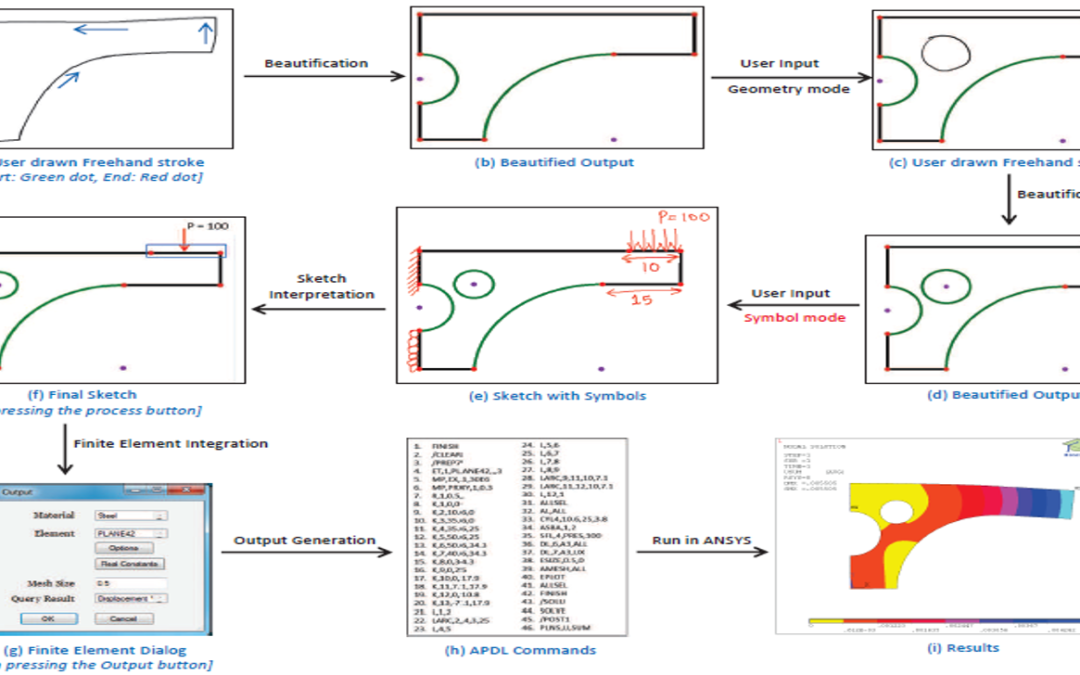
Cecil Piya is a PhD graduate from the school of Mechanical Engineering at Purdue University. Dr. Piya received his BSc in mechanical engineering from Worcester Polytechnic Institute, and earned his Doctorate at Purdue, while working as a graduate researcher in the C-Design Lab under Prof. Karthik Ramani. Here, his research explored novel Human-Computer Interactions and Digital Interfaces that leverage spatial gestures, tangible interactions, and pen-and-touch based media to support virtual 3D product design and shape modeling. In the past he also conducted research in areas such as digital shape reconstruction from 3D point clouds, geometric support for additive manufacturing, feature detection in 3D models, object identification in 2D images, and heat transfer.
