ECE team collaborates with NASA on impact sensors for spacecraft
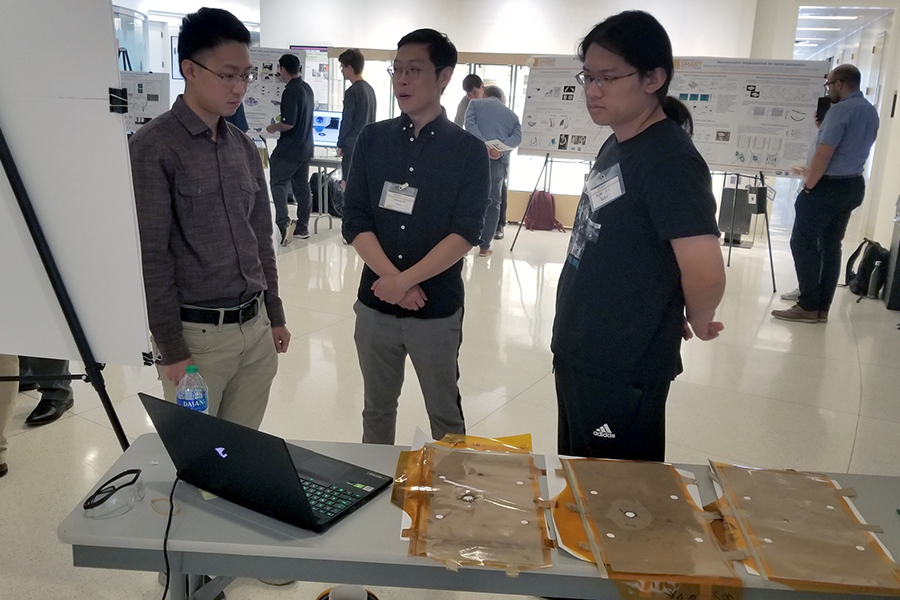
When a team in the Elmore Family School of Electrical and Computer Engineering was developing new scalable impact sensors, they had no idea the devices would be launched to the International Space Station (ISS).
Their work was well under way when scientists from NASA’s Jet Propulsion Laboratory (JPL) took a keen interest in the sensors’ potential for use in spacecraft health monitoring against micrometeoroid and orbital debris (MMOD) damage. Specifically, they were interested in a lightweight, low-power product that could be scaled up and simply designed — all at a very low cost.
“This was not a technology designed specifically for space, but because of the low weight and very flexible platform, it was well adapted for it,” said Ali Shakouri, ECE professor and co-director of the Scalable Manufacturing of Aware and Responsive Thin Films (SMART) Consortium.
Punnathat “Tent” Bordeenithikasem, materials technologist at JPL, first met Shakouri in 2019 during a visit to Purdue through a JPL internal initiative, the Center for Academic Partnership (CAP) fund, which is used to organize workshops for JPL personnel to form collaborations with university partners.
“The CAP involved a tour of the Birck Nanotechnology Center, so that’s where I got to see the cleanroom and manufacturing capabilities. I was very impressed, especially with the roll-to-roll printing technology for flexible electronics,” Bordeenithikasem said. “When the Mars Sample Return campaign had the desire to develop sensors to detect MMOD, we partnered with Purdue to develop a new technology demonstration.”
A statement of work was drafted, a formal collaboration was established, and the Purdue team got to work.
ECE PhD students Yuhang Zhu, Yufei Liu and Nathan Conrad — under the direction of Saeed Mohammadi, an ECE professor who conducts projects through SMART — used JPL funding to create a large-area, high-density sensor system fabricated from conductive metal ink screen-printed on flexible Kapton using SMART’s roll-to-roll manufacturing at the Indiana Manufacturing Institute inside Purdue Research Park.
Purdue is unique in its ability to produce large-scale flexible sensor systems, Shakouri said. This was especially attractive to JPL since its intention was to use the sensors as spacecraft shields.
“Detecting and evaluating MMOD damage is crucial, especially for long-duration deep space expeditions as well as for human missions,” said Douglas Hofmann, senior research scientist and principal at JPL.
It’s imperative to protect precious space cargo, like samples being returned from Mars, from dangerous MMOD impacts, he added.
“I was extremely thrilled when I learned that we were going to collaborate with NASA,” said Liu, who was responsible for the design of the row and column readout drive boards and all measurement and analysis tasks related to changes in sensor data. “I was also somewhat nervous. Having never undertaken a project like this before, I was concerned about the potentially stricter design requirements for sensor systems on spacecraft.”
To prepare the sensors for evaluation, they were integrated into a low-density, two-wall Whipple shield.
“We tested these sensors by shooting them with aluminum spheres at up to 7 kilometers per second using the hypervelocity gun range at White Sands Test Facility,” Bordeenithikasem said. “When the sensors were implemented at different layers along the thickness of the Whipple shield and/or spacecraft walls, the energy of the MMOD impact could also be quantified.”
The method was very attractive as a simple electrical measurement to quantify kinetic energy of impact debris.
When NASA finished the ultra-high-speed particle impact tests, Liu was in charge of processing and analyzing the test sensors sent back to Purdue and conducting measurements and organizing the data.
