Electronics Cooling Schemes
Breakthroughs in many of today’s cutting-edge technologies are becoming increasingly dependent upon the ability to safely dissipate enormous amounts of heat from very small areas. This ‘high-flux’ heat dissipation is encountered in many electronics applications, including computers, computer data centers, hybrid vehicle power electronics, and avionics. Phase change cooling is presently at the forefront of methods used to dissipate high fluxes while maintaining safe device temperatures. Phase change is achieved by boiling a dielectric liquid directly on the device surface. During the past three decades, our team has developed many phase change cooling schemes to meet the broad cooling demands of modern electronics. They include:
Pool boiling thermosyphon:This passive (pumpless) cooling system involves submerging the electronics in a ‘pool’ of dielectric liquid inside a sealed vessel. The heat is dissipated by boiling the liquid directly on the electronics surfaces. The generated vapor rises by buoyancy to the top section of the vessel, where it is returned to liquid state by condensing on the surface of an air-cooled or water-cooled condenser; the condensed liquid drips back to the liquid pool. Several surface augmentation techniques have been developed to enhance boiling heat transfer in thermosyphons, which consist of either modifying the surface of the device itself, or bonding a surface attachment to increase area and promote vigorous nucleation of vapor bubbles. Another enhancement technique is to grow carbon nanotubes on the device surface.
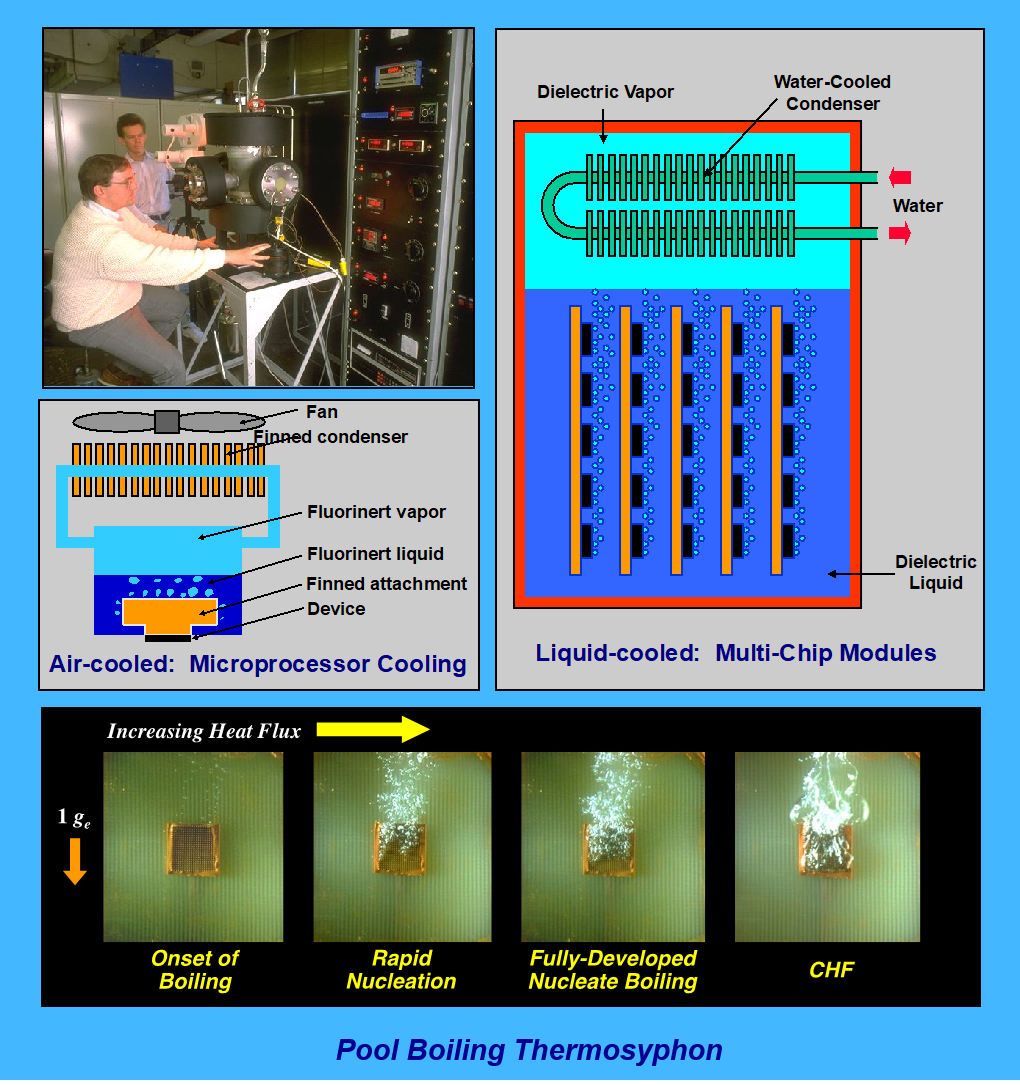
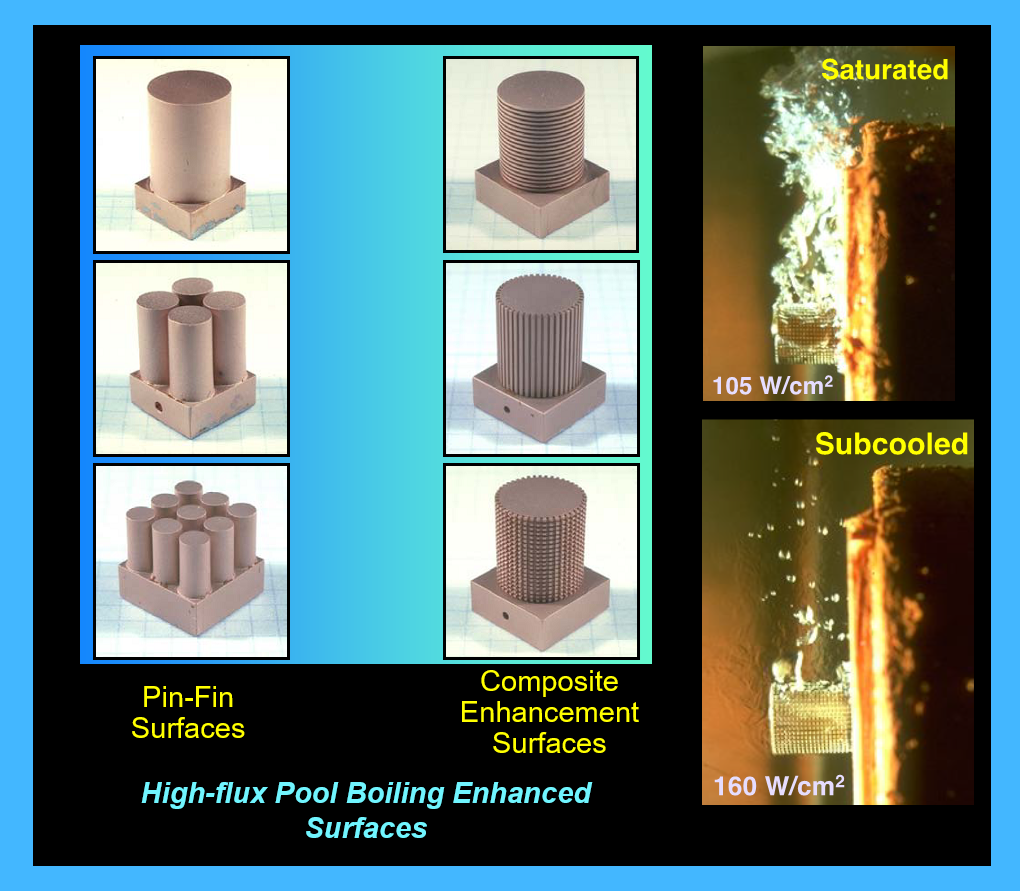
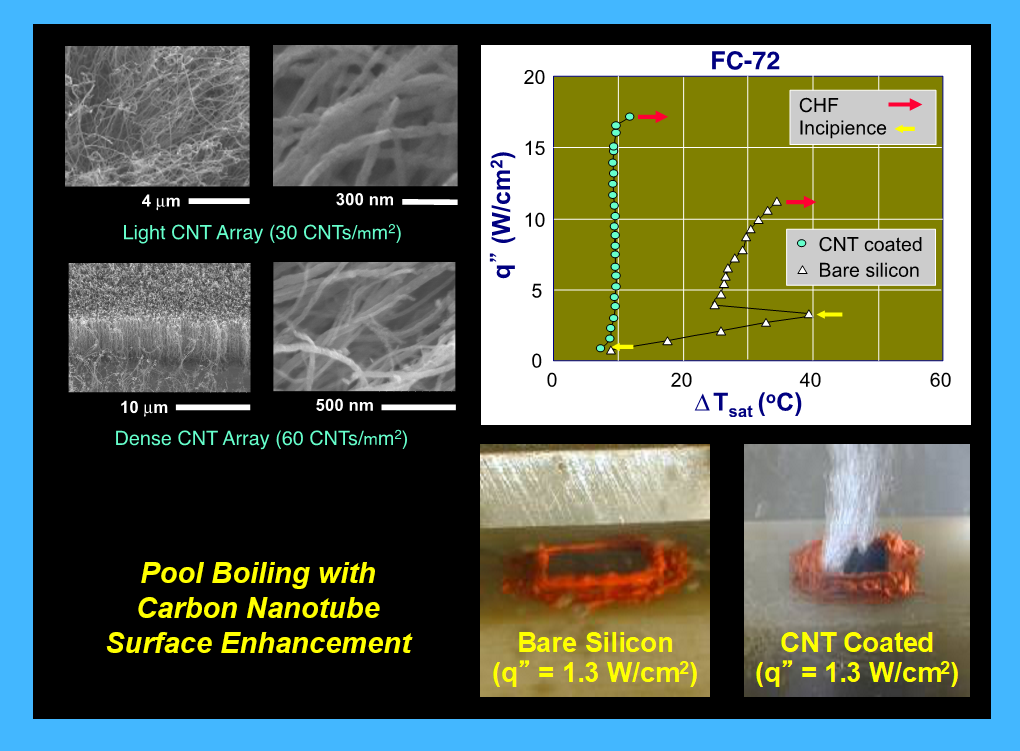
Pumpless cooling loop:
This alternative passive (pumpless) cooling system consists of two vertical parallel tubes that are connected together at the bottom, and atop to a liquid reservoir fitted with a condenser. The heat-dissipating device is connected to one tube (hot tube). As vapor is generated by boiling, average fluid density and hydrostatic pressure in the hot tube are greatly reduced compared to those in the other (cold) tube. This imbalance triggers passive fluid circulation in the loop, with liquid