Supercomputer allocation enables Purdue hypersonics research

As part of the program called Innovative and Novel Computational Impact on Theory and Experiment (INCITE), the DOE awards time on its leadership-class supercomputers at both Argonne and Oak Ridge National Laboratories, which enable researchers to accelerate discovery and innovation. Purdue’s entry in this competitive program was recognized both for its timely research subject and its robust software infrastructure.
“This is huge for both simulation and experimentation,” said Carlo Scalo, associate professor of mechanical engineering, whose research focuses on nonlinear acoustics, compressible turbulence, and hypersonics. “We create very complex models that sometimes take weeks or months to calculate. But we also run physical experiments, which generate mountains of data that also need to be processed.”
Matteo Ruggeri, an aeronautics and astronautics Ph.D. student in Scalo’s lab, studies the aerodynamics involved in hypersonic vehicles. His large-scale numerical simulations are revealing the fundamental mechanisms that enable the passive control of hypersonic boundary layer aerodynamics via engineered surfaces, with the goal of reducing drag and turbulence without needing to actively adjust or move any part of the vehicle.
This was put to the test in a physical experiment at the Air Force Research Laboratory’s (AFRL) Mach 6 Ludwieg tube in Dayton, Ohio. A flat plate, roughly 5 inches wide and 12 inches long, contained a sample of the porous material. It was then subjected to 100-millisecond bursts of hypersonic air, reaching roughly six times the speed of sound. Similar tests were run on a control plate without the porous material. Ruggeri analyzed the data with the help of Purdue’s Rosen Center for Advanced Computing.
His results have been published in AIAA SCITECH, AIAA Aviation, and Experiments in Fluids.
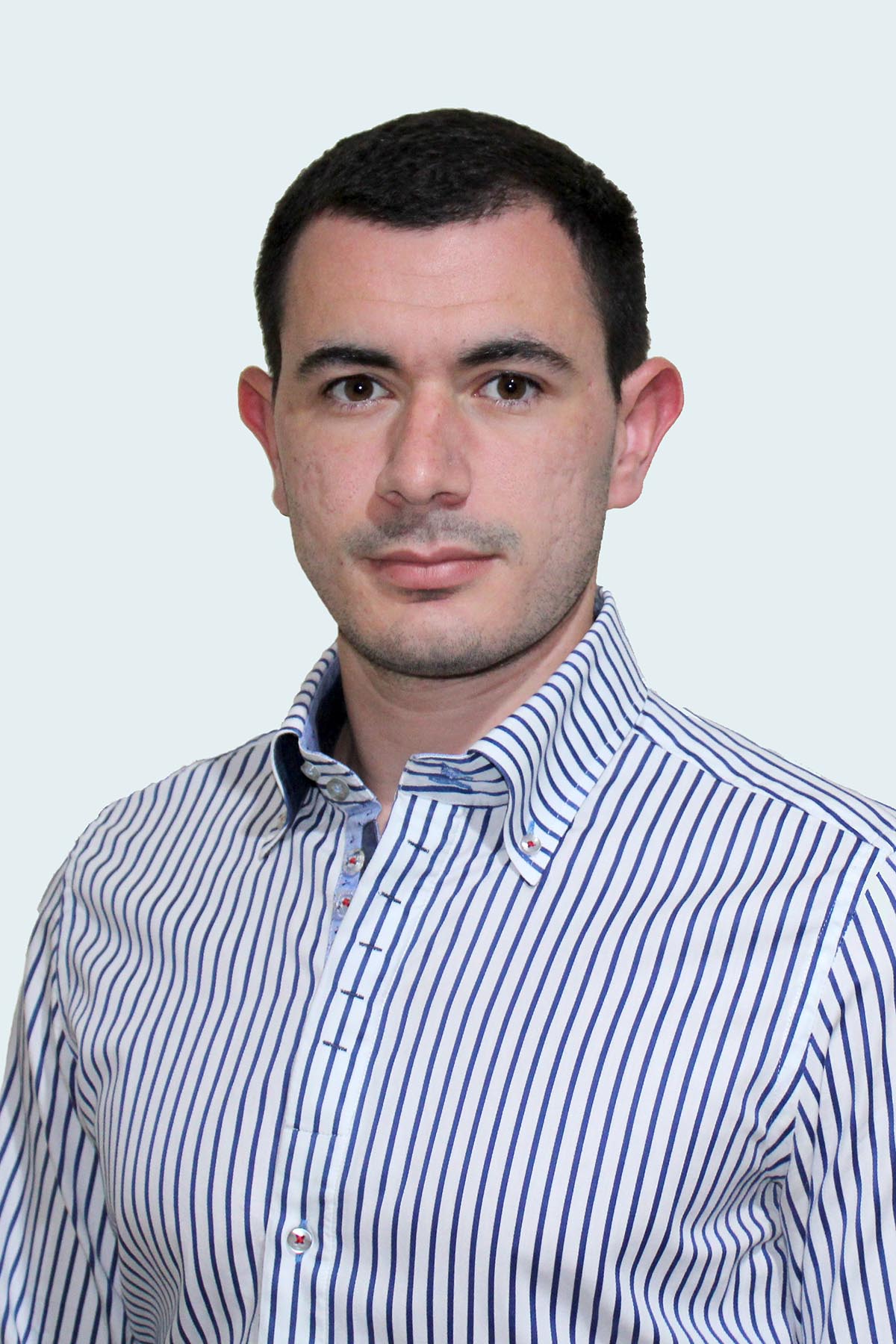
Based on those results, Ruggeri decided to try a different approach. “Inspired by previous results, we wanted to use a different surface pattern to delay the transition to turbulence,” Ruggeri said.
To design this new form of control, Ruggeri started a new large-scale computer simulation with a new surface treatment to manipulate the aerodynamic energy at hypersonic speeds. A new flat insert was manufactured based on those simulations. Through the financial support of the AFRL Regional Network’s Midwest Hub, Ruggeri was able to return to Dayton and conduct more hypersonic testing with the new passive control strategy.
“My simulations predicted that this design would control certain frequencies that naturally occur in a hypersonic boundary layer,” Ruggeri said. “And according to early results from the Air Force, that’s exactly what happened.”
