Designing for efficiency
How have you used your Purdue degrees in the development of this new wing?
My engineering degrees established a foundation in science and engineering that taught me what it takes to design an aerospace vehicle or product. I learned how to dissect complex problems into simpler pieces to find solutions. Within the school we had great facilities, like the wind tunnel, that offered hands-on opportunities to design, build and test. You could put a design through its paces to discover any mistakes.
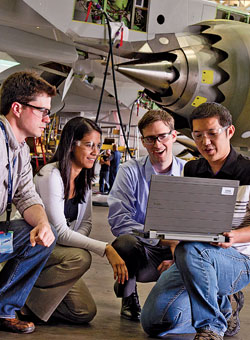
David Loffing, third from left, leads a team of engineers at Boeing.
In lay terms how does this new wing design differ from conventional wings?
Most people wouldn't be able to tell a difference just looking at them. The wing for the 747-8 is built off the technology foundation that former chief engineer for development Joe Sutter and his group used to develop the first 747 back in 1960s.
When we looked to bring this airplane to the 21st century, we utilized new tools and technologies that Boeing applied to the 787 and lessons learned from the 777.
If you look at the wing, you might just see changes to the wing tip but the differences go much deeper than that. Everything from the side body all of the way up to the wing tip has changed utilizing the latest in aerodynamic design and new airfoil technology.
Probably the biggest change to the wing design is integrating the engines and the wing together aerodynamically to optimize the shape and loft of the wing for reduced drag and improved fuel burn performance.
We used computational photodynamics. Back in the day we would have to do all of this design iteration in the wind tunnel. With new tools and processes we can now do this on computers and come out with an even more optimal design.
How will this new design help with better fuel efficiency?
Our world is dependent on commercial airfreight and cargo and not just commercial airliners in the traditional sense. A lot of what we use on a daily basis — from electronics to food — is flown on planes.
Bringing in the new, more efficient 747-8 vehicle to the airlines will improve the lives of those around the world and help our industry become a better global neighbor by reducing fuel burn and carbon emissions in a more environmentally efficient fleet of airplanes.
How long was the process for developing the new wing?
I started on the project when I joined Boeing in 2004. After doing a lot of studies it became apparent that we needed a new wing to go along with this new engine.
Airplanes are highly integrated and we couldn't achieve the efficiencies needed just by swapping the engines. I followed the wing through the product development "paper" idea onto the detailed design phase with first flight in 2010 and delivery in 2011. It took about six years from beginning to end.
As a student, did you see yourself following this career path?
I am now a manager in aerodynamic stability control, managing about 20 engineers. The group is responsible for our aerodynamic simulation modeling for all of our commercial airplanes.
If you had told me in 2004 that I would be a manager in the aero industry, I would probably have laughed. When I left Purdue, I considered furthering my education to take more of a technical path at Boeing, not necessarily a managerial path. Life has a funny way of changing.