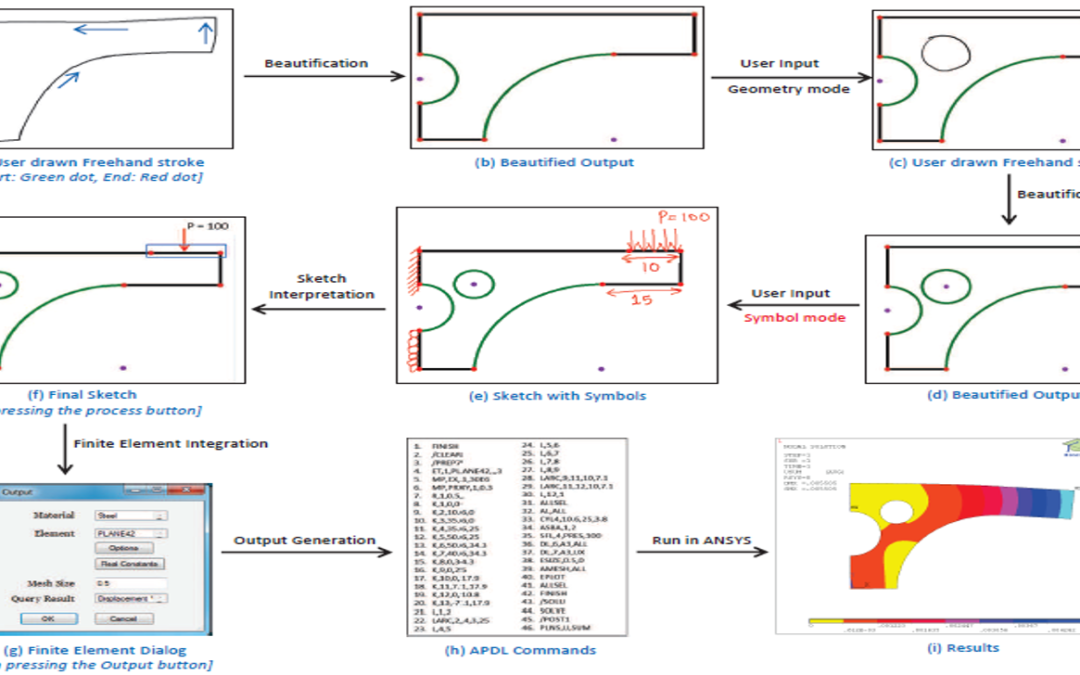
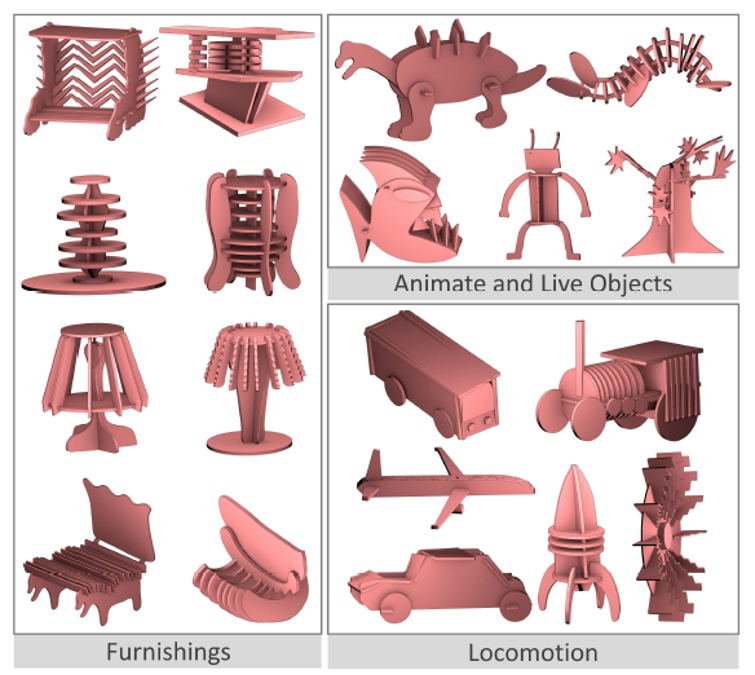
Proto-TAI++: Exploring Perceptually Consistent Creation of Planar Shape Assemblies Through Multimodal Tangible Interactions
We explore tangible 3D interactions that allow for geometric and perceptual correspondence between a midair modality and the 3D elements it controls. To demonstrate our approach, we use a concrete application scenario through Proto-TAI++, a multimodal system using...