automation Letters.
“Hydrogels are soft materials that react with water in different ways, depending on different stimuli,” said Liyuan Tan, a Ph.D. student in Cappelleri’s lab, who authored the research paper. “Some hydrogels will expand like a sponge; others are hydrophobic, meaning they repel water. If you place these different hydrogels in an alternating pattern, they will twist and form a helical shape, which helps the robot to locomote more quickly.”

But there’s a problem. Hydrogels are generally soft, while the magnetic head is generally hard. How do you connect them, at such small scales? “We came up with the idea of combining two different micro-fabrication techniques,” said Tan. “The head is created using photolithography, which is a traditional method of fabricating hard microscale structures. Then for the tail, we use a 3D printing technique called two-photon polymerization, which we can do with the Nanoscribe Photonic Professional GT2.”
Fabrication occurred at Birck Nanotechnology Center in Purdue’s Discovery Park, one of the most advanced micro- and nano-fabrication labs in academia.
“We’re talking about 10-to-50 microns wide for these objects, which is about the width of a human hair,” said Cappelleri. “You can’t just use a nut and bolt to connect these two halves. Any kind of impurity or speck of dirt or stray magnetic particle will ruin the robot. Using the Nanoscribe 3D printer, we’ve been able to not just connect the two halves, but to customize the designs of the helical tail for different environments.”
They experimented with different angles for the alternating hydrogels, as well as different environments of water and isopropyl alcohol. Once they hit upon the right combination, the swimming speed of the HAMMR exceeded their expectations. “This robot achieved a velocity of 8.1 body lengths per second,” said Tan, “which is the fastest reported velocity for any adaptive swimming microrobot.”
For this specific robot, 8.1 body lengths is about 2 millimeters per second, which doesn’t sound very fast. But if this tiny robot were translated to the scale of, say, a 7-meter torpedo, it would be one of the fastest objects to ever travel underwater.
Of course, the end goal for HAMMR isn’t speed, but precision. “The first step was being able to fabricate these robots and get the best locomotive performance in a fluidic environment,” said Cappelleri. “And because they are adaptive, we can change their geometry to go through small constrictive areas like blood vessels, or the reproductive tract. Now that we’re there, our goal is to develop therapeutic applications. Can we load a drug on to the robot? Can we use it to perform a biopsy? We’re looking forward to functionalizing these robots for many different capabilities in the human body.”
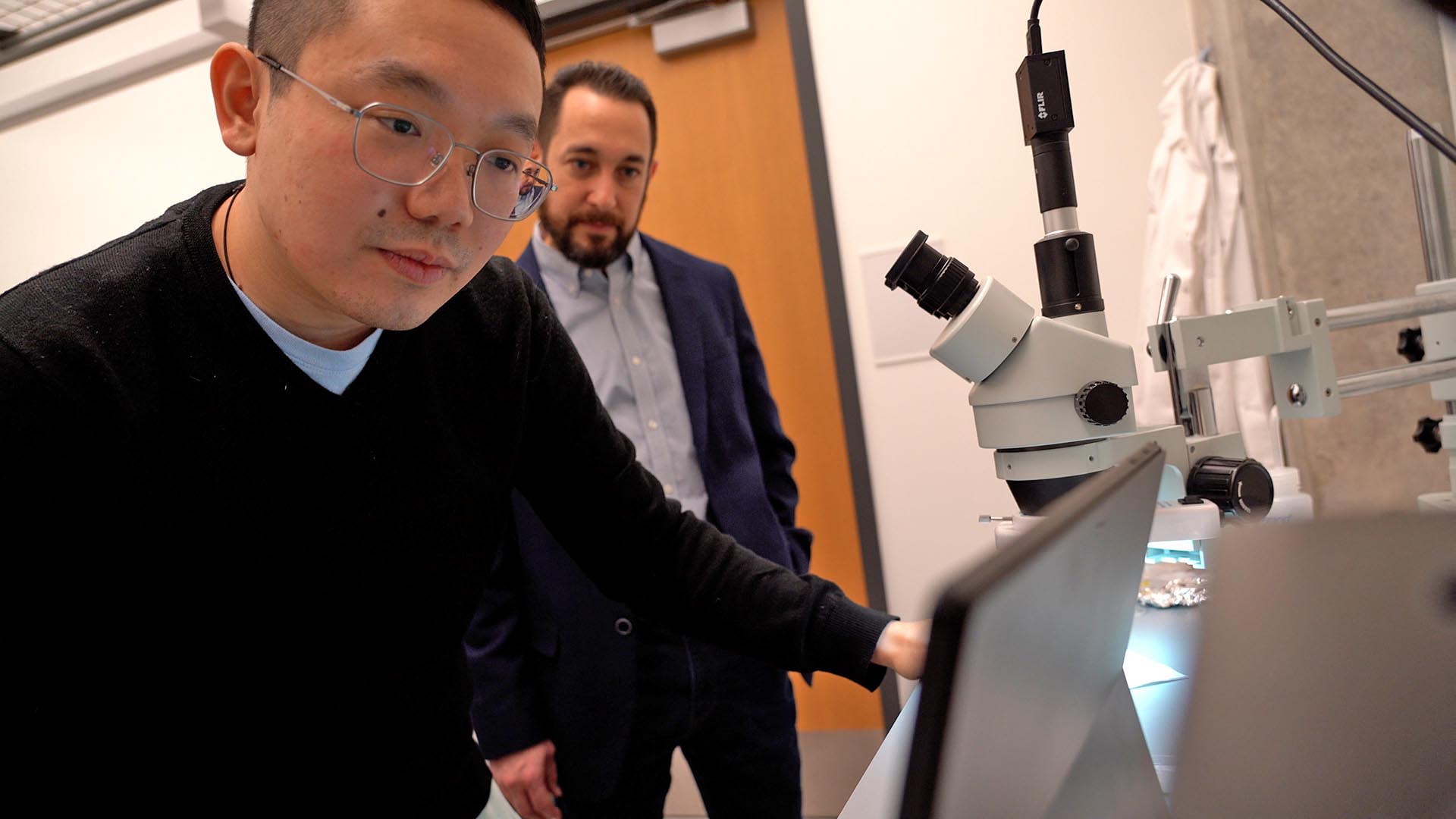
Writer: Jared Pike, jaredpike@purdue.edu, 765-496-0374
Source: David Cappelleri, dcappell@purdue.edu, 765-494-3719
Design, Fabrication, and Characterization of a Helical Adaptive Multi-material MicroRobot (HAMMR)
Liyuan Tan and David J. Cappelleri
https://doi.org/10.1109/LRA.2023.3242164
ABSTRACT: Adaptive locomotion is an advanced function of microrobots that can be achieved using smart materials. In this paper, a responsive hydrogel is utilized as a smart material and used to fabricate Helical Adaptive Multi-material Micro-Robots (HAMMRs) with deformable tails to achieve adaptive locomotion capabilities. Moreover, a novel fabrication method is proposed to realize these types of helical microrobots with enhanced swimming performances by taking advantage of a strong magnetic head and deformable tail. The deformations of different tail designs and the fabricated microrobots are tested in different solvents. The swimming performances of the swimming microrobots are investigated experimentally under a rotating magnetic field and verified with theoretical calculations. The HAMMRs show significant deformations upon stimulation and changes in swimming performance which are in agreement with the scaled calculation result. Finally, the HAMMRs present an enhanced mobility with a highest published translational velocity for an adaptive swimming microrobot of 8.1 body length per second.