from the cold tube flowing downwards towards the hot tube, and liquid-vapor mixture in the hot tube rising upwards to the liquid reservoir, where the vapor is re-condensed to liquid state. This system provides great flexibility in boiler design around the heat-dissipating device.
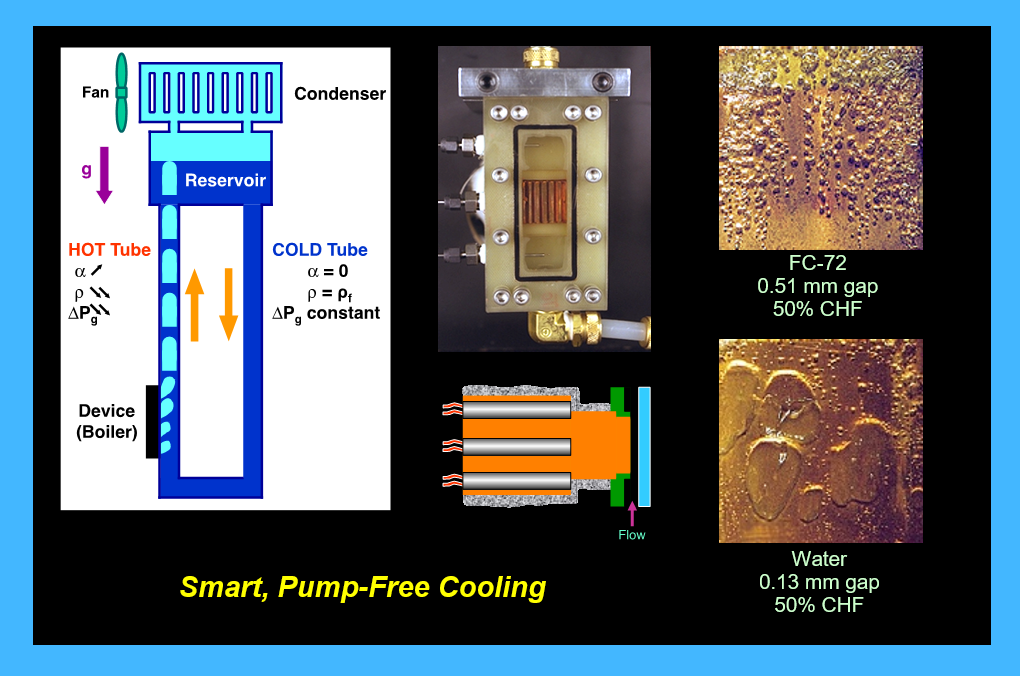
Falling-film cooling:
This system is somewhat similar to the pool boiling thermosyphon in terms of closed vessel construction and condenser design. However, most of the liquid is stored in an internal reservoir situated atop vertically stacked circuit boards. Cooling is provided by thin films that fall from the bottom of the reservoir along the circuit boards. The generated vapor rises by buoyancy to the top section of the vessel, where the vapor is returned to liquid that drips down into the reservoir. The falling-film scheme is considered ‘semi-passive’ because most of the fluid within the vessel is circulated passively by buoyancy. However, a small auxiliary pump is required to lift any un-evaporated liquid at the bottom of the vessel to the reservoir; this maintains constant liquid level in the reservoir and therefore constant film velocity along the circuit boards.