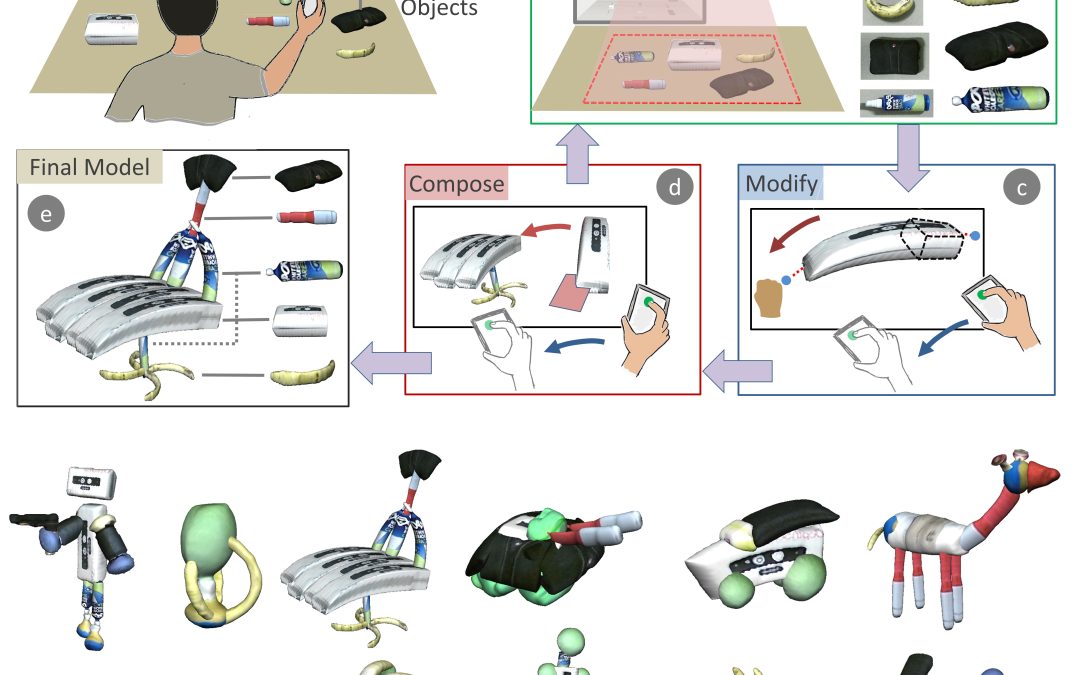
RealFusion: An Interactive Workflow for Repurposing Real-World Objects towards Early-stage Creative Ideation
We present RealFusion, an interactive workflow that supports early stage design ideation in a digital 3D medium. RealFusion is inspired by the practice of found-object-art, wherein new representations are created by composing existing objects. The key motivation...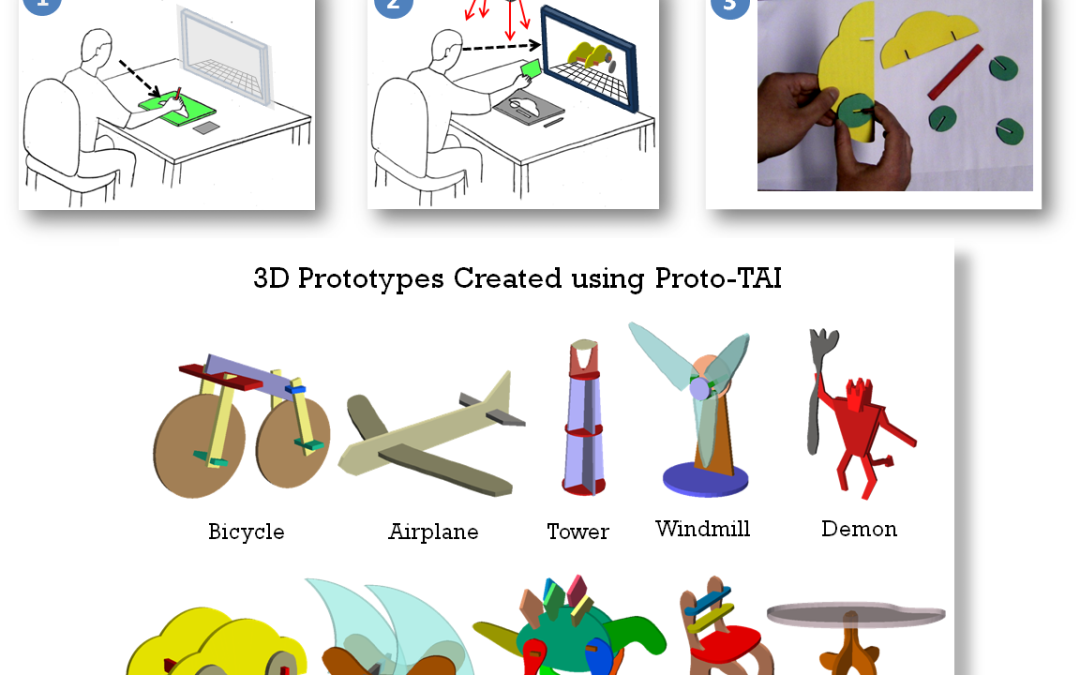
