Laser
Peening Research |
Objectives:
The goal of this project area is to provide a complete physical understanding of the laser
peening process and to develop a comprehensive
predictive
model, which will enable optimization of the process to achieve desired
residual stress specifications. Specific objectives of the research include:
- Study the fundamentals of laser-material-plasma interaction during
laser peening processes.
- Develop comprehensive predictive modeling capability for laser
peening processes.
- Find operating conditions that globally optimize the process in
order to:
- maximize laser peening rate
- achieve desired residual stress distributions.
- Study the laser peening mechanism for various workpiece materials.
- Develop guidelines to determine materials for which laser peening is best suited.
- Develop an economic analysis of laser peening against current practice.
Back to Top |
Research
Plan:
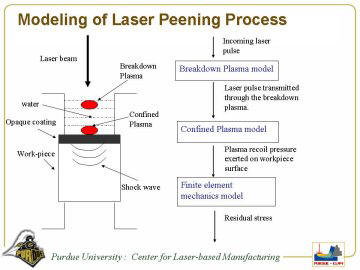 The study of laser
shock peening at Purdue is based on the simultaneous
experimental and numerical investigation of the process. The experiments
are performed using a ns solid state laser integrated with a positioning
system. Modeling
efforts aim at developing a comprehensive predictive model, which allows
the prediction of residual stress profiles in terms of laser operating
parameters, coating material and thickness, and workpiece material,
while accounting for the existing stress distribution. This allows the underlying physics to be determined while increasing the
laser shock peening
knowledge-base.
|
Research
Progress:
- A comprehensive 1D thermal model of laser peening process has been
developed. The model is capable of predicting plasma
pressure, laser-plasma interaction, electron densities, etc. (figures in the
top row below)
- The water breakdown plasma phenomenon has been successfully
modeled. This can provide the limit of laser peening
processes in terms of laser power.
- A 3D finite element modeling procedure of predicting residual stresses with
given plasma recoil pressure has been developed. This can
provide the resultant residual stress distributions (figure in bottom
row below)
- Laser-based monitoring techniques are being developed to monitor
various conditions such as plasma plume size, plasma temperature and
electron density during laser shock peening processes.
Back to Top |
Predicted Plasma Pressure
vs. Time  |
Predicted
vs. Measured Max. Plasma Pressure

|
|
FEA predicted
shock wave propagation in A356-T6 alloy workpiece
 |
Predicted
vs. Measured Residual Stress Distribution
 |
|
SPONSORS National
Science Foundation
Purdue Research Foundation
Indiana 21st Century Research and Technology
Industrial partners
|