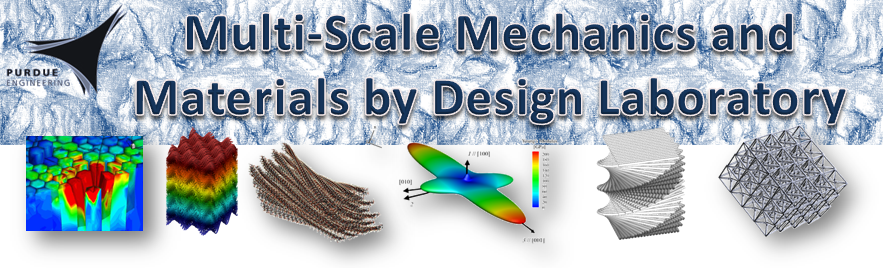
Research:
Solid mechanics applied to the multi-scale analysis and design of
advanced and novel architectured materials, interfaces and complex
structures. Our research interests lie at the interface between Solid
Mechanics and Materials Engineering with focus on the development of
novel materials that exhibit paradigm-shifting properties for various
applications that can impact the general field of infrastructure and
lightweight structural materials. Our contribution to solid mechanics
has been focused on the structure-function relationship of advanced
materials at multiple length-scales, combining state-of-the-art
computational techniques and experiments to characterize the
properties, and enabling the design of novel materials. Our arly work
on micromechanical models for materials has provided a robust framework
for combined computational/experimental investigations of
polycrystalline materials. Our contribution to fracture mechanics
includes the development of a new fracture models for thin-walled
structures and their implementation in commercial finite element codes.
We also made contributions in the area of smart materials, structures
and smart composites (with a total of 10 patents and 5 other published
patent applications). We have recently worked on solid mechanics
problems related to biological and biomimetic materials. Our group
pioneered the use of the 3D printing technology for the fabrication of
scaled-up biomimetic composites and its combination with
theoretical/computational models and experiments to unveil the most
important toughening mechanisms found in some of most impact resistant
natural materials. Our most recent work has focused on architectured
metamaterials, smart and programmable materials. See below some
examples and related papers.
For a more complete list of publications click [here]
Watch some videos related to our research:
Selected Research Projects
- Convergent Evolution To Engineering: Multiscale Structures
And Mechanics In Damage Tolerant Functional Bio-Composite And
Biomimetic Materials - DoD/MURI 2015-2018.
- CAREER: "Multiscale Investigation and Mimicry of
Naturally-Occurring Ultra-High Performance Composite Materials," NSF
Faculty Early Career Development 2013-2018.
- Phase Transforming Cellular Materials, NSF-Goali, 2015-2018.
- A Multiscale Strategy for the Modeling of the mechanical
performance of hoop and loop fasteners based on a detachment zone model
(DZM). Velcro Co. 2013-2016.
- Collaborative Research: 3D Printing of Civil Infrastructure
Material with Controlled Microstructural Architectures, NSF, 2016-2019.
- Scalable Nanomanufacturing. SNM: Roll-To-Roll Manufacturing
Of Films And Laminates Based On Cellulose Nanomaterials, NSF, 2014-2018.
- Concrete Patching Materials And Techniques An Guidelines For Hot Weather Concreting INDOT/JTRP, 2014-2016.
- Investigating The Need For Hma Drainage Layers INDOT/JTRP2015-2016.
- Toward Performance Related Specifications for Concrete Pavements INDOT/JTRP, 2014-2016.
- Damage-tolerant Biological Composites Derived from the Teeth of a Giant Chiton AFOSR 2012-2017.
- Uncovering and Validating Toughening Mechanisms in High Performance Composites, AFOSR 2012-2016.
Related Projects:
|
|
Biological and biomimetic
materials research:
Identification of
deformation and failure mechanisms of the
hierarchical structure of hard biological materials through different
length scale, with emphasis on biomineralized marine organisms such as
mollusk shells, radular teeth and crustaceans exoskeletons.