PROTO-TAI: Quick Design Prototyping using Tangible Assisted Interfaces
In the real world, we use our innate manual dexterity to create and manipulate 3D objects. Conventional virtual design tools largely neglect this skill by imposing non-intuitive 2D control mechanisms for interacting with 3D design models. Their usage is thus...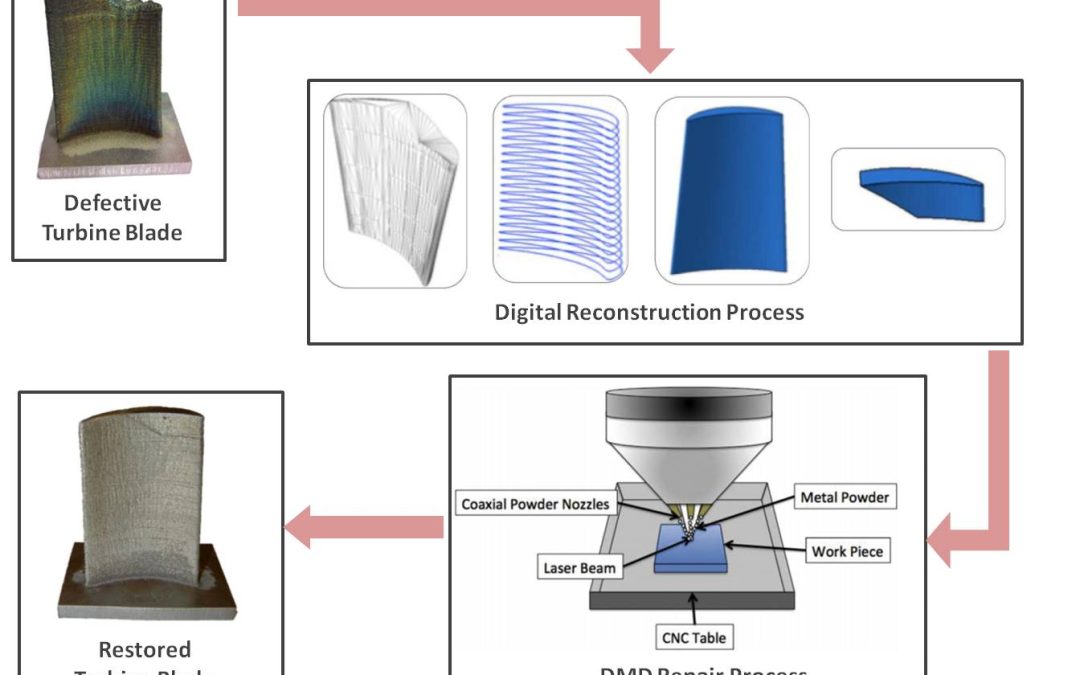