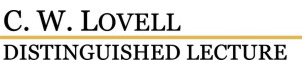
12th C. W. Lovell Distinguished Lecture
Dr. James D. Murff
"Evolution of Offshore Geotechnical Engineering"
The search for and production of oil and gas has been a primary impetus for progress in offshore engineering. The earliest offshore drilling and production structures appeared circa 1900. Initially drilling was carried out on crude, improvised fixed and floating structures in coastal waters, bays, lakes, and bayous. The first drilling out of the sight of land was conducted in 1947 off the Louisiana coast in 18 feet of water. The drill rig operated on a simple, scaffold-like structure supported by sixteen 24 inch diameter steel pipe piles and attended by a large moored barge. The first truly offshore soil boring was carried out from a temporary, bottom founded structure. Drilling structures quickly evolved to the so called jack-up or self-elevating platform as well as floating platforms. The favored permanent production structures, which are the primary focus of this presentation, were steel, space-frame structures supported by battered piles to support the system weight and the large lateral and overturning loads imposed by waves, winds, and currents. Concurrently, the impracticality of using fixed bottom structures for soil borings led to the successful use of a moored work boat with moon pool amidships to carry out the requisite geotechnical boring and sampling.
The almost exclusive use of steel pipe piles as foundation elements focused attention by geotechnical engineers on pile design. Axial capacity of piles was determined using relatively simple alpha methods in clay and friction models in sand using ideas carried over from land practice. The very soft, surficial clay soils at many sites stimulated research on the lateral behavior of piles resisted by weak, non-linear soil supports. Considerable effort was focused on the latter in the mid to late 1950's and early 1960's leading to the beam column models that are still widely used today.
By the early 1970's water depths for production facilities had reached some 300 feet and were increasing rapidly. Foundation requirements demanded larger diameter, longer piles. The large extrapolations beyond land experience and the very limited offshore experience became a concern. This resulted in a number of research programs in the 1970's extending into the 1980's aimed at improving axial pile capacity design methods. This work included advanced modeling of pile installation including pore pressure increases and dissipation (set up); field load tests on pile segments placed at depths and in soils representative of offshore prototypes; and extensive literature searches to develop pile load test data bases to be used to test the reliability of proposed models. These studies resulted in significant improvement in the alpha and friction models although the basic empirical frameworks were maintained. Perhaps more importantly the new research provided a greatly improved understanding of the strengths, weaknesses and applicability of the various design methods. In addition to the above advances, significant improvements were made during this time in applicable geophysical and geotechnical exploration methods.
By the mid 1980's industry had installed what remains the deepest water "conventional" fixed bottom structure, the Bullwinkle Platform in 1350 feet of water. This water depth range is considered a practical limit for conventional fixed bottom structures. The dynamic response of a structure of this height to wave loading begins to create serious fatigue issues. Attempts to hold down the structure period reach a point of diminishing returns since increased stiffness requires increased mass. At greater water depths it becomes much more efficient to employ floating structures with periods greater than the dominant wave periods to mitigate dynamic amplification. A range of floating structure types have been used in deeper water depths including the Tension Leg Platform (TLP), Floating Production Systems (FPS and FPSO), both ship shape and semi-submersible, and SPAR systems. In addition, bottom founded subsea production systems are also widely employed. The floating systems have required a new breed of foundations, deep water anchors capable of maintaining the floater on station for many years.
In general there are three types of mooring systems. Pure vertical tension anchors are required for TLPs. Catenary moorings are conventional ship anchoring systems with widely spaced, multiple mooring lines which are essentially horizontal at the sea bed and as a system provide omni-directional lateral resistance. Taut moorings are a special case of catenary moorings where the mooring line is maintained in sufficient tension to produce constant angles ranging from 25 to 45 degrees or so above the horizontal. These systems create new demands on the respective foundations.