Biomimetics applied to the intelligent design of materials: Design and
modeling of synthetic nano/micro-composites mimicking hard biological
materials using bioinspired damage mitigation strategies. Development
of multiscale models for bio-inspired materials. Strong collaboration
with material scientists, chemists and biologists.
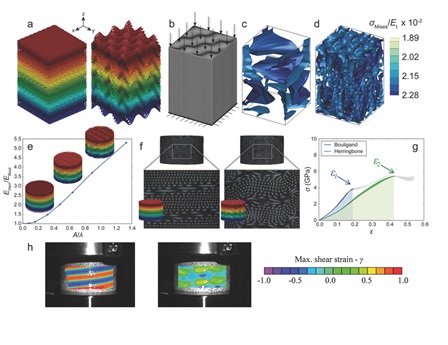
Our group is
currently focused on two remarkable hard biological materials, the
chiton’s radular
teeth and nacre. (Current work is being done in collaboration with Prof. David Kisailus' group at UC Riverside.)
|
The radular teeth of chitons, a group of elongated mollusks
that are able to erode hard substrates, has a remarkable damage
tolerance and
abrasion resistance properties. Its rod-like structured made
of of magnetite
grains, is shown to exhibit remarkable hardness and stiffness
(even harder than human enamel).
The second material is nacre,
found in certain sea shells, an excellent
example of material design and optimization for extreme strength and toughness. Although this
materials is constituted by 95% of a brittle ceramic (CaCO3), it exhibits a remarkable
toughness without sacrificing strength. In
fact, nacre is 3000 times tougher than its constituent ceramic material.
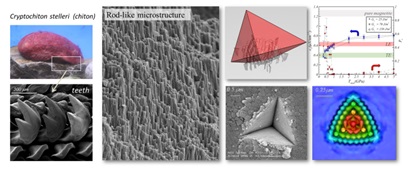
|
MURI Project: Our lab is part of a multi-university and multi- disciplinary (MURI) team "Convergent
Evolution to Engineering: Multiscale Structures and mechanics in Damage
Tolerant Functional Bio-Composite and Biomimetic Maetrials".
Awarded by the Department of Defense ($7.5M) this project will
study over 20 organisms, including mammals, reptiles, birds,
fish, mollusks, crustaceans, fosils, insects and plants to
develop strong, tough materials based on their design structures. Press
Release [@Purdue] [@UCR]
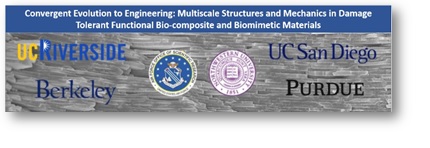
website: http://muri.ucr.edu
Collaborators: David Kisailus, Cheryl Hayashi (University of California Riverside), Joanna McKittrick, Marc Meyers (University of California San Diego), Horacio Espinosa (Northwestern University) and Robert Ritchie (University of California Berkeley).
Most relevant Papers:
Abalone/Nacre:
- F. Barthelat, H. Tang, P.D. Zavattieri, C-M. Li and H.D. Espinosa, ”On
the mechanics of mother-of-pearl: A key feature in the material
hierarchical structure”, Journal of the Mechanics and
Physics of Solids, 55(2), pp. 306-337, 2007 (Top 10 Most Cited
Journal of the Mechanics and Physics of Solids Article during the last
5 years). . [Download
PDF]
- J.E. Rim, P.
Zavattieri, A. Juster, H. Espinosa, “Dimensional
analysis and parametric studies for designing artificial nacre”,
Journal of the
Mechanical Behavior of Biomedical Materials, 4(2), pp.
190-211, 2011. [Download
PDF]
- H. Espinosa,
A.
Juster, F. Latourte, D. Gregoire, O. Loh, P.
Zavattieri, “
Tablet-Level Origin of Toughening in Abalone Shells and Translation to
Synthetic Composite Materials
”, Nature Communications, 2,
173, doi:a10.1038/ncomms1172 , 2011.
[Download PDF]
Mantis Shrimp:
- James C.