“We were all thrilled,” Scalo said. “I am continuously stunned by Matteo’s talent, from his physical intuition to his incredibly fast implementation and execution of new computational models. We joke that Matteo is like a hypersonic boundary layer whisperer!”
With the experiment concluded, much calculation remains. Even with Purdue’s supercomputing capabilities, hypersonic modeling and analysis is extremely difficult because of the immense amount of detail required to get accurate results. That’s why the recent DOE supercomputer allocation will be such a game-changer.
“As important as computer modeling can be, there’s nothing that beats experimental data,” Ruggeri said. “The data generated in a half-second test could be twenty times more than what we create in a computer simulation that takes months. There’s no way we could match the wealth of that data with our model without the support of DOE’s supercomputers.”
The team plans to use this allocation to validate their results (which were limited to two dimensions), but also to simulate future results in three dimensions. “Seeing this hypersonic flow in three dimensions will bring us closer to practical results, because ultimately what matters is reducing drag on a vehicle,” Ruggeri said.
“I’m so proud of Matteo and his work,” Scalo said. “His modeling led to a brand-new experiment, which led to more modeling, which led to another experiment, and so on. Eventually our blue-sky goal is to simulate a whole vehicle. His work is bringing us closer to the reality of viable hypersonic vehicles.”
Writer: Jared Pike, jaredpike@purdue.edu, 765-496-0374
Source: Carlo Scalo, scalo@purdue.edu
Matteo Ruggeri, mruggeri@purdue.edu
About Purdue Innovates
Purdue Innovates ensures startups with significant research can access mission-critical resources to start, de-risk, scale and fund their world-changing innovations. With support from Purdue Innovates, Scalo’s startup, HySonic Technologies, LLC, applied and received Phase I SBIR awards from the U.S. Navy in 2019 and 2021.
Purdue Innovates is a unified network at Purdue Research Foundation to assist Purdue faculty, staff, students and alumni in either IP commercialization or startup creation. As a conduit to technology commercialization, intellectual property protection and licensing, startup creation and venture capital, Purdue Innovates serves as the front door to translate new ideas into world-changing impact.
For more information on licensing a Purdue innovation, contact the Office of Technology Commercialization at otcip@prf.org. For more information about involvement and investment opportunities in startups based on a Purdue innovation, contact Purdue Innovates at purdueinnovates@prf.org.