“I also measured and analyzed special damage points that had not been encountered in the lab environment,” he said.
The Purdue Engineering team designed the sensors so that puncture holes on the vast surface area of the spacecraft could easily be detected and quantified.
“JPL wanted to know how big that hole is and where it is so that they can assess whether the mission should be aborted and not brought back to Earth,” Mohammadi said.
The technology can detect damage in real time while reducing equipment weight and minimizing the space it occupies inside a spacecraft, Liu said.
“Additionally, it can estimate the impact force based on the area of damage, thereby inferring internal damage to the spacecraft. This assists ground control personnel in determining whether the mission should continue,” he said.
The testing at White Sands in New Mexico showed some interesting properties at hypervelocity speed, Mohammadi said.
“We were able to quantify the ballistic holes in the sensor, but we also saw additional damages due to the shock waves in the flexible substrate. Mounting and packaging of the sensor in the spacecraft will be important,” he said.
The results of the team’s testing recently were published in an Elsevier paper, for which Liu wrote the description of the overall design of the sensor system, sensor readout, data readout after the high-speed particle test and part of the schematic diagrams. Liu, along with Hofmann, Bordeenithikasem, Shakouri, Mohammadi, Zhu and Conrad, are listed as co-authors on the paper.
The project’s frosting on the cake came on March 14, when two Kapton MMOD sensors that Purdue and JPL developed together were launched on SpaceX CRS-27 and placed on the exterior of the Materials International Space Station Experiment (MISSE) 17. Daily, they are being tested during 16 thermal cycles, including ultraviolet exposure, radiation and atomic oxygen exposure at low earth orbit.
“It’s great to see NASA testing the roll-to-roll printed technology outside the ISS to see how long it’ll last,” said Conrad, who worked on proof-of-concepts for various sensor implementations and then with system design and selection of individual components. “The technology is a very low-mass way to verify the integrity of a spacecraft.”
After the panels return to Earth, JPL will send them to Purdue for additional characterization, Shakouri said. NASA also will scrutinize the effectiveness of the sensors for future use.
“We will see if they decide they want to put this on their mission to Mars or not,” Mohammadi said. “They haven’t really made that decision yet since the sensors are still on the Space Station. If they decide to take this technology and rely on our facility, we can actually make these at scale at Purdue. In terms of electronics, we designed them so that they will be perfectly compatible with what NASA uses for communication and power on their spacecraft missions.”
Zhu — who designed and fabricated the sensors, conducted and executed the proof-of-concept experiments, and delivered the samples to JPL for hypervelocity testing — was pleased with what the team accomplished.
“I believe this is a revolutionary technology for space exploration. This technology can overcome every constraint of the conventional method — an on-board camera with blind spots, high power, and a low coverage area. We hope the samples on the ISS go well and that we can further collaborate with NASA,” Zhu said.
Recounting his interactions with JPL, Liu appreciated the professionalism extended by Bordeenithikasem and Hoffman. “The issues they raised during the project provided a lot of assistance in improving and perfecting our product.”
Conrad agreed.
“The NASA folks were great,” he said. “They have a very wide variety of talent; there were subject matter experts for nearly every issue we ran into.”
Bordeenithikasem commended Purdue’s research facilities and their multidisciplinary benefits for Purdue students.
“I personally believe the collaborative nature and the way Birck is set up to encourage cross-pollination between different research groups and research fields is very unique and also very helpful for the students’ future careers,” he said.
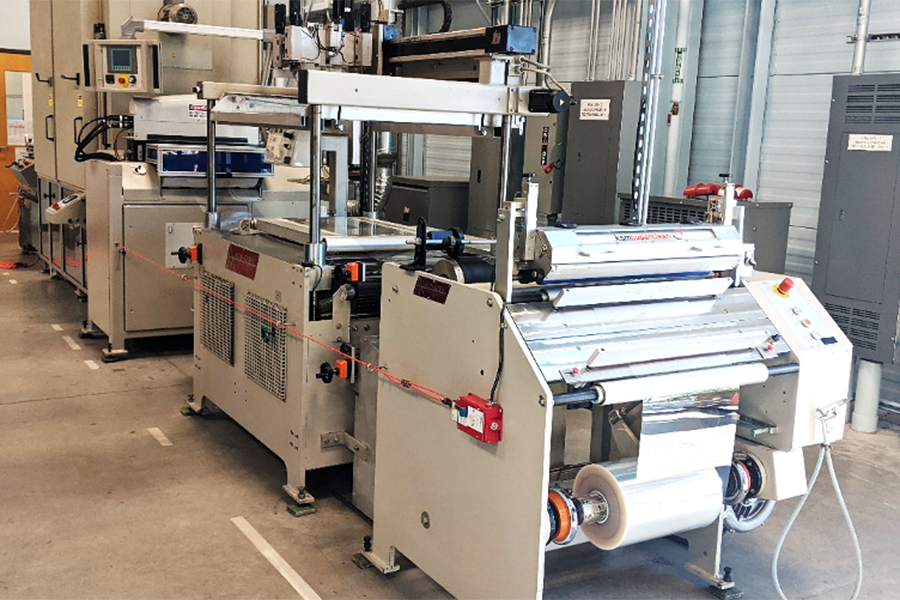