CTRC Breakthroughs
Renewable and Sustainable Energy
Research Topics
Microscale Transport and Microchannels
Electrically Actuated Microscale Flows
Thin-Film Transport, Wicks and Heat Pipes
Novel Air and Impingement Cooling Approaches
Surface and Interface Engineering
Thermal Materials R&D
Thermal Interfaces
Small-Scale Refrigeration
Exploratory and Novel Concepts
Renewable and Sustainable Energy
Integrated Electric Vehicle Battery Thermal Management
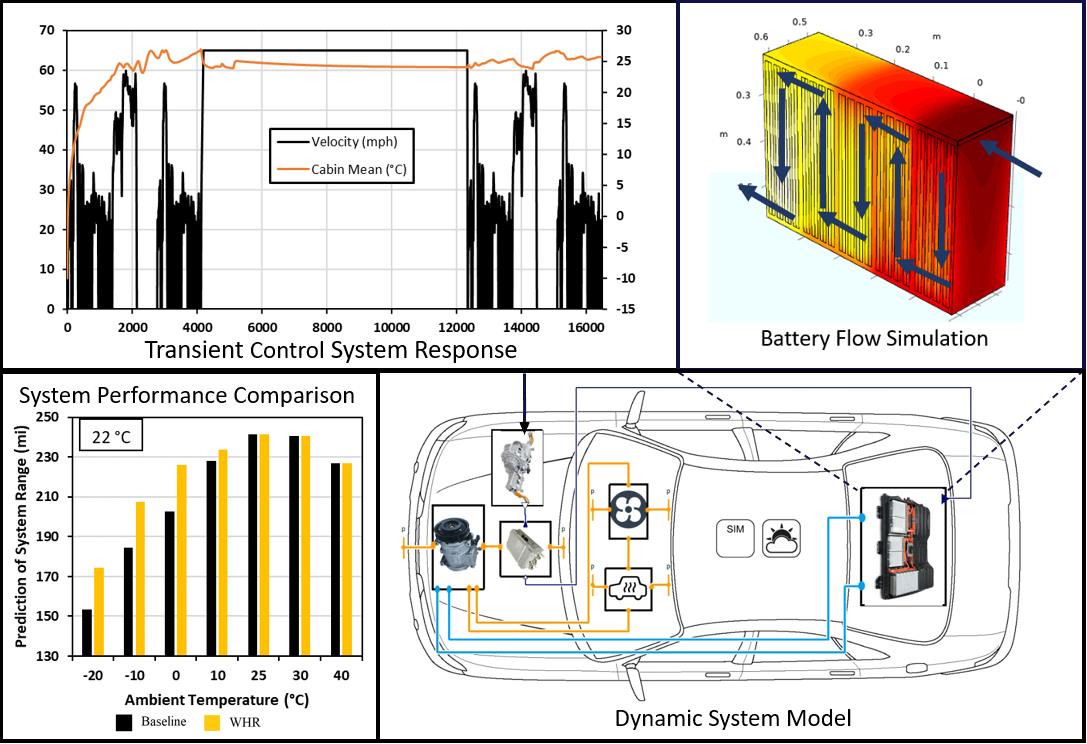
Previous analyses of electric vehicle thermal systems have been conducted under different drive cycles, ambient conditions, and system control schemes. Consistent analyses across various candidate thermal system architectures is desired to assess the pros and cons of each architecture under different cycles and ambient conditions, and ultimately to design the next generation of electric vehicle thermal management systems. This project has identified and characterized the performance of a baseline electric vehicle thermal management system and to this end, a dynamic system model was developed to simulate across a range of ambient, drive cycle, and control parameters. Moreover, the thermal management system model has been extended to include five additional systems, one being a novel approach to low temperature waste heat recovery. Further investigation of battery pack construction in dependence of TIM, flow rate, and inlet temperature parameters was completed. These studies identified an optimal EV thermal management system and optimal cooling structure for the battery pack.
