Materials Processing: Intelligent Heat Treating of Alloys
One of the most important applications of spray cooling is quenching of aluminum alloy and steel parts. Quenching is the most critical stage of heat-treating, which is intended to control the alloy’s microstructure in pursuit of superior mechanical properties. Heat-treating is comprises of three stages: solution heat-treating, quenching, and age-hardening. Solution heat-treating involves heating the alloy to near liquidus temperature to enable alloying elements to diffuse into the grains of the primary metal. This is followed by rapid quenching to retain the alloying elements in supersaturated solid solution. Age hardening is accomplished by reheating the alloy below solvus temperature for a specified time period, resulting in a fine dispersion of precipitates within the grains of the primary metal. These fine precipitates produce an alloy with maximum hardness and maximum strength.
Implementation of quenching is by far the most challenging stage of heat-treating. A slow quench could result in massive precipitation along the primary metal grain boundaries rather that within the grains, producing a microstructure that cannot be improved upon by age-hardening. Conversely, a very fast quench rate might induce large variations in cooling rate between thin versus thick sections of a complex-shaped part, resulting in potentially severe residual stresses. Both slow and non-uniform quenching are commonly encountered with bath quenching, where no means are available to control local cooling rate for different regions of the part’s surface. This is where spray cooling can play a very beneficial