Weaver, Garrett W. Milliron, Ali Miserez, Kenneth
Evans-Lutterodt, Steven Herrera, Isaias Gallana, William J. Mershon,
Brook Swanson, Pablo Zavattieri, Elaine DiMasi, and David Kisailus, "The Stomatopod Dactyl Club: A
Formidable Damage-Tolerant Biological Hammer", Science, 336
(no. 6086), pp.
1275-1280, June 2012.
[Download PDF].
- L.K.
Grunenfelder, N. Suksangpanya, C. Salinas, G. Milliron, N. Yaraghi, S.
Herrera, K. Evans-Lutterodt, S.R. Nutt, P. Zavattieri, D. Kisailus,“Bio-Inspired Impact Resistant Composites", Acta Biomaterialia, 10(9), pp. 3997-4008, 2014. (DOI: 10.1016/j.actbio.2014.03.022) [Download PDF]
- N. Guarín-Zapata, J.D. Gomez, N. Yaraghi, D. Kisailus, P.D. Zavattieri, "Shear Wave Filtering in Naturally-Occurring Bouligand Structures", Acta Biomaterialia, 23, pp. 11-20, 2015.23, pp. 11-20, 2015. [Download PDF]
- Yaraghi, N. A., Guarín-Zapata,
N., Grunenfelder, L. K., Hintsala, E., Bhowmick, S., Hiller, J. M.,
Betts, M., Principe, E. L., Jung, J.-Y., Sheppard, L., Wuhrer, R.,
McKittrick, J., Zavattieri, P. D. and Kisailus, D. (2016), "A Sinusoidally Architected Helicoidal Biocomposite". Advanced Materials, 28(32), pp. 6835-6844, 2016 [Download PDF]
- N Suksangpanya, NA Yaraghi, D Kisailus, P Zavattieri, "Twisting cracks in Bouligand structures", Journal of the Mechanics Behavior of Biomedical Materials, DOI: 10.1016/j.jmbbm.2017.06.010, 2017 [Download PDF]
Chiton/Rod-like structures:
- L.K. Grunenfelder, E. Escobar de
Obaldia, Q. Wang, D. Li, B. Weden, C. Salinas, R. Wuhrer, P.
Zavattieri and D. Kisailus, “Stress and Damage Mitigation from Oriented Nanostructures within the Radular Teeth of Cryptochiton stelleri", Advanced Functional Materials, 24(39), pp. 6085-6240, 2014 (DOI: 10.1002/adfm.201401091) [Download PDF][Cover Page]
- E. Escobar de Obaldia, C. Jeong, L.K. Grunenfelderb, D. Kisailus, P. Zavattieri, "Analysis
of the mechanical response of biomimetic materials with highly oriented
microstructures through 3D printing, mechanical testing and modeling", Journal of the Mechanical Behavior of Biomedical Materials, 48, pp. 70-85, 2015 (Top 3 Most Downloaded JMBBM Article - July 2015) [Download PDF]
- E. Escobar de Obaldia, S. Herrera, L.K. Grunenfelder, D. Kisailus, P. Zavattieri,"Competing mechanism in the wear resistance behavior of biomineralized rod-like microstructures", Journal of the Mechanics and Physics of Solids, 96, pp. 511-534, 2016. [Download PDF]
- C. L. Salinas, E. Escobar de Obaldia, C. Jeong, J. Hernandez, P. Zavattieri, D. Kisailus, "Enhanced toughening of the crossed lamellar structure revealed by nanoindentation", Journal of the Mechanics Behavior of Biomedical Materials, DOI: 10.1016/j.jmbbm.2017.05.033, 2017 [Download PDF]
NanoHUB tools: S Lee; C. Gomez, P. Zavattieri; A. Strachan (2011), "Bio Composite Simulator," DOI: 10254/nanohub-r12273.1. link: http://nanohub.org/resources/nacresimulator
|
|
Nanomechanics of cellulose: Study
and characterization of the hierarchical structure-mechanical response
relationship of the cellulose nanocrystals (CNCs) to understand how they can
achieve their full potential for the new generation of green and
renewable materials. Development of new theories, novel multiscale
computational tools and continuum/discrete models to properly describe
and predict the mechanical behavior of cellulose nanocrystals.