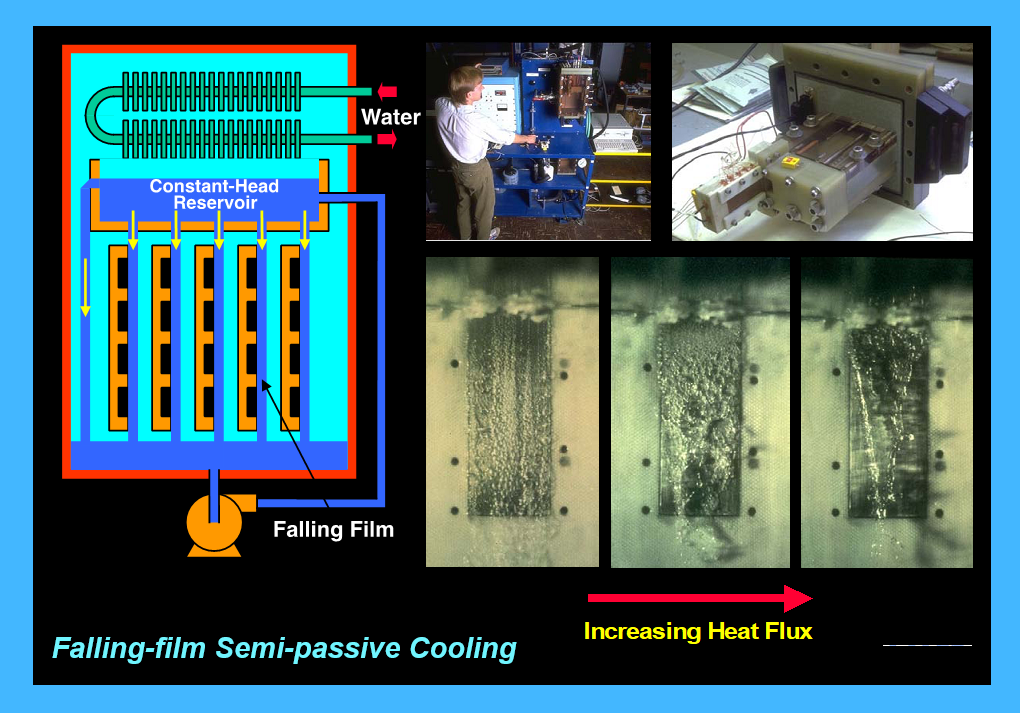
Channel flow boiling:
When passive or semi-passive cooling systems fail to tackle high device heat fluxes, a pumped flow loop is often required. The simplest of ‘flow boiling’ systems is one featuring boiling along a flow channel, which is typically formed between parallel circuit boards. The primary benefit of flow boiling is the heat transfer enhancement achieved by fluid motion. However, there is also great flexibility is controlling coolant temperature in the form of either ‘saturated boiling’, where the coolant is supplied at saturation temperature, or ‘subcooled boiling’, where coolant temperature is lower than saturation temperature. Subcooling provides the advantages of greatly enhancing upper heat flux limit, and ensuring that any vapor produced within the channel is rapidly recondensed to liquid; this simplifies the cooling loop from two-phase to single-phase liquid configuration. Like pool boiling, flow boiling can be ameliorated with the aid of surface enhancement.
