Partnering on particles A preeminent team advances research on particulate structures and manufacturing techniques across many industries.
Partnering on particles
Author: | Eric Bender |
---|---|
Subtitle: | A preeminent team advances research on particulate structures and manufacturing techniques across many industries. |
Magazine Section: | Preeminent Teams |
Article Type: | Feature |
Page CSS: | #article-banner{ background-position: 100% 25% !important; } |
From nanometer-scale powders in a drug tablet to bullet-sized pellets of chicken feeds, particulate products make up a trillion-dollar annual market in the United States. Optimizing these particulates is key for improving everything from drugs to food to specialty chemicals to biofuels — and brings major challenges in both basic and applied research.
In one example, most people probably don’t realize the sophistication of the mix of particles combined in a pill, points out Lynne Taylor, the Retter Professor of Pharmacy. “They just see a white tablet, while in reality, these systems are typically very complex, containing particles with finely tuned properties,” she says. “The microstructure of particulate products is intimately related to their performance.”
More generally, “a particle is just a more complex form of matter than a fluid,” says G. V. (Rex) Reklaitis, the Burton and Kathryn Gedge Distinguished Professor of Chemical Engineering. “For example, if I mix two different powders with different-size particles, we don’t have the ability to predict the properties of that blend. Even properties like flow are still difficult to predict. There’s no good way of even measuring the flow rate of particles.”

These are among the challenges taken on by the College of Engineering’s Designer Particulate Products preeminent team, launched in late 2014. The preeminent team brings together faculty and students to work on model-based process design for engineered particles and structured particulate products, says Carl Wassgren, team lead and Professor of Mechanical Engineering.
Wassgren’s own research highlights the broad spectrum of problems and applications the team is addressing. “Scientists and engineers don’t have good models for predicting the behavior of particulate materials during manufacturing,” he says. “We focus on developing models for predicting how powders flow, mix, break and compact. We apply these models to improve the performance of industrial processes used to manufacture a wide range of particle-based products, including pharmaceutical tablets, powdered detergents, catalysts, agrochemicals and foodstuffs.”
Collaboration is key to success in this research, and establishing the preeminent team has helped his lab and many others connect on projects that would be difficult to tackle on their own, Wassgren says.
Taylor agrees. “A major strength of Purdue is the willingness of researchers to collaborate across disciplines,” she says. “The preeminent team enables researchers from different areas to come together and share perspectives from their own disciplines. This in turn leads to synergistic research, which is greater than the sum of the parts. Innovation happens at the boundary between disciplines.”
Until now, most Purdue researchers have concentrated primarily on pharmaceutical applications. Building on these accomplishments, the preeminent team also aims to strengthen research in other industries, with agriculture a leading target.
“Agricultural particles are a lot bigger than those in pharmaceuticals, and we handle millions of tons of material, rather than kilograms as in pharmaceuticals,” notes Klein Ileleji, Associate Professor of Agricultural and Biological Engineering. “But we use similar technologies and instruments, and our courses in particle characterization teach the same things irrespective of the application. My first master’s student worked with me on biomass particles for fuel, and she went on to become a pharmaceutical scientist.”
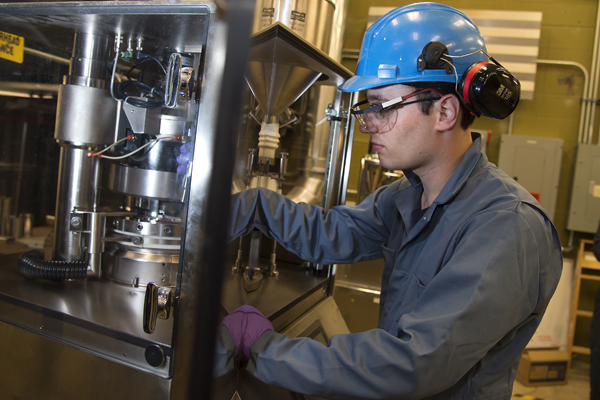
Designing drug materials
Taylor’s research seeks to unpack the complexities of drug delivery systems, doing advanced analytical characterization of their components and studying their mechanisms, especially probing into details about how the active ingredient is released.
Zoltan Nagy, Professor of Chemical Engineering, brings systems engineering models and tools to integrated process systems for particulate manufacture. One major emphasis is to develop novel control approaches to create crystal particles. “We investigate these techniques across broad scales, from microfluidic and droplet crystallization systems to large-scale industrial processes,” he says.
Nagy also works to improve control systems that aid the shift to continuous (rather than batch) manufacturing of solid products — a major trend in the pharmaceutical industry in recent years.
In related research, Reklaitis and colleagues study automated continuous tablet production lines, using a pilot plant that takes powders, blends them, granulates them and actually makes tablets.
