HOME
CONTACT
BACKGROUND
RESEARCH
FACILITIES
PERSONNEL
PUBLICATION IN LAM
PUBLICATIONS |
Laser-Assisted Machining Research |
Objectives:
An ultimate objective is to provide alternative, economically
attractive machining process capabilities with a complete physical understanding of the LAM
processes and the development of a comprehensive thermo-mechanical
model that will enable its commercial application to machine parts made
of advanced materials such as ceramics, composites and high temperature
alloys to precise
specifications. Specific objectives of the research include:
- Determine the [LAM] machinability improvement of ceramics
including silicon nitride, zirconia and mullite, various metal
matrix composites and high temperature alloys including titanium
alloys, nickel-based alloys and hardened alloys.
- Find operating conditions that globally optimize the processes, taking into account to:
- maximize material removal rate
- minimize sub-surface flaws
- minimize surface roughness
- minimize tool wear
- Determine the material removal mechanisms for various workpiece materials.
- Determine the tool wear mechanism and tool wear rate for representative LAM conditions.
- Develop material constitutive models for various materials for
stress, strain and strain rates representative of LAM.
- Develop transient, three-dimensional model of the workpiece undergoing LAM, including
internal radiation for semi-transparent materials.
- Understand the underlying physics of LAM.
- Develop guidelines to determine materials for which LAM is best suited.
- Develop an economic analysis to determine conditions for which LAM is a feasible
alternative to grinding or hard turning.
Back to Top |
Research
Plan: The study of laser-assisted machining at Purdue is based on the simultaneous
experimental and numerical investigation of various processes including
turning, milling and micromilling. The experiments and modeling
share a symbiotic relationship, as certain parts of one relies on results from the other (Schematic). This allows the underlying physics to be
determined while increasing the machining knowledge-base.
Back to Top
Achievements
in LAM
| |
Experimental results:
-
LAM has been
successfully applied to machining of various ceramics such as
silicon nitride, partially stabilized zirconia and mullite (as shown
below). A significant improvement of machinability has been
achieved with long tool life up to 2 hours.
-
LAM has been
successful in improving machinability of various
difficult-to-machine alloys such as Inconel 718, Ti-6Al-4V, Waspaloy,
Compacted Graphite Iron, stainless steel (P550), hardened steel,
high Cr. steel, and metal matrix composites. Typical improvement
includes 30% reduction in specific cutting energy, 2-4 fold
improvement in surface roughness, and 2-4 fold improvement of tool
life. It has been demonstrated that LAM does not
adversely affect the subsurface integrity (no microstructural
changes, no subsurface damage or cracks, compressive residual
stresses).
-
LAM capabilities for
micromachining have been successfully demonstrated for various
materials, including titanium alloys, ceramics and ceramic-matrix
composites. In each case, a significant improvement of
tool life, surface quality and cost savings has been demonstrated.
Modeling results:
-
Three-dimensional
transient numerical models have been developed to predict the
workpiece temperature distributions during laser-assisted turning and milling
operations.
-
Multi-scale,
multi-phase finite element models have been developed to predict the
LAM processes and subsurface damage.
|
Silicon Nitride
|
Zirconia Ceramics
|
Mullite
|
Thermal
Model
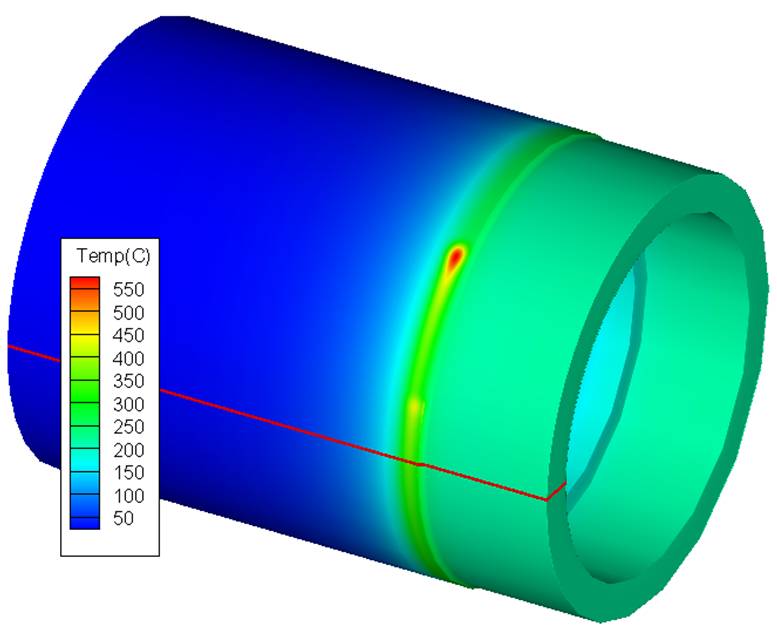 |
Comparison between conventional machining and LAM of MMC
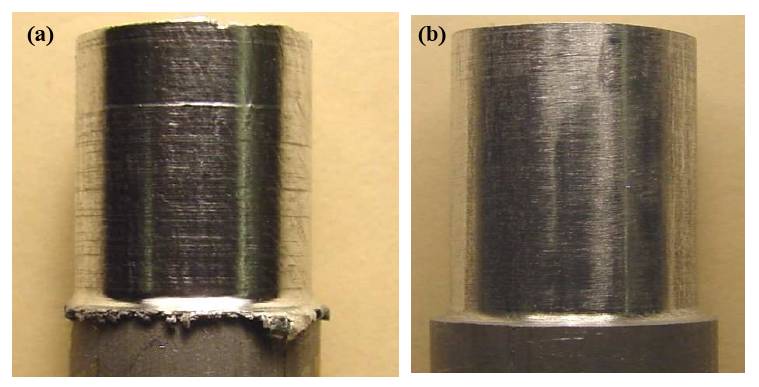
Conventional
LAM |
Economic
Analysis
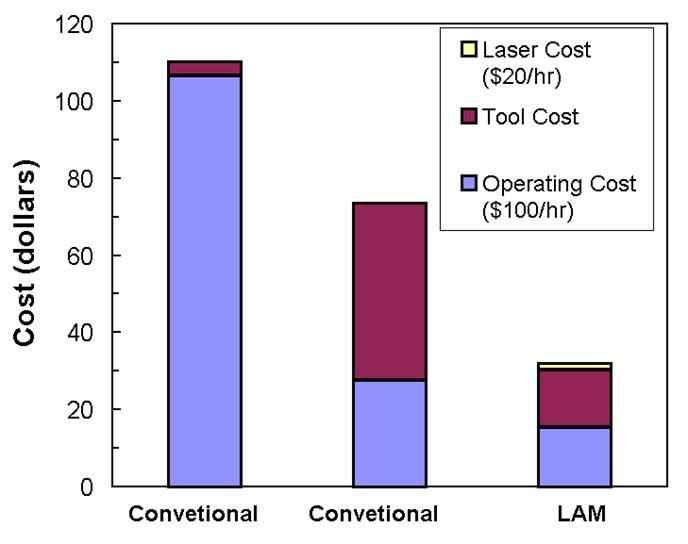 |
Back to Top |
Numerical Modeling
|
LAM Experiments
|
SPONSORS National
Science Foundation
Caterpillar,
Schlumberger, Lockheed Martin, Weir Minerals, Rolls Royce, Boeing, GE
Aviation
Indiana 21st Century Research and Technology
DoD, NASA
|
Back to Top |