Spray Cooling
Spray cooling provides several important cooling benefits, such as high heat transfer coefficients, high critical heat flux (CHF), and better surface temperature uniformity than jet impingement for large surface areas. Cooling effectiveness is realized by breaking the liquid into a dispersion of fine droplets having large surface-area-to-volume ratio, which acquire multiple trajectories and impact a broad surface area.
Designing a spray cooling system is by no means a straightforward endeavor. Cooling system designers are quickly confronted with the task of configuring a system whose performance depends on an usually large number of parameters. Aside from nozzle type and coolant, cooling performance is influenced by droplet size, droplet velocity, volumetric flux, and the spatial distributions of these parameters, in addition to spray angle, nozzle orientation angle, and orifice-to-surface distance.
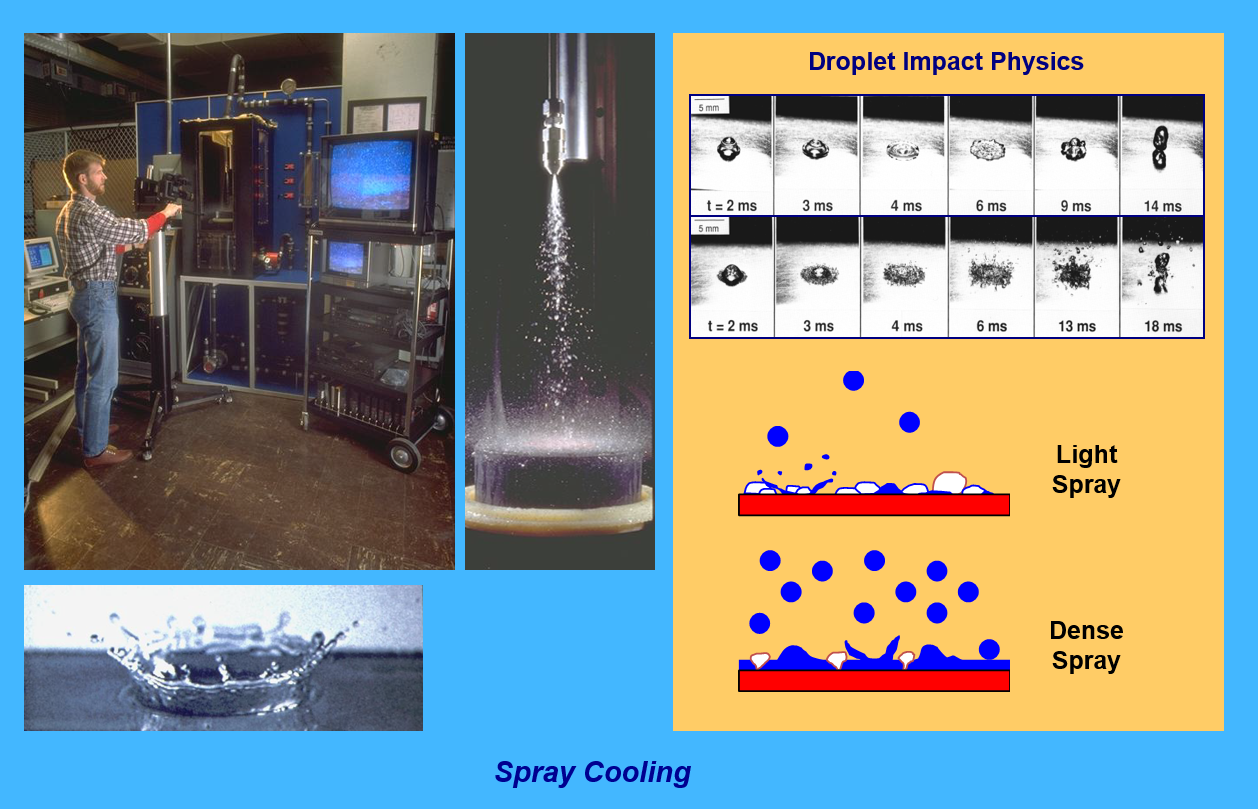
In response to these challenges, our team has developed a comprehensive design methodology to tackle the influences of all spray parameters with a high degree of accuracy, and which is applicable to coolants with drastically different thermophysical properties.