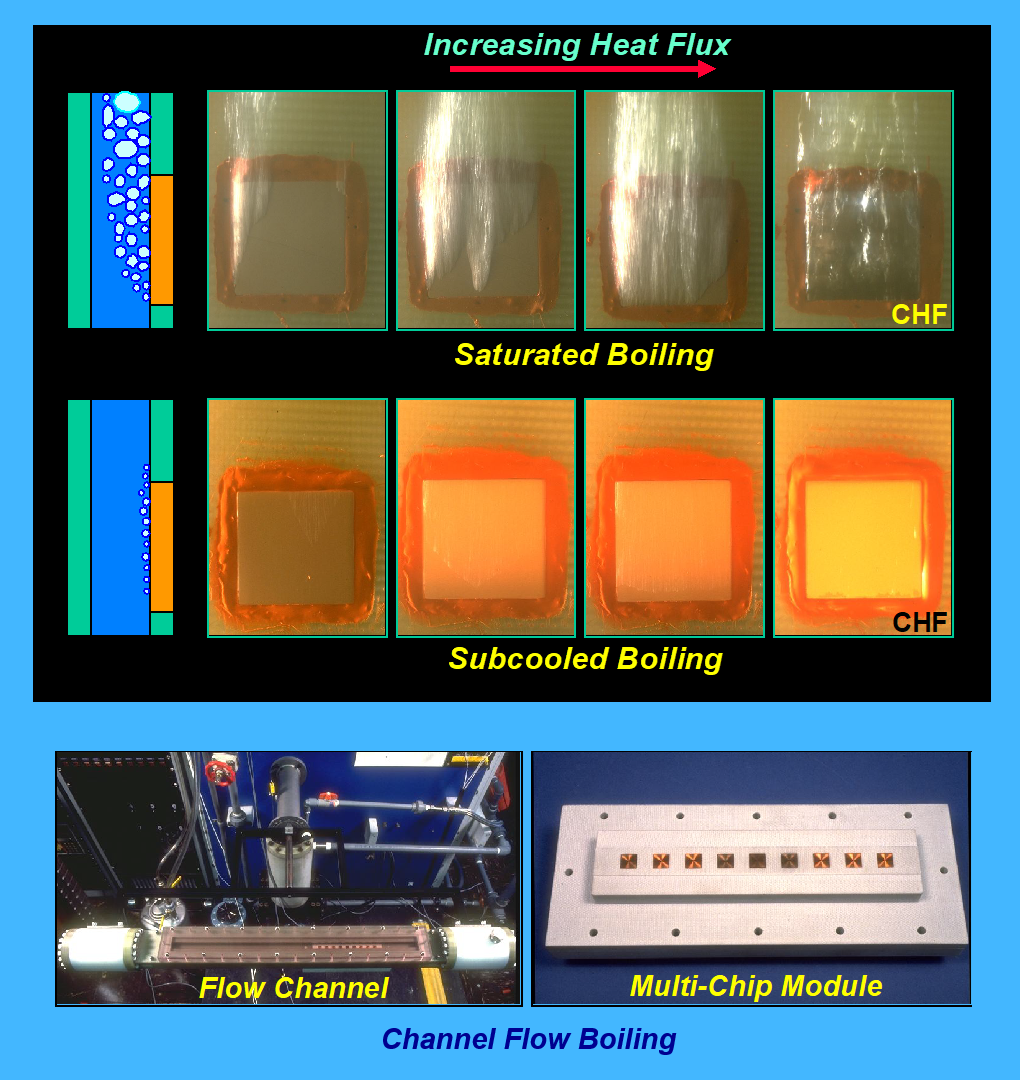
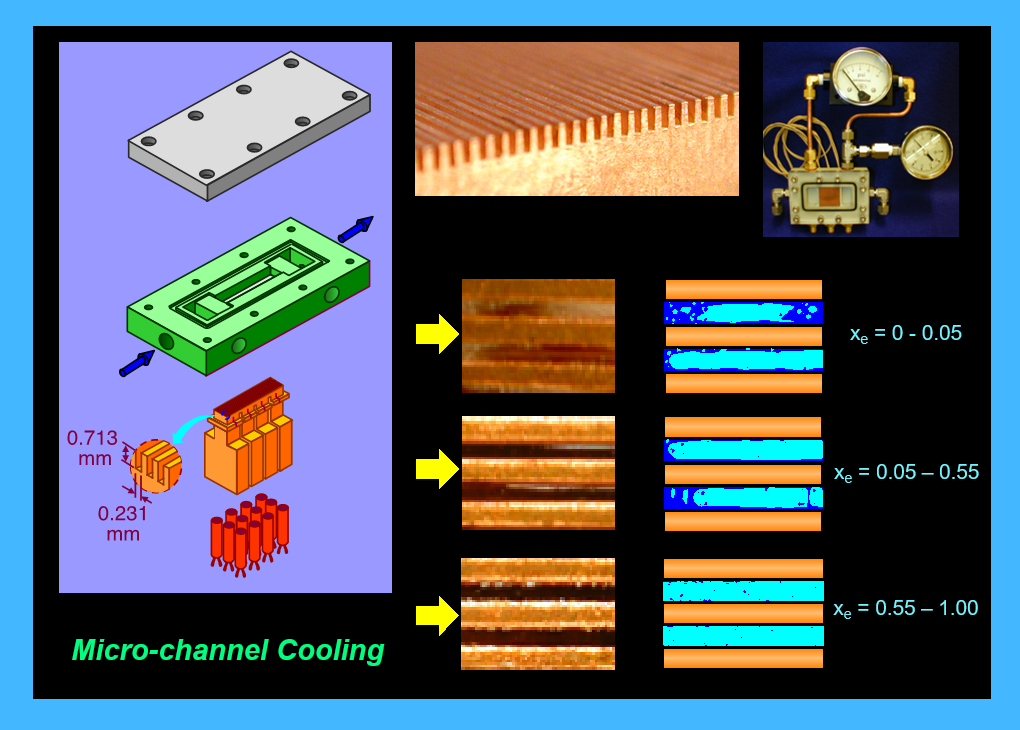
Jet-impingement cooling:
Jet impingement involves directly impacting the surface of the heat-dissipating device with a liquid jet, and boiling is generated laterally away from the impingement zone. Free (unconfined) jet-impingement cooling can be problematic, as the momentum of vapor bubbles causes splashing of liquid away from the surface. A preferred configuration is ‘confined jet-impingement’, where coolant from a slot jet is expelled laterally through two opposite flow channels. Several configurations are possible with confined jet-impingement, including cooling modules containing multiple fluid inlets (jets) and outlets. Overall, jet impingement produces very high heat transfer coefficients, but can greatly increase coolant flow rate.