Optimization of CO2 Heat Pumps for Commercial Building Applications
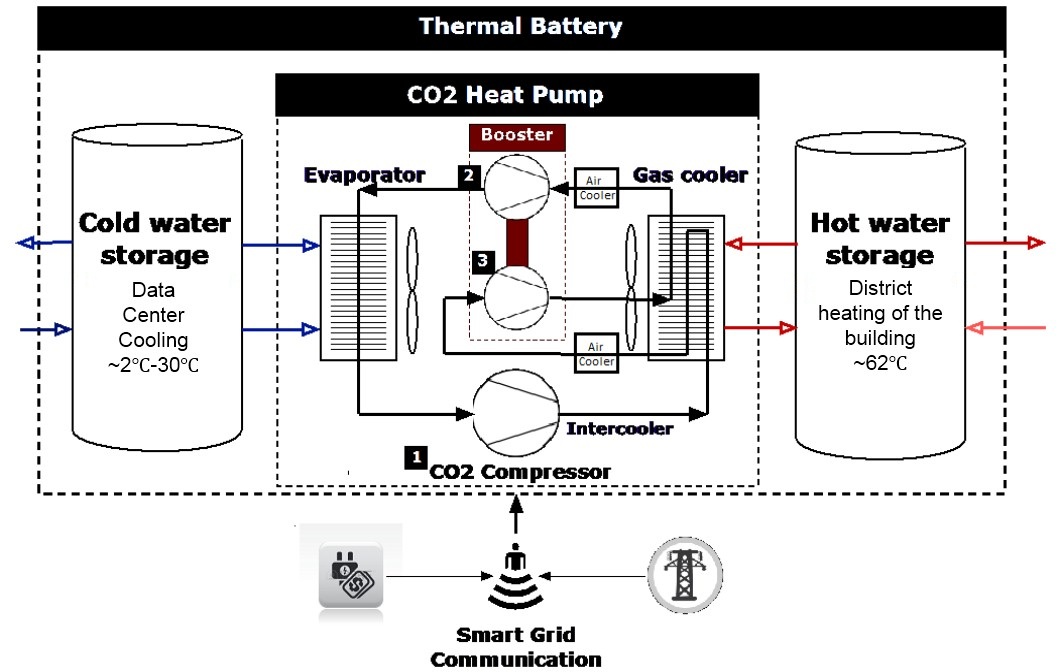
The proposed heat pump uses CO2 as the refrigerant. CO2 has a low GWP, is non-toxic, non-flammable and non-corrosive. Integrating the heat pump with a thermal battery for commercial applications allows the system to be operated with Smart Grid technologies. Many commercial buildings, including data centers, hotels and hospitals, have simultaneous heating and cooling demands depending on season, occupation and auxiliary equipment. Electrical equipment that produce heat could provide a potential for cost-effective and energy efficient operation of buildings if integrated appropriately. Liquid-to-liquid CO2 heat pump systems are a promising technology for such applications. A model was created to analyze a data center on the Purdue University campus. The simulations show energy savings of approximately 28%, which results in noteworthy environmental benefits.
Organic Rankine Cycle with Solution Circuit or Low Grade Heat Recovery
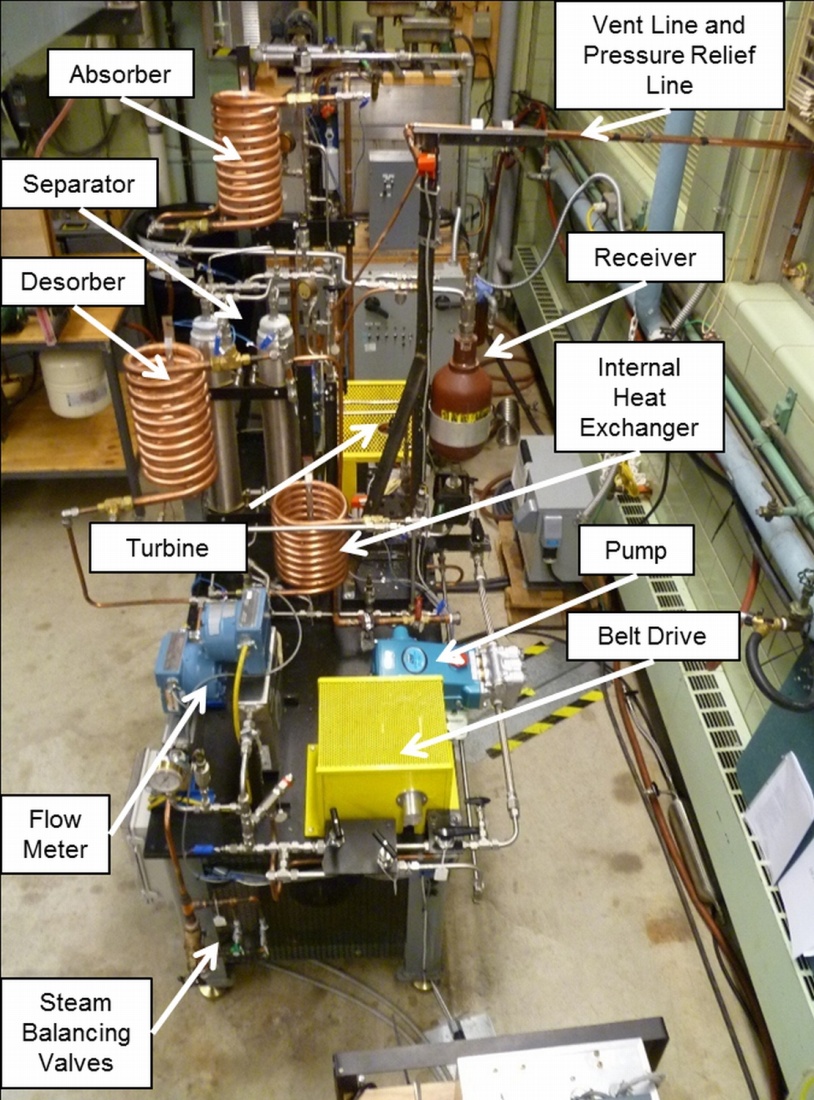
The Organic Rankine Cycle with Solution Circuit (ORCSC) is an attractive technology for harnessing low grade heat as an energy source for power generation. Preliminary numerical modeling has shown that the ORCSC offers significant efficiency improvements over current technology for comparable systems. It also allows the use of high pressure, environmentally neutral working fluids such as carbon dioxide at far lower pressures than found in other systems. The model offers a simple, cost-effective solution for adapting the system for peak and non-peak loads that the system is likely to encounter in practice. Integrating two different bodies of knowledge, namely mechanical fluid flow machines (expansion turbines) and heat and mass transfer (absorption and desorption) in the heat exchangers, into one technology is the broad technical challenge for this system. Simulation and preliminary experimental results have shown that this technology is particularly effective for low source temperatures where achieving cycle efficiencies as close to the theoretical (Carnot) limit as possible is important for ensuring the economic feasibility of the technology. The figure shows the experimental test facility for Organic Rankine Cycle with Solution Circuit showing all major system component
