AAE's Alexeenko co-leads research hub to transform freeze-drying process used to make lifesaving drugs, preserve food
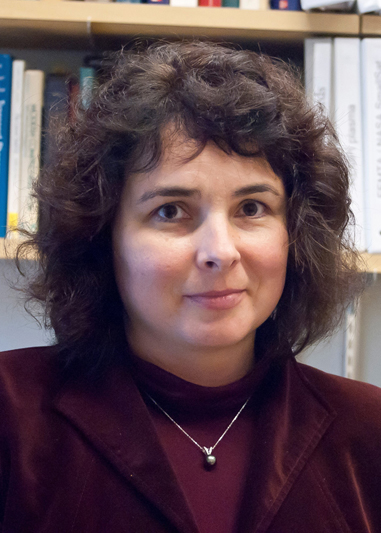
A consortium of researchers, industry members from pharmaceutical and food processing sectors, as well as equipment makers and others, are working together at the Advanced Lyophilization Technology Hub, or LyoHub, at Purdue to modernize a process that has not changed fundamentally in 70 years even though it has a worldwide annual market of about $16 billion.
“Our ultimate goal is to develop a new type of process that will make lyophilization obsolete,” said Elizabeth Topp, professor of industrial and physical pharmacy. “I hope the conventional inefficient process will be supplanted by something that can be better controlled and is much more efficient in terms of time and energy.”
Lyophilization removes water from a product after it is frozen and placed under a vacuum, converting the solid, frozen water directly to vapor without passing through a liquid phase. This process is known as sublimation. The process is used to increase the stability and shelf life of pharmaceutical products while keeping their chemical integrity. It also makes food easier to transport while preserving the food’s nutritional quality, taste, shape and size. The process was developed during World War II to preserve blood plasma and medications such as penicillin without the need for refrigeration.
The problem with lyophilization, however, is that it is time-consuming, expensive and has an energy efficiency of less than 5 percent. A lyophilizer is run in batches, like someone baking cookies in an oven, compared with other manufacturing processes that are run continuously with raw materials being fed into one end and finished products rolling out the other. The batch system gives producers less control and poses challenges to ensuring uniformity, said Topp, who co-leads LyoHub with Alina Alexeenko, a Purdue professor of aeronautics and astronautics.
Despite being less efficient, pharmaceutical companies are increasingly dependent on lyophilization because of the rise of biologics, which include a wide range of products such as vaccines, blood and blood components, somatic cells, gene therapy, tissues and recombinant therapeutic proteins. Lyophilization is used to stabilize products susceptible to physical and chemical degradation.
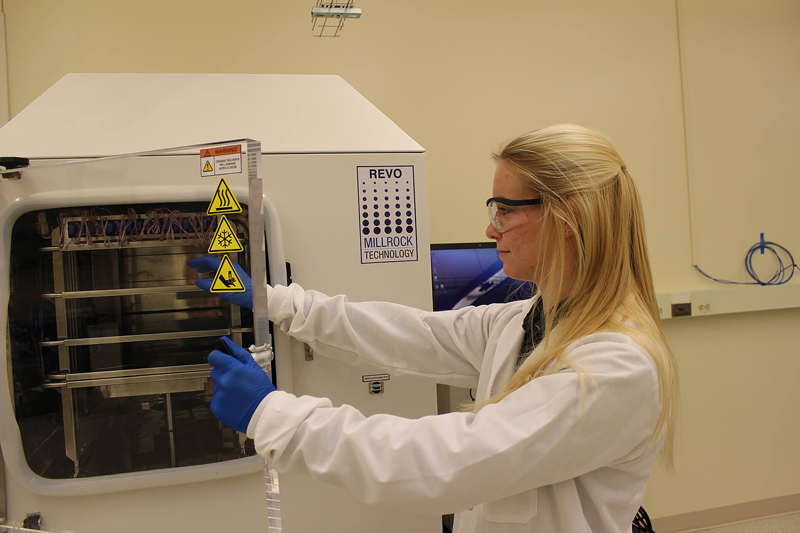
“We have very high-tech products that depend on this very old-fashioned process. The question before LyoHub is: How do we advance this technology so we have a faster, more efficient way of getting stable, dried products on the pharmacy side?” Topp said. “Also, how can we do this on the food side in an arena where the margins are so much lower than in pharma? How can we advance the technology so everybody wins?”
Although replacing lyophilization is the ultimate goal, LyoHub also is working to improve each step in the lyophilization process in the meantime. Researchers are working to develop sensors that are less bulky and to advance process analytical technology.
LyoHub, which is based in the Birck Nanotechnology Center at Purdue’s Discovery Park, announced in September a 10-year technology road map to identify needed improvements and ways to get there. The overall goal is high-quality products that are readily available at a lower cost.
Finding a replacement for lyophilization could help overall public health. Although many food and pharmaceutical products could not be commercially viable without lyophilization, some pharmaceutical companies don’t produce drugs that require lyophilization, Topp said.

“The scary downside from the standpoint of the public is: What if no one picks up that molecule?” Topp asked. “What if it is never developed? That’s a whole lot of lost investment that never benefits patients. We have lots of patients who could use help.”
The consortium also wants to improve communication with regulatory agencies while developing industry standards. Pharmaceutical companies rarely make changes in the drug manufacturing process after it has been approved by the Food and Drug Administration because they don’t want to go through the laborious qualification process again.
LyoHub also is working to create “best practices” standards to set scientifically sound and industry standard approaches for issues such as equipment qualification, batch acceptance, process validation and cleaning validation. Those standards are needed because companies often take overly conservative approaches that lead to product rejection and lengthy delays in the startup of new equipment and facilities, Topp said.
“We think everyone can win by working together. We understand that there will be areas where members of the consortium won’t want to share proprietary information. But it doesn’t make sense for us as a group to answer the same question with five different companies separately. It’s much more efficient and cost-effective for them all to pool resources and share the results when possible,” she said.
Purdue researchers have filed patent applications related to lyophilization through the Purdue Office of Technology Commercialization.
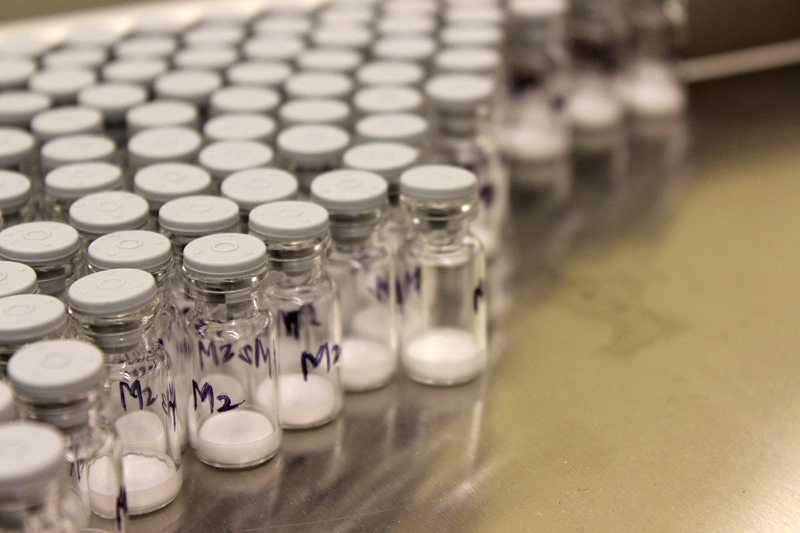