Electronics Refrigeration Cooling
While modern electronic and power devices have witnessed a significant increase in heat dissipation rate, the maximum allowable temperature in most applications has remained fairly constant or increased by a modest amount. In any liquid cooling application, device temperature increases with increasing heat dissipation rate for a fixed coolant temperature. This dependence could bring device temperature above the maximum allowable limit when dissipating high heat fluxes. Maintaining acceptable temperatures in this situation requires reducing the temperature of liquid coolant. But this might bring coolant temperature below ambient, which necessitates the use of a refrigeration system to sustain the cooling.
Various refrigeration cooling schemes have been explored. Of those, vapor compression is deemed most practical. Our team has demonstrated refrigeration cooling of electronics using two different configurations that employ micro-channel heat sinks. In the first direct-refrigeration-cooling configuration, the micro-channel heat sink serves as evaporator in the vapor compression loop. Here, the refrigerant is used as coolant for the heat-dissipating device. The second indirect-refrigeration-cooling configuration involves using two fluid loops. Heat from the device is rejected by subcooled boiling in the micro-channel heat sink to a primary coolant circulated through a pumped loop that rejects the heat via a liquid-to-liquid heat exchanger to refrigerant flowing in a separate vapor compression loop. The two configurations produce two drastically different types of flow boiling inside the heat sink, saturated and subcooled.