Thermoelectric Power Generation from Waste Heat in Electronic Systems
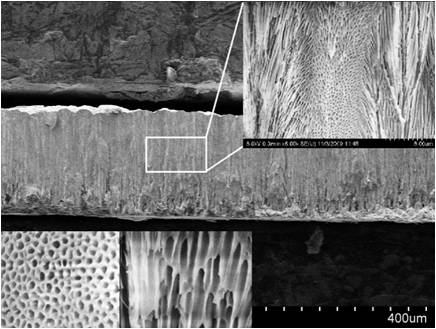
One promising technology for converting waste heat to electric power is the thermoelectric generator (TEG). Recent improvements in the thermoelectric figure-of-merit, ZT, bode well for the implementation of these solid-state waste heat recovery systems. This project not only involves designing the fabrication process of a low grade waste heat generator but also developing a modeling tool to optimize the element configuration. The model completed recently allows assessment of the effect of element design, contact resistance, leg length, and thermoelectric properties on power density and efficiency. The figure shows 350 micron thick self-supporting branched porous anodic alumina template for microcoolers and waste heat energy converters.
Alternative Waste Heat Recovery Opportunities
Thermally activated systems based on sorption cycles, as well as mechanical systems based on vapor compression/expansion are assessed in this study for waste heat recovery applications. Two cycles are considered to provide refrigeration or air-conditioning, two cycles are considered for power generation, and one is considered to upgrade low-grade heat to higher temperatures. The size and performance of each system is estimated for two general cases. One for smaller-scale and low-temperature waste heat availabilities and the other is for larger-scale and higher-temperature applications. Comparative assessments of these cycles on the basis of efficiencies and system size, guide the selection of waste heat recovery and upgrade systems for different applications and waste heat availabilities. It is found that even with such low-grade waste heat sources, work produced is approximately 10% of the available waste.