The TLP subjects the anchors to almost pure uplift loading with a significant cyclic component. Most of these systems have used pile anchors however, the cyclic, tension loading regime presents new considerations for pile design. Further, the installation of piles in very deep water has required significant innovation in the development of underwater hammers. A new anchor type, the suction caisson, has been used extensively for both catenary and taut moorings. In this anchor type a large diameter cylinder, open at the bottom and closed at the top, is inserted into the soil by a combination of self-weight and pressure drawdown within the cylinder. The anchor line is attached to a pad-eye at an optimum depth below the soil surface and applies lateral and uplift mooring loads at this point. The suction caisson has required new design procedures for both installation and load capacity estimates. In addition to the various anchor requirements, a wide range of hardware has been deployed on the ocean bottom supported by shallow foundations or mud mats. These range from subsea production systems to pipeline end terminals or manifolds (PLETs or PLEMs), to steel catenary riser (SCRs) bases. These systems generally impose multi-dimensional loading on their shallow foundations typically sitting on very weak soils. Again innovative design methods have been required
The new foundation demands discussed above and the very deep water environment have required concurrent innovations in the development of improved geophysical and geotechnical investigation tools. Conducting a soil boring in as much as 10,000 feet of water is a very time consuming and hence costly exercise and retrieving samples from such depths make sample disturbance a constant concern. This is further complicated by the fact that a deep water mooring may have as many as 16 separate anchor sites to be characterized. These challenges have led to a number of innovations such as use of seabed sampling and in-situ testing equipment as well as the use of jumbo piston cores using self-weight penetration coupled with cone penetrometer testing. These techniques generally require smaller, cheaper support vessels. The use of autonomous, underwater vehicles has greatly improved the efficiency and quality of geophysical data collection. All of these innovations have resulted in the ability to carry out integrated site studies. These bring together the geology and geotechnical aspects of a particular site and greatly improve the ability of the geotechnical engineer to plan and design the mooring system for deep water production systems.
About Dr. James D. Murff
Don Murff was born and grew up in Houston Texas. He graduated from the U.S. Military Academy at West Point in 1963 and served 5 years on active duty with the Army Corps of Engineers attaining the rank of Captain. He served at Ft. Hood Texas, Panama Canal Zone where he received the Army Commendation Medal, and South Vietnam where he received the Bronze Star Medal for Service. In 1972 he received his PhD degree from Texas A&M where he studied Geotechnical Engineering and Engineering Mechanics.
Don went to work for Exxon Production Research Company in the Offshore Division in 1972 where he was involved in research and consulting for Exxon Affiliates worldwide. He retired in 1999 having attained the position of Sr. Research Advisor, one of Exxon's highest technical positions. His professional activities include service on the API Geotechnical Resource Group, which is responsible for developing and maintaining the geotechnical portions of API's Recommended Practice for Design of Offshore Platforms. He served the Group in many capacities including Chairman for 6 years. API awarded him a Citation for Service in 1987 and a 30 year Service Award and a Resolution of Appreciation in 2006. He has been a member of the National Research Council's Geotechnical and Marine Boards, and has been a member and Chairman of the Industry Advisory Committee to the UT/TAMU Offshore Technology Research Center. He served on the Editorial Advisory Committee of the Journal of Numerical and Analytical Methods in Geomechanics for 19 years. Don is co-holder of three U.S. patents and has authored or co-authored over 90 papers in technical conferences and journals. Four of his papers have received the ASCE Hall of Fame award for contributions to the Offshore Technology Conference. He is a member of the International Society for Soil Mechanics and Geotechnical Engineering (ISSMGE) and chaired the Technical Committee on Offshore Geotechnical Engineering for four years. He is a registered Professional Engineer in Texas and was elected a Distinguished Member of ASCE in 2008. After his retirement from Exxon Don served as a Visiting Professor at Texas A&M University for 10 years and in 2010 was named a Distinguished Graduate of A&M's Zachry Dept. of Civil Engineering. Since his retirement from Exxon he has served as a consultant to the Offshore Industry. In 2012 he was selected by his peers to give the ISSMGE’s inaugural McClelland Lecture.
Among Don's avocations is Master's Swimming. Don has recorded a number of top 10 times in various events and has won several National Championships. Don is also a volunteer tutor for the ASCEND Learning Center in Austin where he helps young adults with developing job skills including earning their high school GEDs
Don has been married to the former Jean Megby for 51 years and they currently live in the Hills of Lakeway near Austin, Texas. They have two sons and daughters-in-law, Jim and wife Kris and Roger, wife Greta and two grandchildren, Sophie (15) and Thomas (13).