HOME CONTACT
RESEARCH
FACILITIES
PERSONNEL
PUBLICATIONS |
Laser Welding Processes Under Research |
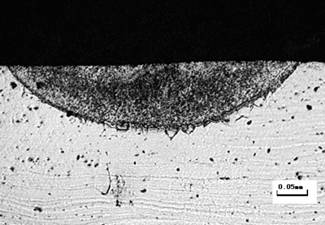
Conduction welding |
Key hole welding |
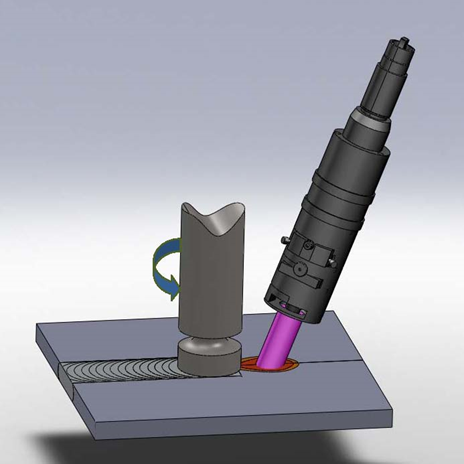
Laser-assisted FSW |
Laser
Welding Research |
Objectives:
The goal of this project area is to develop novel laser welding
applications at both macro and micro scales, using solid state lasers along with comprehensive modeling,
monitoring
and control capabilities. The developed predictive models consist of
a weld pool
model for key-hole dynamics, a solidification model, and a diffusion kinetics model,
which can predict the resultant microstructure and mechanical properties
of the weld joint. More specific goals include:
- Find optimal operating conditions for different materials in
order to:
- maximize laser welding rate
- minimize sub-surface flaws
- maximize weld joint quality
- Develop novel applications of laser welding such as fuel cell
stacks, magnesium alloys, zinc-coated steels, aluminum panels and
dissimilar materials
- Develop a comprehensive predictive multi-physics model for laser
welding processes.
- Develop in-process monitoring and control schemes for the laser
welding process.
- Develop a laser-assisted friction stir welding process for
difficult-to-weld materials
Back to Top |
Research
Plan: The study of laser welding Purdue is based on the simultaneous
experimental and numerical investigation of the process. The experimental
investigations
are being carried out using the high power fiber
laser set-up integrated with three axis machining center and diagnostics
capabilities for the entire welding process.
Modeling
efforts include development of multi-physics models for prediction of laser beam absorption, plasma-laser
interaction, melting and solidification, resultant microstructure, weld
pool dimension and resultant
residual stresses. Several
parallel processing computing workstations in cluster are available and
being used for these computational work.
Back to Top
|
Research
Progress:
- A predictive microstructure evolution model
has been developed based on the combined Cellular Automata and
Phase Field method (see the sample result in Fig. 1).
- A comprehensive molten pool model considering free surface
tracking has been developed for both fusion welding and keyhole
welding and is being coupled with the microstructure evolution model
(see Fig. 2 and 3).
- An experimental system has been established (Fig. 4).
- An on-line weld pool monitoring and control system has been
developed and successfully demonstrated.
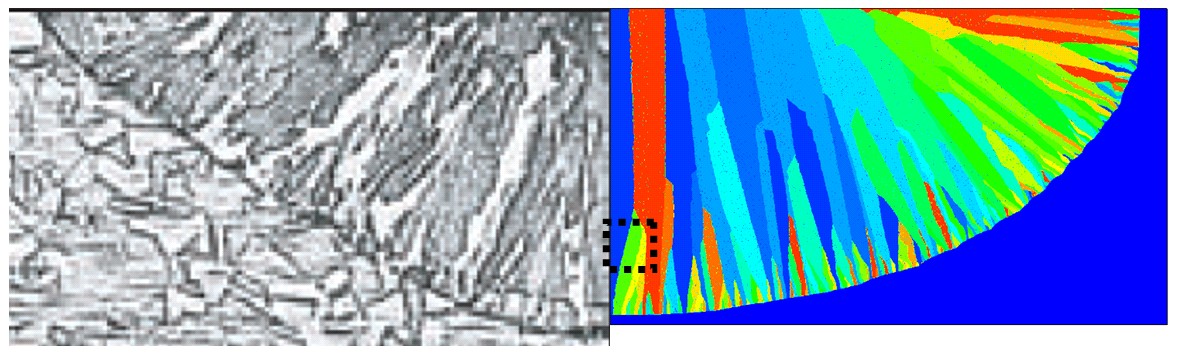
Fig. 1: Predicted and measured
columnar dendrite after fusion welding
|

Fig. 2: Predicted and measured molten
pools during fusion welding
|

Fig. 3: Predicted
and measured keyhole weld pool
|
Fig.
4: Laser welding system |
Back to Top
|
SPONSORS National
Science Foundation
Industrial Members
|
Back to Top |