Reklaitis also explores printable drugs. “Instead of an ink that you use in an inkjet printer, we’re taking an FDA-approved polymer, melting the active ingredient in the mixture so that it becomes a fluid, and then precisely metering and depositing it onto a placebo tablet,” he says. “Then it solidifies, we coat it and we have a dosage.”
“That is a very nice way of delivering very active drugs,” he remarks. “In many modern drugs you really need only a couple of milligrams for a dose, and it’s difficult to make those kinds of tablets using conventional powder mixing techniques.” Additionally, printable drugs also offer promise in making doses at different levels, which could allow compounding pharmacists or clinical pharmacies to deliver individualized dosing.
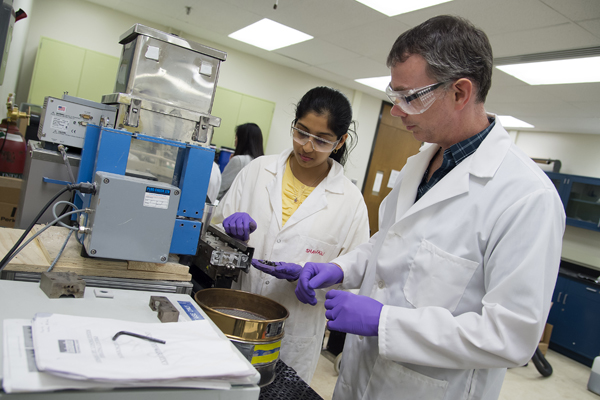
Aiding in agriculture
“We have huge opportunities in agricultural technologies related to the feed, fuel, fiber and food areas and also in agricultural chemicals,” says Ileleji. His research examines the handling of harvested grains, studying issues such as drying, particle flows, pre-processing, storage and logistics.
As part of a U.S Agency for International Development (AID) research project, Ileleji and his colleagues have developed a grain dryer for farmers in developing countries. In another project, they evaluate a feedstock called Distillers Dried Grains with Solubles, a byproduct of corn ethanol production that can be difficult to handle because it may cake and not flow easily out of a bin. In a third, they develop methods to agglomerate feedstocks, especially using materials that are currently considered waste streams, to improve their ease of handling and economics, and use as carriers for animal and plant nutrients. Additionally, Ileleji and his coworkers look at the flow of biomass materials such as switch grass flow in hoppers, and seek to create better handling equipment for these materials.
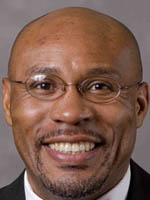
The formation of the preeminent team provided a chance to hire new faculty in agricultural research. R. P. Kingsly Ambrose returned to Purdue last fall as an assistant professor of agricultural and biological engineering. “There are lots of challenges in handling and processing these particles,” Ambrose points out. Among them, he says, if you change the temperature or the humidity of agricultural-based particles, the particle characteristics change considerably.
Wassgren, Ileleji, Ambrose and other faculty are collaborating on proposals for industrial consortia focused on agricultural “inputs” such as seed coatings and fertilizers. One effort will look at coatings that can protect seeds from drought and flood, Ambrose says. Another will tackle a problem with seed flow lubricants — powder that drifts away from the seeds can carry neonicotinoids, insecticides that are dangerous for bees. “Our issue is to make the powder stick in a better way to the coating on the seed to prevent it drifting off,” Ambrose says.
Granulated fertilizers often cake into large clumps that can release fine particles as they are handled, and these particles can pose health and environmental problems. “Several members of the preeminent team, including myself, will be focusing on improving fertilizer granule design in order to control their release rate and improve their handling qualities,” Wassgren says.

Interdisciplinary infrastructure
“No one faculty member can really afford to have 25 different tools that are state of the art for measuring various properties,” Reklaitis notes. The preeminent team offers an opportunity to boost Purdue’s suite of advanced analytical instruments that will be available to the community. Most notably, the College of Engineering is supporting the purchase of an x-ray micro computed tomography instrument, which provides extremely high resolution 3D images that will greatly improve the ability to study the internal structure of granules and compacts.
Additionally, the team is hiring a new senior technician to help run the Particle, Powder, and Compact Characterization Laboratory and the Solids Continuous Processing Pilot Plant. “We’re hoping this person will help grow a testing program to provide industry with property measurements for their particulate materials as well as to test their materials in various types of manufacturing equipment,” Wassgren says.
“Overall, Purdue is uniquely suited to lead the effort for developing the science, technology, and training pertaining to particulate processes and products,” he sums up.
“Few universities can match the concentration of faculty we have with expertise in particle-related topics or the quality of our characterization and manufacturing facilities,” Wassgren says. “We also offer course work and degree concentrations and programs related to particle science and technology.” Additionally, Purdue’s ties to the pharmaceutical and agricultural industries always facilitate new ideas with real-world applications, and provide opportunities for students to network and obtain industrial work experiences.
“We have an awful lot to learn, and an awful lot of interesting engineering research ahead,” adds Reklaitis.
Learn more about the College of Engineering’s Designer Particulate Products preeminent team,