Development of mesoscale nonlocal models for adhesion between
nanocrystals with strong connection to in-situ experiments with
application to the processing of cellulose-based
nanocomposites.
Collaboration with experimental and processing groups across
campus.
 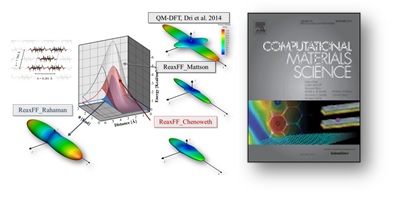
Current collaborators: Ashlie Martini, Robert Moon, Jeffry Youngblood and Jason Weiss
More information at the
NanoForestry Web site
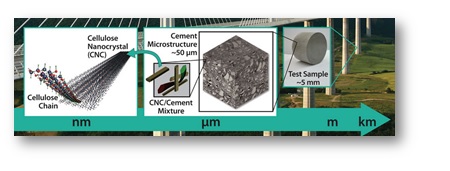
Most relevant Papers:
Modeling of Cellulose NanoCrystals (CNCs)
- F. Dri, L.H. Hector Jr., R. J. Moon,
P.D. Zavattieri,“Anisotropy
of the Elastic Properties of Crystalline Cellulose Iβ from First
Principles Density Functional Theory with Van der Waals Interactions”, Cellulose, 20(6), pp. 2703-2718, 2013. [Download PDF]
- F. Dri, R. Moon, P. Zavattieri, ”Multiscale Modeling of the Hierarchical Structure of Cellulose Nanocrystals”, in Production and Applications of Cellulose Nanoparticles. Ed. M.T. Postek, R. J. Moon, A. Rudie, M. Bilodeau, TAPPI Press. (June 2013). [Download PDF]
- F. Dri, S Shang, L.G. Hector Jr,P. Saxe, Z-K Liu, R. Moon and P.D. Zavattieri, "Anisotropy and temperature dependence
- of structural, thermodynamic, and elastic properties of crystalline cellulose Iβ: a first-principles investigation", Modelling and Simulation in Materials Science and Engineering, 22 085012, 2014.[Download PDF].
- F.L. Dri, X. Wu, R.J. Moon, A. Martini, P.D. Zavattieri, "Evaluation of reactive force fields for prediction o fthe thermo-mechanical properties of cellulose Iβ", Computational Materials Science, 109, pp. 330-340, 2015 [Download PDF]
- M. Shishehbor, F. Dri, R. Moon, P. Zavattieri "A continuum-based structural modeling approach for cellulose nanocrystals (CNCs)”, Journal of the Mechanics and Physics of Solids, DOI: 10.1016/j.jmps.2017.11.006, 2017. [Download PDF]
NanoHUB tools:
- Mateo Gómez Zuluaga; Robert J. Moon; Fernando Luis Dri; Pablo Daniel Zavattieri (2013), "Crystalline Cellulose - Atomistic Toolkit," DOI: 10.4231/D35T3G03. Link: https://nanohub.org/resources/ccamt
- Mateo Gómez Zuluaga; Fernando Luis Dri; Pablo Daniel Zavattieri; Robert J. Moon (2013), "Anisotropy Calculator - 3D Visualization Toolkit," DOI: 10.4231/D3K06X13R Link: https://nanohub.org/resources/matrix2surface
- Kuo Tian, Mehdi Shishehbor, Pablo Daniel Zavattieri (2016), "Coarse Graining of Crystalline Cellulose", DOI: :10.4231/D3930NW4D. Link: https://nanohub.org/resources/cgmcc
- Joshua Leonardo, Mehdi Shishebor, Pablo Zavattieri, "Mechanics of Crystalline NanoCellulose Nanofilm", doi:10.4231/D3TT4FW0D, https://nanohub.org/resources/cnc
CNC/Cement Composites
- Y. Cao, P. Zavattieri, J. Youngblood, R. Moon, J. Weiss "The influence of cellulose nanocrystal additions on the performance of cement paste", Cement and Concrete Composites, 56, pp. 73-83, 2014. [Download PDF]
- Y. Cao, W.J. Weiss, J.
