Graduate Studies Add Depth to Alums' 3-D Manufacturing Vision
Author: | William Schmitt |
---|

Two friends who earned their master’s degrees in Aerospace Engineering found the support they needed from the Purdue community in their visionary, resilient trek to make products “smarter” through a company they have named Tri-D Dynamics. They’re now designing and building equipment for a next generation of metallic components that offer connected capabilities and efficiencies for such industries as energy, construction, mining and autos, as well as aerospace.
Purdue grads Deepak Atyam and Alexander Finch, along with co-founder Jesse Lang, are pioneers aiming to transform key aspects of technology and materials with their venture’s “Cold Metal Fusion” approach. Cold Metal Fusion is a powder-based additive manufacturing technology where metal particles are sprayed faster than the speed of sound to form structural parts and coatings. Thanks to advances they pursued in the past several years at Purdue’s College of Engineering, they expect their innovation, using industrial-scale 3-D printing, to boost speed and sustainability on factory floors nationwide.
“We can’t wait for the day when we see a product out there and we know that it was made with our process,” said Finch, who received his master’s degree in 2017. Implementation anticipated over the next several years will fulfill a dream that helped propel a collaborative friendship with Atyam beginning in 2011. The two met as undergraduates at the University of California San Diego.
Back then, they joined in a team effort, led by Atyam, to develop additive manufacturing of rocket engines. Their work resulted in a successful engine test. Industry interest grew in light of new prospects for space exploration, and they said to themselves, “Maybe there’s a business we can create out of this,” Finch recalled in an interview.
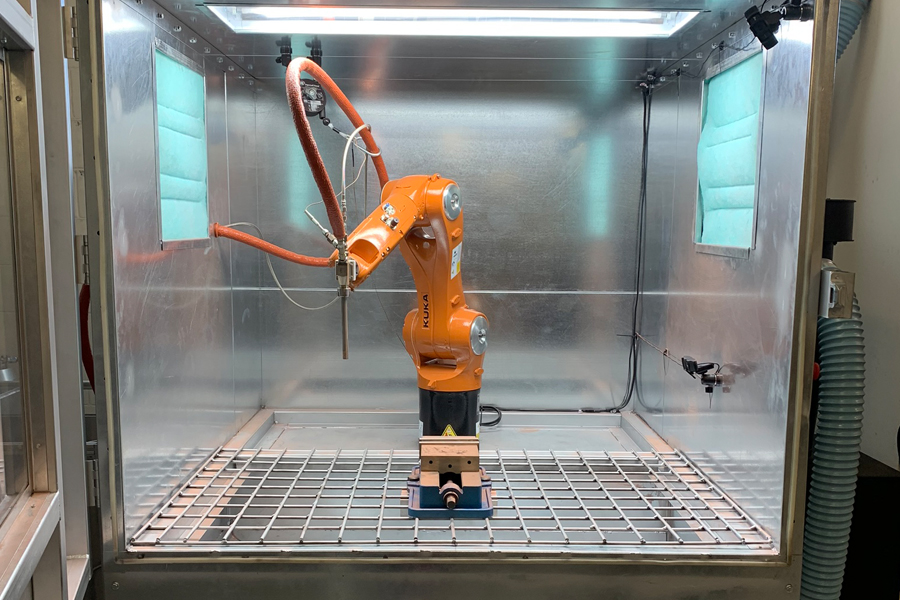
The friends knew they needed more education and Purdue could give them the credibility of world-class expertise in aerospace engineering, so they came to West Lafayette for graduate study. They established a business for building rocket engines on a small, customized scale, and they sought guidance from the Purdue Foundry, which provides instruction and support for entrepreneurial students.
The Foundry helped them receive funding from the National Science Foundation (NSF) to assess their plan’s viability. They learned that market demand would fall short of their expectations, but they discovered that Cold Metal Fusion printing holds potential far beyond the rocket engine sector: It allows for metal to be added onto other materials, allowing industries to create big, multi-material components and other items efficiently and flexibly.
“You can get some pretty cool applications from that,” Finch said. Manufacturers could print electronics into structures because the temperatures involved would not damage the electronic components used in the printing of parts.
Purdue’s extensive expertise and resources served the students well. A group of alumni called the Silicon Valley Boiler Innovation Group provided mentors. Atyam and Finch needed to show their own flexibility, modifying their initial rocket-engine dream.

The duo had entered the University’s largest contest for entrepreneurial plans, the Burton D. Morgan Business Model Competition, and had won $50,000 in cash and services. They made the pivot from rocket engines to a grander vision based on Cold Metal Fusion. They saw that manufacturers could, more easily and inexpensively, make products incorporating artificial intelligence and other digital strengths. industry innovators could use existing materials, or materials they designed from scratch, incorporating metallic sensors and electronics.
Imagine smart infrastructure, such as pipelines, that can adjust to data about changes in the environment or operational malfunctions or ways to increase sustainability.
Finch said he and Atyam imagined “a living, breathing structure with a nervous system that transmits information.”
That is now the vision for Tri-D Dynamics. These two Purdue alumni have raised seed money from investors to start initial construction of Cold Metal Fusion printing equipment, and they are moving toward beta testing customized for clients. This leap ahead in manufacturing technology is expected to open the door for engineers and others to pursue more innovative designs and flexible operations.
Alongside possible boons for high-tech manufacturing, living standards and the profits of Tri-D Dynamics, the two alumni have seen first-hand the boon Purdue programs offer for ambitious students like them.
“Purdue did a really great job of providing support, resources, workspaces, tools and financial resources—and getting smart people together, helping to find sponsorships,” Finch said.
The duo owes much to professors and staff who strive to support leadership among engineers, Finch said. “You don’t get anywhere without people,” Finch said of the campus that served as their steppingstone, “and there were a lot of people to help us out.”
