HOME CONTACT
RESEARCH
FACILITIES
PERSONNEL
PUBLICATION IN AM
ALL PUBLICATIONS |
Laser
Additive Manufacturing Research |
Objectives:
The goal of this project area is to develop the critical and enhanced capabilities of
building three dimensional functional parts directly from CAD drawings
and synthesizing novel materials using various laser-based additive
manufacturing processes. It also aims at developing a complete
set of predictive
models that will facilitate design, optimization, qualifications of the
AM processes and their commercial applications. Specific objectives of the research include:
- Find optimal operating conditions for various applications in
order to:
- maximize build rate
- minimize sub-surface flaws
- maximize part quality
- Develop functionally grade deposition capabilities of material for various materials.
- Develop a comprehensive set of predictive multi-physics models
that link process-microstructure-mechanical properties for laser-based
additive manufacturing processes.
- Develop data-driven models that will capture the physical
relationships
- Develop the capabilities of synthesizing metal matrix composites
- Develop the in-situ synthesis of novel materials such as bulk metallic glass materials,
shape memory alloys and high entropy alloys
- Develop in-process monitoring and control schemes for the laser
additive manufacturing processes.
Back to Top |
Research
Plan: The study of laser additive manufacturing at Purdue is based on
the simultaneous experimental and numerical investigation of various AM processes. The experimental investigations are carried out using
multiple additive manufacturing systems (both blown powder and powderbed, see the bottom figures) to develop various applications including direct
fabrication of functional parts, in-situ synthesis of metal matrix
composites and new alloys, and functionally graded materials. Modeling
efforts include multi-physics based comprehensive predictive models
for prediction of powder flow, melting and solidification,
resultant microstructure, deposited layer dimension and resultant
residual stresses. To this end, various in-house developed
codes have been developed
and are coupled with commercial FEM codes such as Abaqus to calculate the
resultant residual stresses and mechanical properties. A number of
parallel processing computing workstations in cluster are available and
being used for these computational work.
Back to Top
|
Research
Progress:
- Experimental studies on AM of over 30 different materials,
including following materials:
Iron and steels |
Fe, H13, SS316, SS304, ODS steel |
Other Alloys |
Ti-based: CP Ti, Ti6Al4V |
Ni-based: Inconel 625, Inconel 690,
Inconel 718 |
Al-based: Al4047, Al6061, Al7075 |
NiTi shape memory alloy |
Bulk metallic glasses (FebalCr25Mo20W10Mn5C3Si2B5,
Zr65Al10Ni10Cu15) |
Co-Cr-based: Stellite 6 (Co-Cr-W-C+others),
Co-Cr-Mo |
Monel K500 (Ni63Co27-33+others) |
Metal matrix composites |
Ti-TiC |
Al-SiC |
Ti6Al4V-TiC |
In690-TiC |
Other materials |
W, Mo, Graphite, ZrO2 |
- A comprehensive set of physics-based models:
- Process models:
- modeling for powder flow distribution and temperature from the co-axial nozzle,
- comprehensive molten pool model considering free surface
tracking, coupled with the powder distribution model has been developed to optimize operating conditions
of the directed energy deposition processes (see Figs. 1 and 2
below)
- high fidelity powderbed fusion process model,
considering powder spread, powder dynamics, molten pool
dynamics considering denudation and powder-molten material
interaction, etc.
- Microstructure prediction models:
- phase field modeling for solidification (2D, 3D)
- cellular-automata model for large domain grain
morphology prediction (3D)
- hybrid cellular automat-phase field model that improves
the computational efficiency by 4 orders of magnitude over
phase field model (2D, 3D)
- solid state phase transformation models
- Mechanics model
- prediction of mechanical properties based on
microstructure (multiscale models)
- prediction of mechanical properties based on
microstructure (structural genome based)
- metallo-thermo-mechanical modeling for prediction of
residual stresses
- In-process monitoring
- An on-line track monitoring system based on a vision system and
a scanning laser has been developed. This system is
capable of measuring the three dimensional deposited tracks in real
time (see Figs.
3 and 4 below).
- In-process molten pool monitoring
- In-process porosity monitoring
- Applications:
- Successful fabrication of various parts including hip implants
(see the sample parts on the top of this page).
- Functional gradient coating
- Synthesis of bulk metallic glasses
- Synthesis of Nitinol with controlled phase transformation
temperature and mechanical properties
- Remanufacturing of legacy parts
- Synthesis of magnetic materials
- Synthesis of nuclear reactor materials
- In-situ synthesis of metal matrix composites
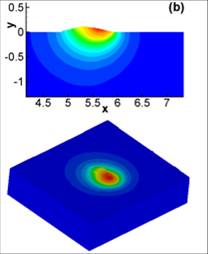
Fig. 1: Molten pool and deposition
track model |
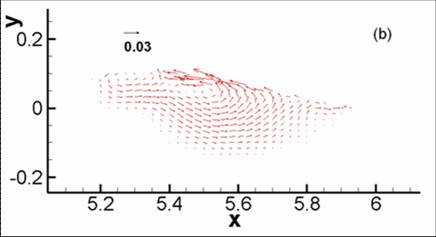
Fig. 2: Molten pool fluid flow prediction |
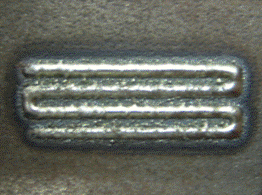
Fig. 3: Actual track |
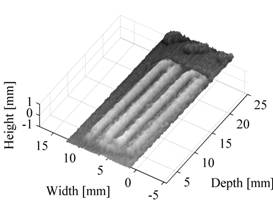
Fig. 4: Measured
Track by the vision system |
Back to Top
|
 Fig.
5: 5 axis direct deposition system
|
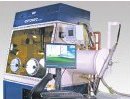
Fig. 6:
Optomec LENS 750 |
SPONSORS National
Science Foundation, DoD, DoE, DTRA, NASA
Purdue Research Foundation
Indiana 21st Century Research and Technology Fund
Industrial Companies
|
Back to Top |