HOME CONTACT
RESEARCH
FACILITIES
PERSONNEL
PUBLICATIONS |
Achievements in Laser Cladding |
Stellite Cladding Example
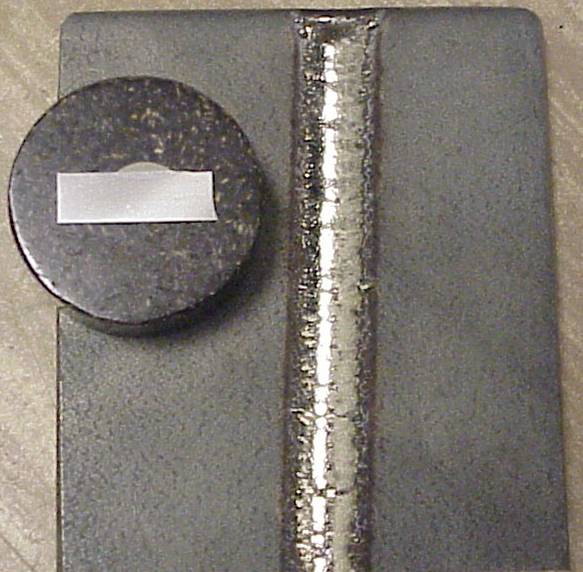 |
Micrograph of the cross section of a clad sample  |
Laser
Cladding Research |
Objectives:
The goal of this project area is to provide a complete physical understanding of the laser
cladding process (applied to various materials) and the development of a complete
predictive
model that will enable optimization of the process and its commercial application to
cladding
of various engineering surfaces
to meet precise specifications. Specific objectives of the research include:
- Find operating conditions that globally optimize the process in
order to:
- maximize laser cladding rate
- minimize sub-surface flaws
- maximize clad zone quality
- Investigate the laser cladding mechanism for various materials.
- Develop a predictive transient, three-dimensional thermo-diffusion model for laser
cladding.
- Understand the underlying physics of laser cladding.
- Develop guidelines to determine materials for which laser cladding is best suited.
- Develop an economic analysis of laser cladding against current practice
Back to Top |
Research
Plan: The study of laser-cladding at Purdue is based on the simultaneous
experimental and numerical investigation of the process. The experiments
are conducted using three different state-of-the-art set-ups, providing
an array of different capabilities. The existing set-ups
provide the capabilities of cladding a surface with a complex contour
using a high power direct diode laser (HPDL) due to the seven d.o.f. positioning ability and harmonizing software. Modeling
efforts include prediction of powder flow, melting and solidification,
resultant microstructure, deposited layer dimension and resultant
residual stresses. Several models are integrated to provide
the comprehensive predictive capabilities.
Back to Top
|
Research
Progress:
- Successful laser cladding of various materials has
been achieved by preplaced cladding and blown power cladding (see
the figures above for Stellite 6 on 1018 steel alloy ).
Deposited tracks no porosity, no cracks and minimal dilution (2-3%).
- A flexible cladding set-up (seven d.o.f.) has been established (see the
right figure below).
- Current work includes blown powder cladding, and preplaced
cladding of different materials.
- A predictive numerical model has been developed to predict and
optimize operating conditions during the cladding (see figures blow)
- Experimental measurements of powder velocities and temperature
during blown powder cladding have been performed to verify the
predictive model.
Back to Top |
Schematic of blown powder cladding
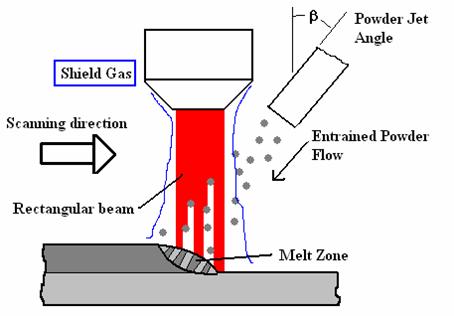 |
Cladding Experimental Set-up
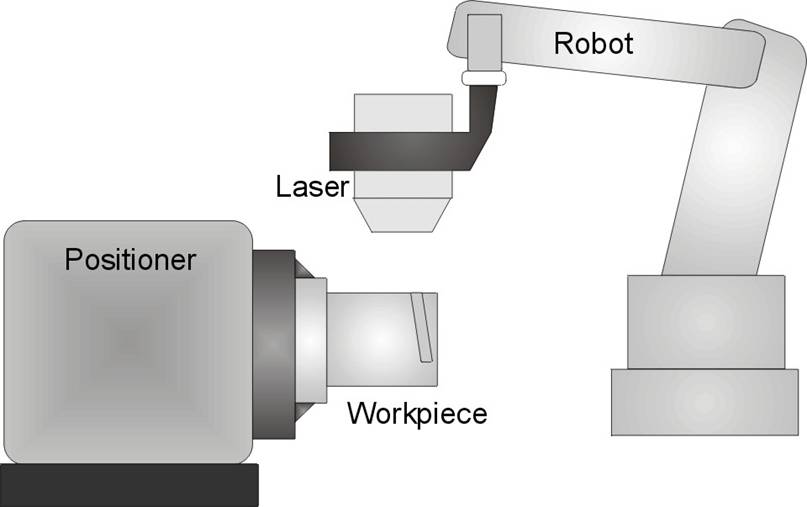
|
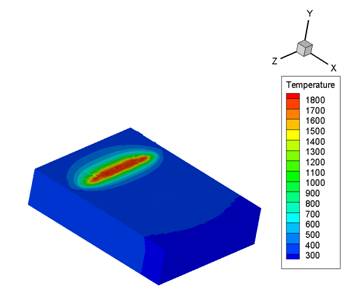
Predicted molten pool |
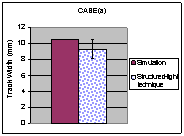 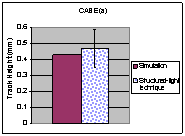

Predicted clad geometry |
SPONSORS National
Science Foundation
Purdue Research Foundation
Indiana 21st Century Research and Technology
Caterpillar
Adiabatics
|
Back to Top |