In direct-refrigeration-cooling, a refrigerant such as R134a enters the micro-channel evaporator as two-phase mixture and exits as saturated mixture or, preferably, superheated vapor, as required by the compressor. The refrigerant undergoes rapid change of phase along the evaporator into a high vapor fraction mixture, resulting in mostly annular or slug flow.
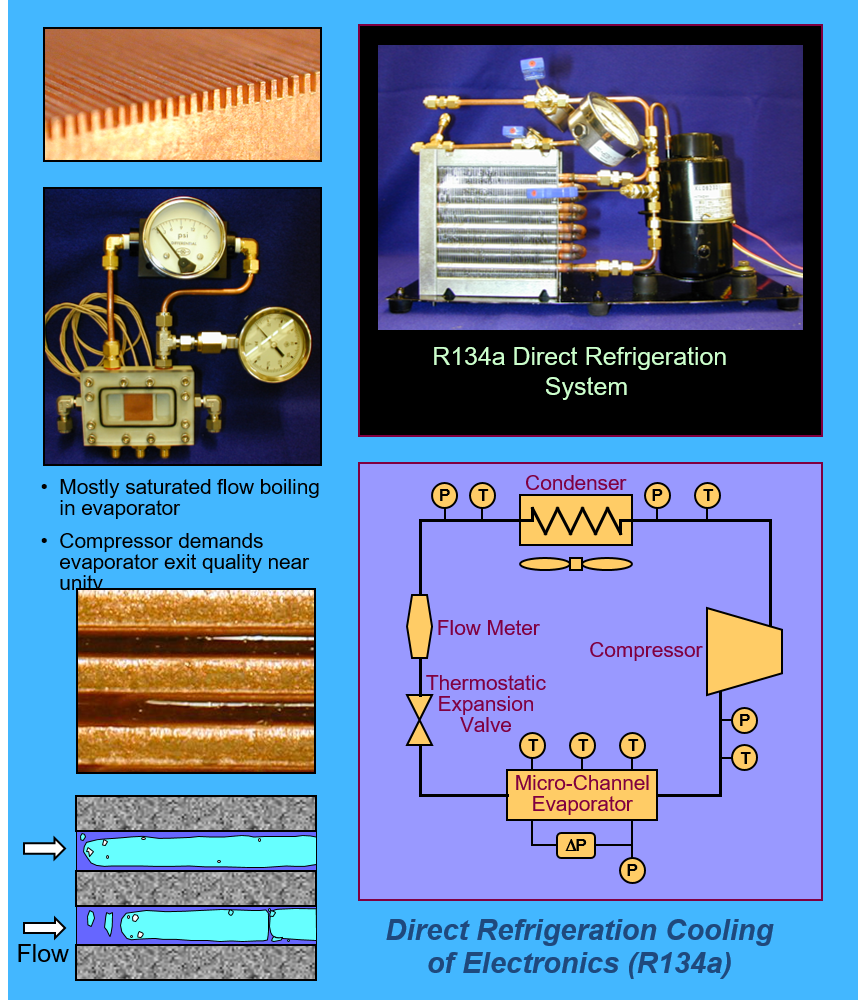
The separate primary coolant loop in the indirect-refrigeration-cooling configuration provides great flexibility in attaining desired micro-channel heat sink’s inlet conditions, and the coolant need not be maintained in saturated state. In fact, it is typically supplied to the heat sink in subcooled state with thermodynamic equilibrium quality below zero. The quality increases along the micro-channels but, because micro-channel heat sinks are relatively short, subcooled boiling can prevail to the outlet. Because of relatively vapor small void fraction in subcooled boiling, both pressure drop and heat transfer characteristics are categorically different from those for saturated boiling. Our team has developed design relations for pressure drop, two-phase heat transfer coefficient, and critical heat flux (CHF) for indirect-refrigeration-cooling using HFE 7100 as primary coolant. They showed that, while direct-refrigeration-cooling with R134a does yield very high heat transfer coefficients, its cooling performance is limited by relatively low CHF. Because of the ability to maintain subcooled conditions, indirect-refrigeration-cooling can yield much higher CHF values and is therefore far better suited for high-flux heat dissipation. Tests with this system yielded heat fluxes as high as 840 W/cm2 with HFE 7100 without incurring CHF.
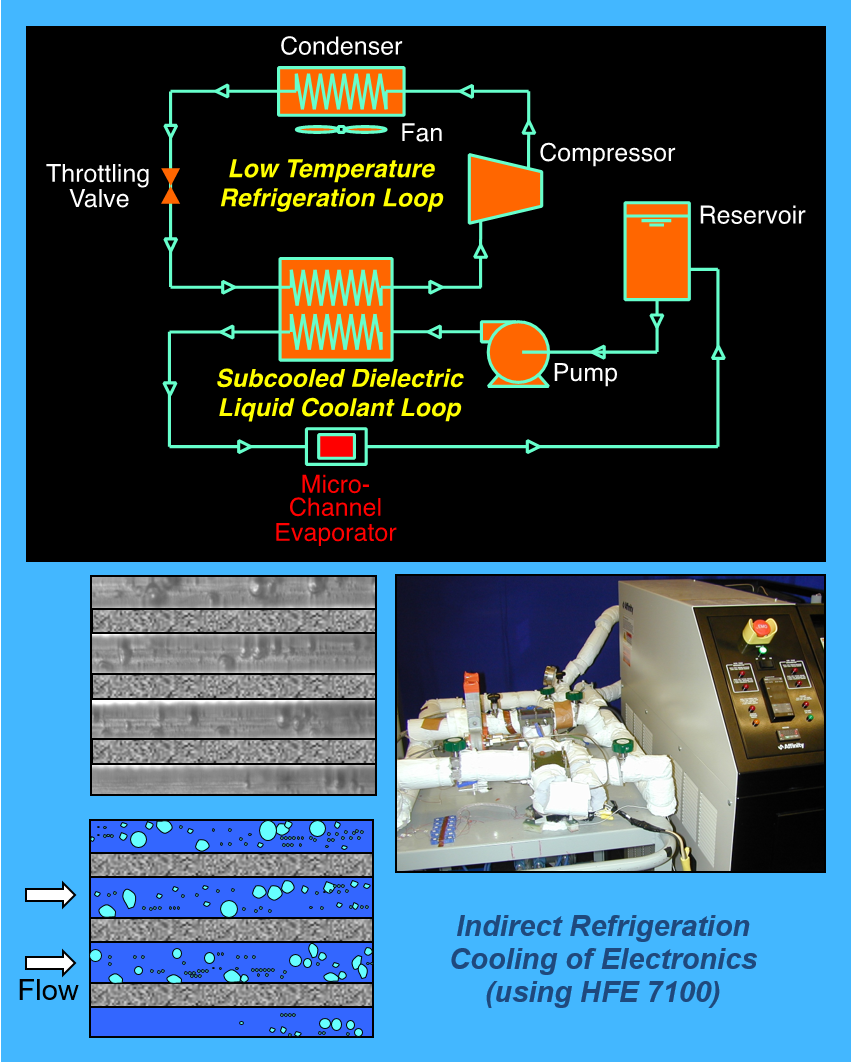