Youngblood, R. Moon, P. Zavattieri, “Performance enhanced cementitious
materials by cellulose nanocrystal additions”, in Production and Applications of Cellulose Nanomaterials. Ed. M.T. Postek, R. J. Moon, A. Rudie, M. Bilodeau, TAPPI Press. (June 2013). [Download PDF]
- Y. Cao, P. Zavattieri, J. Youngblood, R. Moon, J. Weiss, "The relationship between cellulose nanocrystal dispersion and strength", Construction and Building Materials, 119, pp. 71–79, 2016 [Download PDF]
- Y. Cao, N. Tian, D. Bahr, P.D. Zavattieri, J. Youngblood, R.J. Moon, J.Weiss, "The influence of cellulose nanocrystals on the microstructure of cement paste", Cement and Concrete Composites, 74, pp. 164-173, 2016. [Download PDF]
|
|
|
|
Multi-functional cellular materials with programmable properties:
Design
and analysis of active-material based periodic cellular
microstructures to obtain materials that have the capability
to (1)
change and adapt their key macroscopic properties to certain changes in
the loading and environmental conditions (switchable/adaptable
mechanical properties), (2) to adapt their shapes to new configurations
(morphable and reconfigurable surfaces and structures), (3) exert
forces and induce motion for specific tasks (actuation). Study of adaptive materials with real-time
microstructural
control, patterned microstructures with controlled auxectic behavior
and self-adapatable materials.
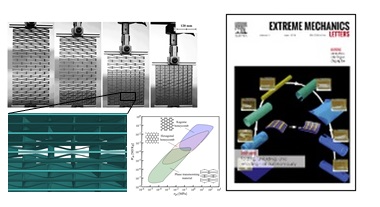 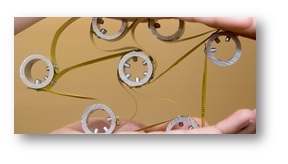
Innovative energy absorbing materials have potential uses in buildings, helmets [Purdue Press][Phys.org]
Some videos: [Programmable Cellular Materials] [Phase Transforming Cellular Materials]
|
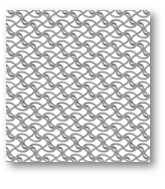 |
Most relevant Papers:
Phase Transforming Cellular Materials:
- D. Restrepo, N.D. Mankame, P.D. Zavattieri, "Phase Transforming Cellular Materials", Extreme Mechanics Letters, 2015 [Download PDF]
Programmable Cellular Materials:
- D. Restrepo,
N. D. Mankame and P. D. Zavattieri, “Shape Memory Polymer based
Cellular Materials”, Mechanics of time-dependent
materials and processes in conventional and multifunctional materials,
v. 3, Society for Experimental Mechanics , 2011.
doi:
10.1007/978-1-4614-0213-8_15.[Download
PDF]
- D. Restrepo, N. Mankame,
P. Zavattieri,"Programmable materials based on periodic cellular solids. Part I", International Journal of Solids and Structures, 100-101, pp. 485–504, 2016, 2016. [Download PDF]
- D. Restrepo, N. Mankame,
P. Zavattieri,"Programmable materials based on periodic cellular solids. Part II", International Journal of Solids and Structures, 100-101, pp. 505–522, 2016. [Download PDF]
|
|
Areas of
Expertise:
Computational
Solid/Structural Mechanics: Modeling
of damage and fracture of advanced
materials. Micromechanics, fracture mechanics and interfacial fracture
mechanics. Development of micromechanical models for brittle and
composite
materials. Multiscale modeling of crack propagation and fragmentation.. Development and application of cohesive zone
models for the
simulations of mixed mode
I/III
fracture of thin-walled structures (including metals, polymers and
composites).
Development of novel
experimental/computational procedures
for determining fracture properties. Multiscale
modeling of interfaces. Analysis of
adhesively-bonded structures. Deformation and fracture
of spot welds.
Identification of deformation and failure of
composite materials at various
length scales. Multiscale modeling of nanocomposites and
determination of the interfacial properties of
nano-reinforcements/polymer
interfaces. Development
of adaptive mesh procedures
for modeling of large deformation and fracture in ductile materials.