role, by providing localized control over cooling rate through changes in any number of spray parameters, especially supply pressure and orifice-to-surface distance. Using an arrangement of optimally configured sprays, a complex-shaped alloy part may be cooled uniformly by impacting thick sections of the part with dense sprays and thin sections with light sprays.
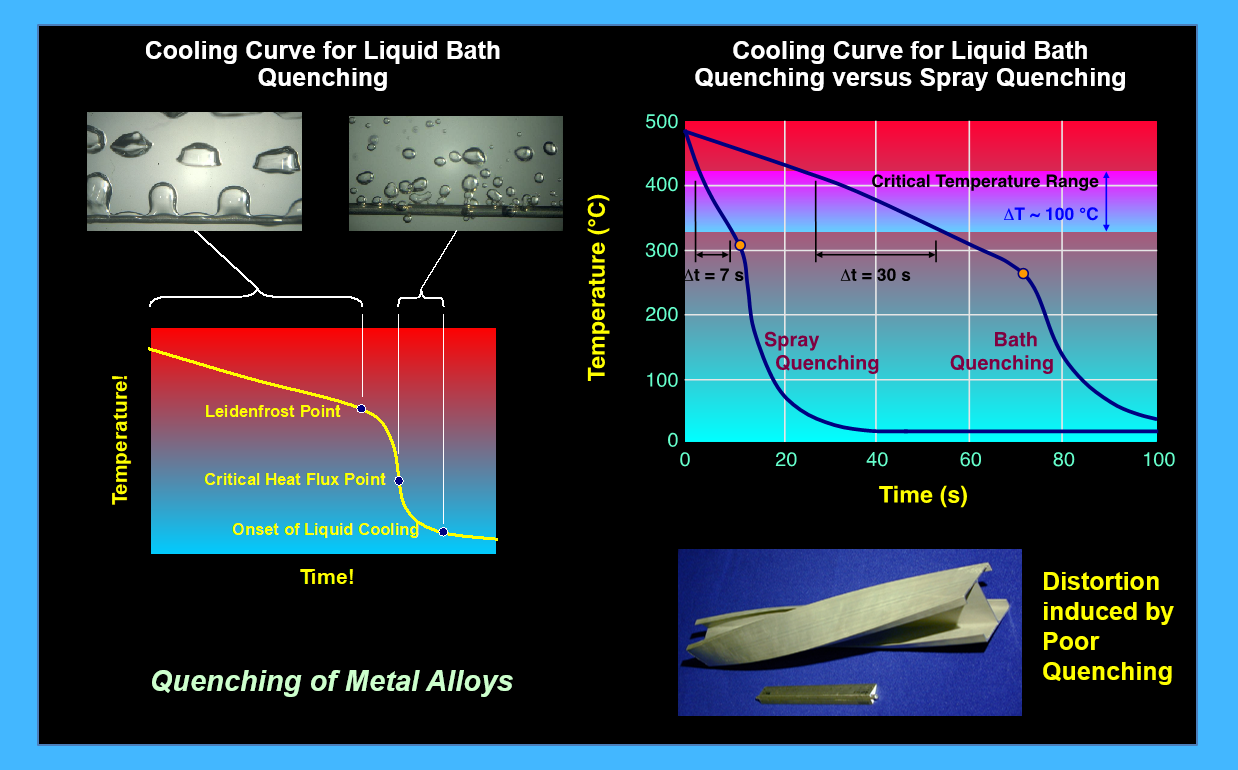
Over the past three decades, our team performed extensive tests in pursuit of fundamental understanding of spray physics, and to develop detailed correlations to predict heat transfer behavior during the various phases of a quench. Our most important accomplishment is development of a revolutionary, cost-effective approach to heat-treating complex-shaped metal alloy parts that promises to eliminate altogether the trial-and-error production practices prevalent in the industry today. Using cooling and metallurgical transformation models, an intelligent CAD system enables the operator of the quench station to optimize the entire process simply by entering the part’s geometry and alloy composition. Upon consulting its databases, the CAD system automatically configures a robot-manipulated spray quenching system to achieve optimum cooling and yield desired mechanical properties. The immediate benefits from the proposed technology are cost savings, energy savings, reduced water consumption, reduced emissions and greenhouse gases, superior part strength and hardness, enhanced corrosion resistance, reduced residual stresses, reduced warping, reduced cracking, greatly increased productivity, and elimination of scrap.
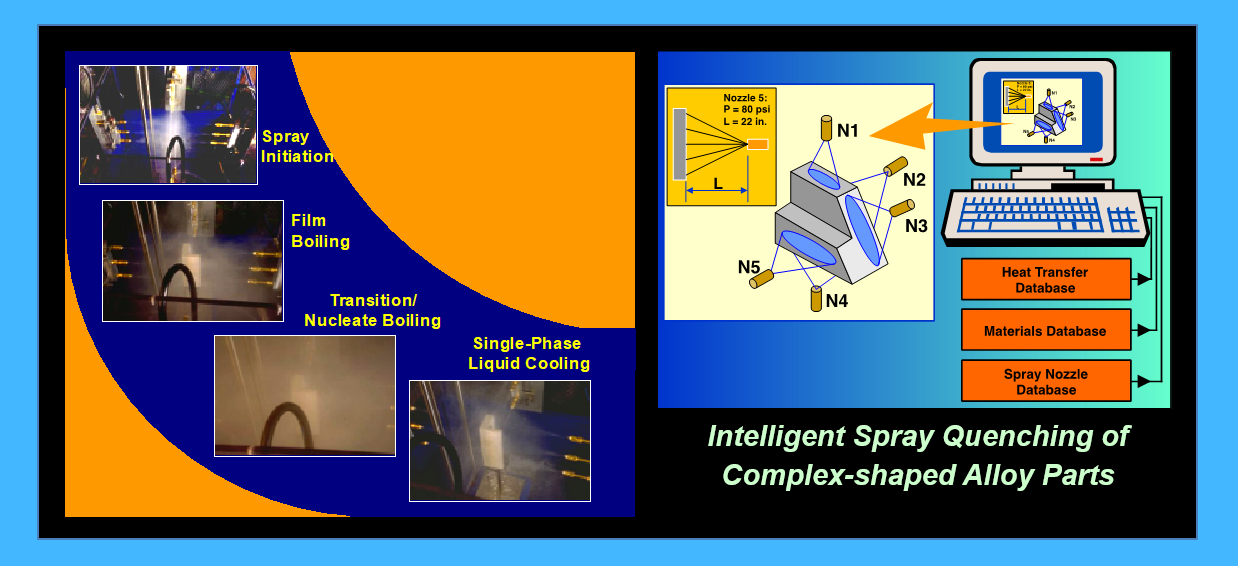