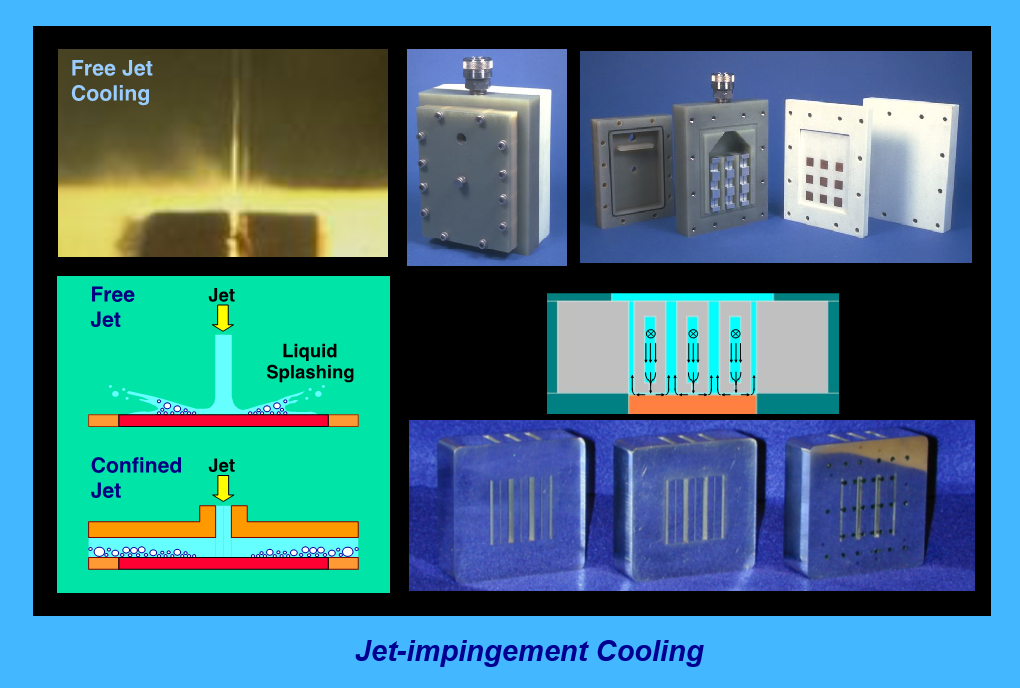
Spray cooling:
Sprays can be issued either as pure liquid (using a pressure spray nozzle) or assisted by an air stream (using an atomizing nozzle). Spray cooling of electronics involves pure liquid sprays exclusively because of difficulty separating air from dielectric liquid in a closed flow loop. Here, the liquid is broken into fine droplets before impacting the surface. The ensuing high surface area-to-volume ratio of liquid droplets greatly enhances heat transfer performance. Furthermore, the droplets acquire a broad range of trajectories, providing better cooling uniformity than jet impingement. A key difficulty in implementing spray cooling is design complexity, given the dependence of cooling performance on a large number of variables. This is why designing an effective spray cooling system requires reliance on precise predictive models and correlations.

Coolant rotation:
This specialized cooling scheme involves charging a small amount of liquid into a cylindrical vessel whose walls are lined with the heat-dissipating devices, and which is fitted with a central rotating stirrer. By spinning the stirrer at high speed, the liquid is pushed outwards, forming an annular liquid layer along the inner wall. During high-flux heat dissipation, centrifugal forces pull vapor bubbles formed along the wall inwards and liquid outwards, which helps maintain the boiling process. In fact, better performance can be realized simply by spinning at faster rotational speed.