Detailed
numerical analysis of ductile fracture in aluminum alloys, application
of
cohesive zone models for crack propagation. Discrete Dislocation
Analysis of
ductile fracture at the mesoscale.
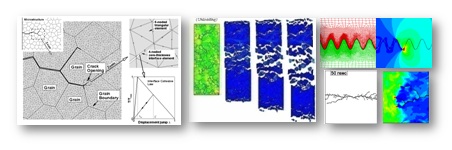
|
|
Multiscale modeling of materials: Bridging
between atomistic models and continuum mechanics through mesoscale
modeling to allow a two-way structure - property relationship for the
prediction and control of materials functionality for a more efficient
non-Edisonian approach to material discovery. Development of
atomistically-informed constitutive models for deformation and failure
of materials to characterize the influence of defects in materials
across multiple length and time scales. Multiscale approaches that aim
to bridge relevant time and length scales. Development of scaling laws
to understand the synergetic role of size, geometry and material
properties. Emphasis on nanostructured periodic materials, nano-
and micro-patterned interfaces.
Patterned Interfaces:
- P.D. Zavattieri, L.H. Hector Jr., A.F.
Bower, “Determination of
the mode-I effective fracture toughness of a
sinusoidal interface between two elastic solids”, International Journal
of Fracture, 145 (3), pp. 167-180, 2007. [Download
PDF]
- P.D.
Zavattieri, L.H. Hector Jr., A.F. Bower,
“Cohesive zone simulations of crack
growth along a rough interface between two elastic plastic solids”,
Engineering Fracture Mechanics, 75(15),
pp. 4309-4332, 2008.[Download
PDF]
- F. Cordisco,
P.D. Zavattieri, L.H. Hector Jr., A.F. Bower, “Toughness of a patterned
interface between two elastically dissimilar solids”, Engineering Fracture Mechanics, 96, pp. 192-208, 2012. [Download PDF]
- F. Cordisco, P. Zavattieri, L.G. Hector, A. Bower ,“On the mechanics of sinusoidal interfaces between dissimilar elastic-plastic solids subject to dominant mode I", Engineering Fracture Mechanics , (DOI:10.1016/j.engfracmech.2014.06.004)[Download PDF]
- F.A. Cordisco, P.D. Zavattieri, L.G. Hector Jr., B.E. Carlson, "Mode I Fracture Along Bonded Sinusoidal Interfaces", International Journal of Solids and Structures, 83, pp. 45–64 2016. [Download PDF]
Crack Propagation in thin-walled structures:
- P.
Zavattieri, “Modeling of crack
propagation in thin-walled structures with a cohesive model for shell
elements”,
special issue on Computational Mechanics of Journal of
Applied Mechanics,73(6),
pp. 948-958,2006.
(Top 10 Most Downloaded
Articles -- October 2006) [Download PDF]
- M.A. Sutton, J.Yan, X. Deng. C.-S Cheng, P. Zavattieri,
“Three-dimensional
digital image correlation to quantify deformation
and crack-opening displacement in ductile aluminum under
mixed-mode I/III loading”, Journal of Optical
Engineering, 46(5), 051003, 2007. [Download PDF]
- J.-H
Yan, M. A. Sutton , X. Deng, Z. Wei and P. Zavattieri, “Mixed-mode
Crack
Growth in Ductile Thin-sheet Materials under
Combined In-plane and Out-of-plane
Loading” International
Journal of Fracture, 160(2), pp. 169-188 2009.[Download
PDF]
- J. Yan, M.
Sutton,
Z. Wei, X. Deng, P. Zavattieri, “Hybrid
Experimental and Computational Studies: Combined Compression-Bending
Fracture of Edge-Cracked Polypropylene Specimens”,
Fatigue and
Fracture
of Engineering Materials and Structures,
33(12),
pp. 791–808, 2010.[Download
PDF]
- Z.