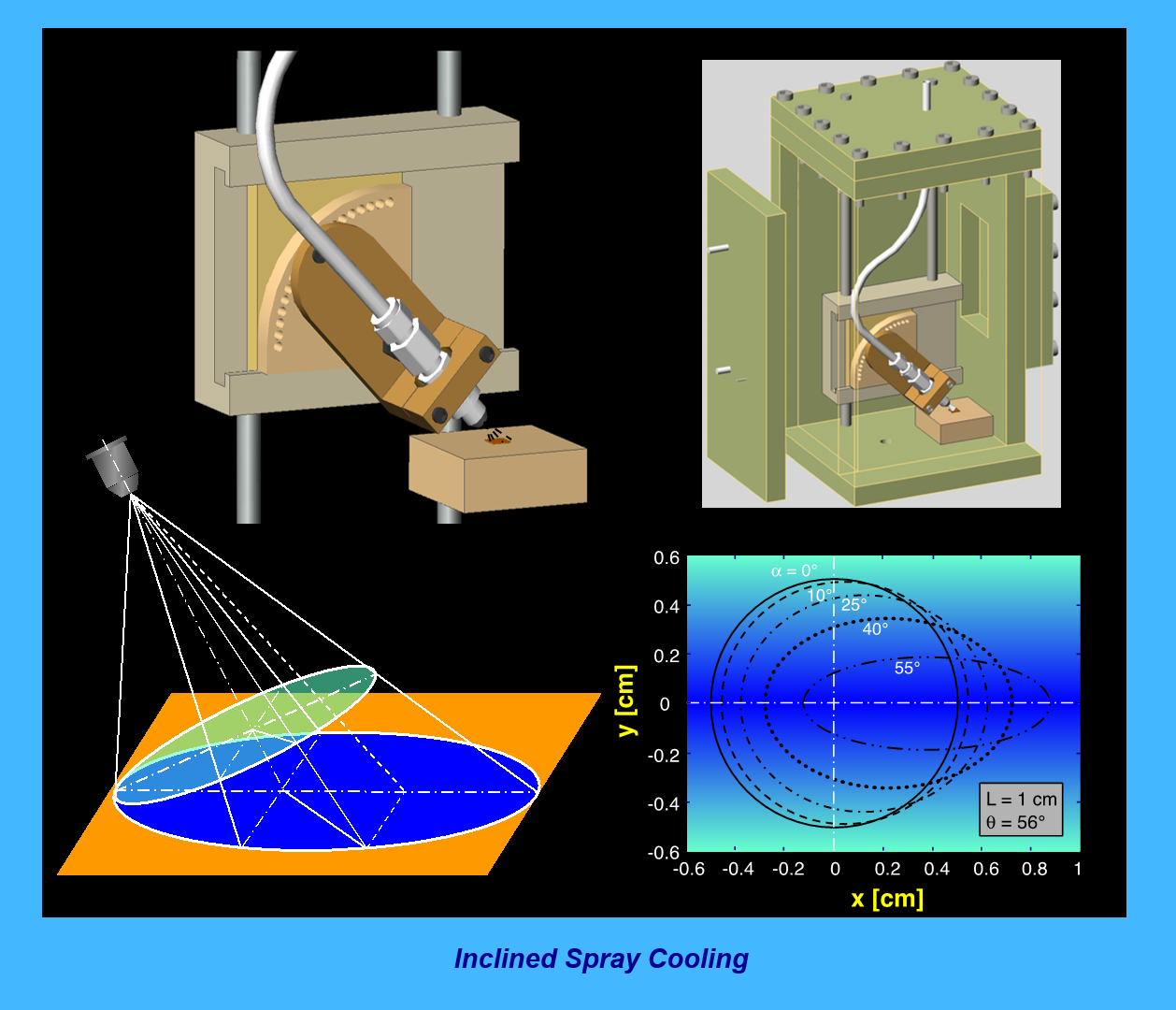