Environmental Effects on Materials
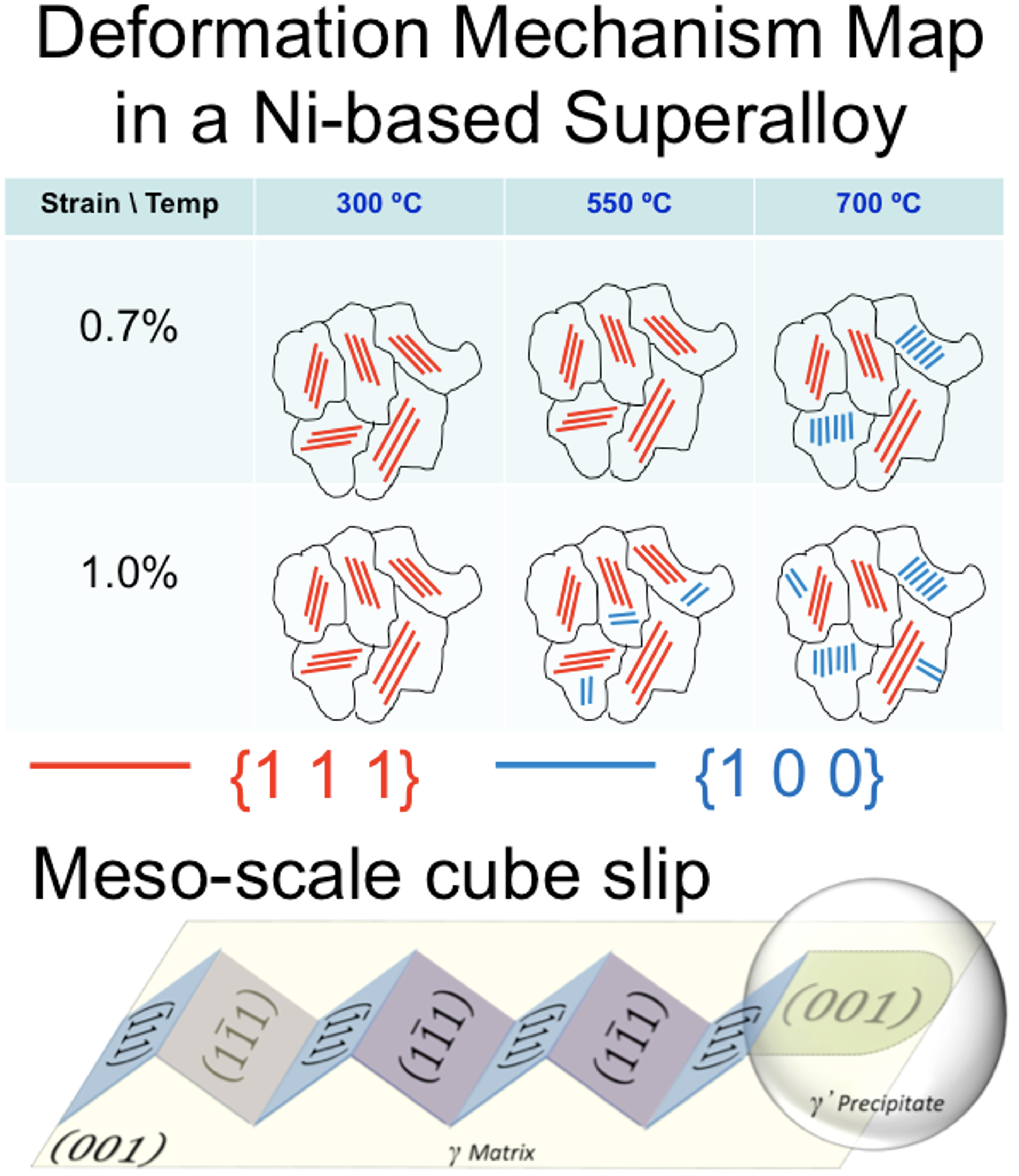
The aerospace industry offers the most challenging and harshest environments for materials, while simultaneously enforcing the strictest requirements for material safety and weight considerations. Evaluation of high-temperature materials environments is a difficult process. Too often researchers extrapolate room-temperature mechanisms to forecast high temperature behavior, but miss the underlying physics (example shown on the right). Our group tests materials in environments realistic to those experienced in service within aerospace applications, which are coupled with detailed characterization to identify the evolution of the microstructure and micromechanical fields in the material.
Our group offers unique capabilities to test materials in extreme environments. Specific research projects on this topic include:
- Thermo-mechanical fatigue of Ni-based superalloys (see image below: Deformation Mechanism Map in a Ni-based Superalloy)
- Oxidation-fatigue interactions in ceramic matrix composites (CMCs)
- Galvanic corrosion of airframe aluminum alloys (see image below: Day 2, Day 6, Day 11, Day 13, Day 15, Day 18)
- Materials in propulsion environments (including gas turbine engines and rotating denotation engines (see below: last image)
- Hydrogen effects on plasticity in single and polycrystalline Ni
- Reliability of coatings, including Ni-based superalloys, refractory alloys, CMCs, and C-C composites
- Ablation effects on the mechanical response of C-C composites and CMCs.