Wei, X. Deng, M.A. Sutton, J. Yan, C.-S. Cheng, P. Zavattieri, "Modeling of Mixed-Mode Crack
Growth in Ductile Thin Sheets under Combined In-Plane and Out-of-Plane
Loading", Engineering
Fracture Mechanics, 78(17), pp. 3082-3101,
2011. [Download
PDF]
- X. Chen, X. Deng, M. A. Sutton, P. Zavattieri,“An Inverse Analysis of Cohesive Zone Model Parameter Values for Ductile Crack Growth Simulations", International Journal of Mechanical Sciences, 79, pp. 206-215, 2014. [Download PDF]
Adhesive Joints:
- S. Li, M.D. Thouless, A.M. Waas, J. Schroeder, P.D. Zavattieri,
“Mixed-mode
cohesive-zone models for fracture of an adhesively-bonded
polymer-matrix composite”, Engineering Fracture Mechanics,
73(1), pp. 64-78, 2006. (Most cited article in
the 2005-2009 period Award)
[Download
PDF]
- S. Li, M.D. Thouless, A.M. Waas, J. Schroeder, P.D. Zavattieri,
“Competing failure
mechanisms in mixed-mode fracture of an
adhesively-bonded polymer-matrix composite”, International Journal of Adhesion
and Adhesives, 26(8), pp. 609-616, 2006. [Download
PDF]
- S. Li, M.D. Thouless, A.M. Waas, J. Schroeder, P.D. Zavattieri, “Use of
Mode-I cohesive-zone models to describe the fracture of an
adhesively-bonded polymer-matrix composite”, Composites Science and Technology,
65(2), pp. 281-293, 2005.[Download
PDF]
- Li, M.D. Thouless, A.M. Waas, J. Schroeder, P.D. Zavattieri, “Use of
a cohesive-zone model to analyze the fracture of a fiber-reinforced
polymer–matrix composite”, Composites Science and Technology,
65(3-4), pp. 537-549, 2005. [Download
PDF]
- Sun, M.D. Thouless, A.M. Waas, J.A.
Schroeder, P.D. Zavattieri “Ductile-brittle
transition in the fracture of plastically-deforming adhesively-bonded
structures.
Part I: Experimental
studies”,
International Journal of Solids and
Structures, 45 (10), pp.
3059-3073, 2008. [Download
PDF]
- C.
Sun, M.D. Thouless, A.M. Waas, J.A.
Schroeder, P.D. Zavattieri “Ductile-brittle
transition in the fracture of plastically-deforming adhesively-bonded
structures. Part II: Numerical
studies” International
Journal of Solids and
Structures, 45 (17), pp. 4725-4738, 2008. [Download PDF]
- C.
Sun, M.D. Thouless, A.M. Waas, J.A.
Schroeder, P.D. Zavattieri, “Rate
Effects for Mode-II Fracture of Plastically Deforming,
Adhesively-Bonded
Structures", International
Journal of Fracture, 156(2), pp. 111-128, 2009. [Download
PDF]
- C.
Sun, M.D. Thouless, A.M. Waas, J.A.
Schroeder, P.D. Zavattieri, “Rate
Effects for Mixed-Mode Fracture of
Plastically Deforming, Adhesively-Bonded Structures," International
Journal of Adhesion and Adhesives, 29, (4), pp.
434-443, 2009.[Download
PDF]
|
|
|
|
[Complete list of publications]
Funding: - NSF
- AFOSR
- Joint Transportation Research Program (INDOT)
- Forest Product Laboratory (USFS)
- General Motors Reserach and Development
- Velcro
- Purdue Research Foundation
- Network for Computational Nanotechnology (NCN)
| 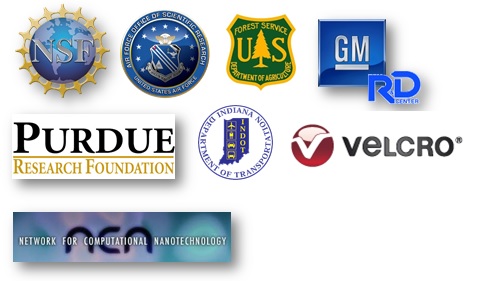
|
Home | Research | People |
Publications | News | Media |
Teaching | Contact
us © 2017
Pablo D. Zavattieri | Site designed by P. Zavattieri
|