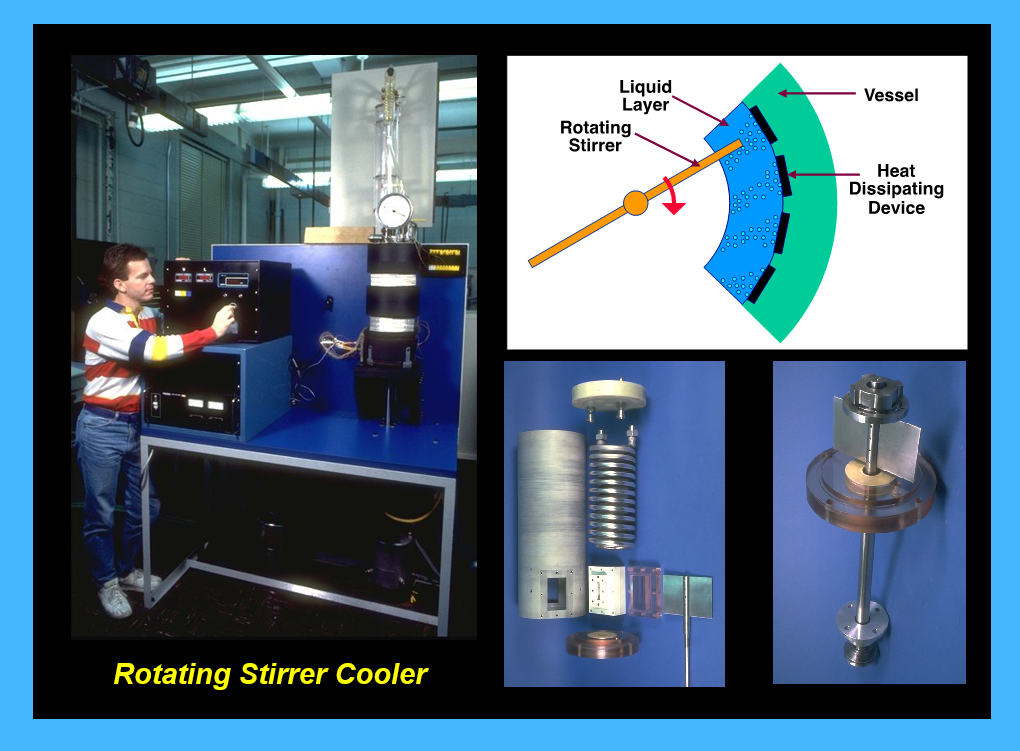
Hybrid micro-channel/jet-impingement cooling:
Micro-channel cooling and jet impingement cooling are two of the most effective thermal management schemes available today. However, despite their cooling merits, both have important drawbacks. When dissipating very high heat fluxes, micro-channel cooling can result in large pressure drop and large axial increases in both coolant and surface temperatures. On the other hand, jet impingent greatly increases coolant flow rate and causes complex flow patterns in expelled fluid, which can be hard to control inside a compact cooling package. ‘Hybrid’ micro-channel/jet-impingement cooling is a highly effective scheme that combines the cooling merits of micro-channels and jet-impingement while avoiding their drawbacks. Here, several micro-channels are formed into the surface of the heat dissipating device, and a series of jets deposit coolant into each channel. In this manner, distribution of impinged fluid is controlled through the use of parallel micro-channels. Also, better uniformity in both fluid and surface temperatures is achieved by distributing the cooling effect gradually along each channel. Using this hybrid scheme, our team demonstrated the ability to safely dissipate over 1000 W/cm2 using dielectric coolant.
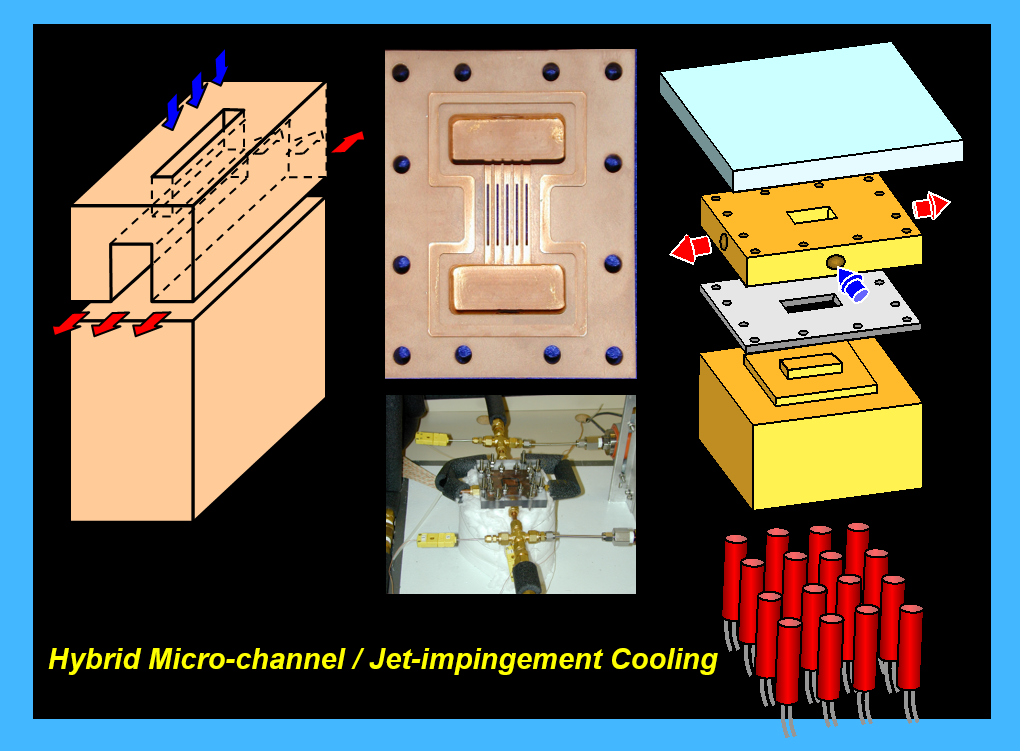