Facilities
With more than 15,000 square feet of testing space, Maha is the largest academic fluid power lab in the country. We have 13 test rigs, multiple diagnostic labs, and real-world equipment including tractors, excavators, and cranes. Maha also has extensive meeting space and offices, perfect for hosting conferences or educational events.
Test Rigs >>>
OLEMS Test Rig
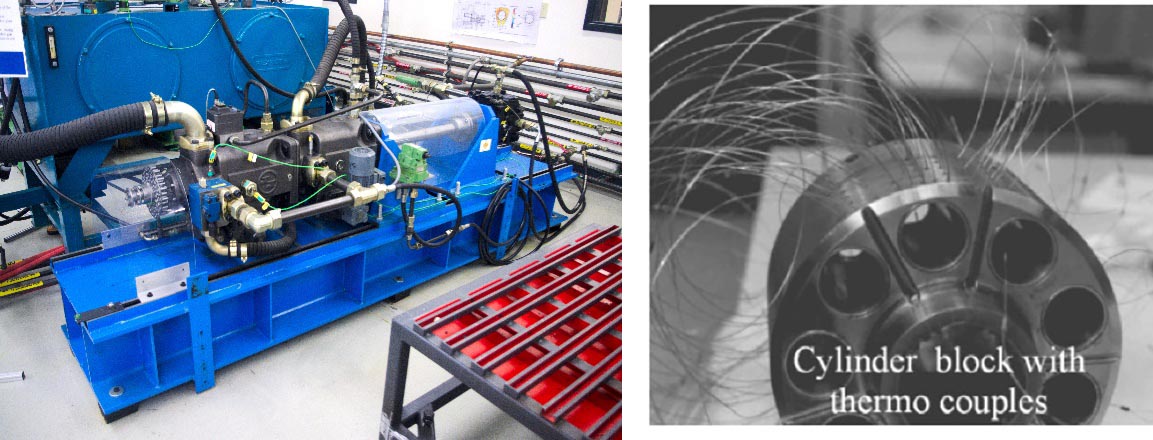
Sixty thermocouples are mounted around a single cylinder to measure the temperature field during operation of the pump. Telemetry is used for data transfer from the rotating cylinder block to the data acquisition board. The measured results are used for the development of a more precise method to calculate the non-isothermal gap flow between piston and cylinder in swash plate type axial piston machines. Results of the test rig serve to support the modeling activity on axial piston pumps.
Elastohydrodynamic Test Rig

The EHD (elastohydrodynamic) Test Rig designed by M. Ivantysynova and H. Everth provides key insight into one of the most critical lubricating interfaces of axial piston machines of swash plate design― namely, the piston-cylinder interface― by allowing its temperature and pressure fields to be measured over a 1,620-point grid. The temperature and pressure distributions of this interface owe their import not only to the fluid properties they govern (density, viscosity, bulk modulus), but also to the material deformations they cause, which are on the same order of magnitude as the fluid film thickness, and therefore significantly transformative to the gap height and, by extension, leakage and power loss through the interface. The EHD captures this valuable information through the use of a single-piston pump. In this unit, a wobble-plate construction causes a piston to move in and out of a measurement block. Pressure and temperature sensors are set into the material of the measurement block in order to gather pressure and temperature information directly at the lubricating interface. The measurement block can be turned to 180 different angular positions, thus allowing the nine inset pressure sensors and nine inset temperature sensors to
each cover 1,620 measurement points.
Tribo Test Rig
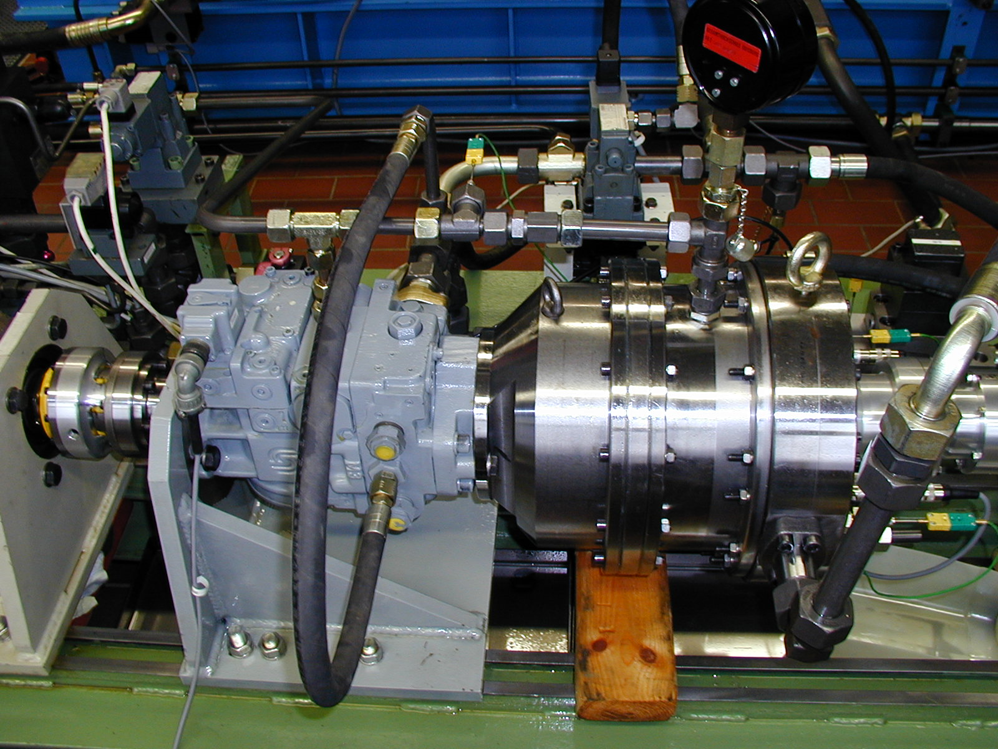
The Tribo pump is designed to measure the dynamic axial and circumferential friction forces between the piston and cylinder. A specially designed replaceable bushing is separated from the rotating cylinder block by a series of hydrostatic bearings. The bushing is held in place by the mechanical connection to the force sensor. Any net friction force acting on the bushing will therefore be directly measured by the force sensor. Data is transmitted wirelessly from the rotating kit to a data acquisition via a telemetry system. The Tribo pump can be operated in either pumping or motoring mode at speeds up to 1800 rpm. Measurements can be taken during steady state conditions at different oil viscosities. The experimental bushing and piston pair in the Tribo test rig can be readily replaced. This provides the capability to examine the impact of novel materials and surface micro-geometry on the behavior of this important lubricating interface.
Transmission Test Rig
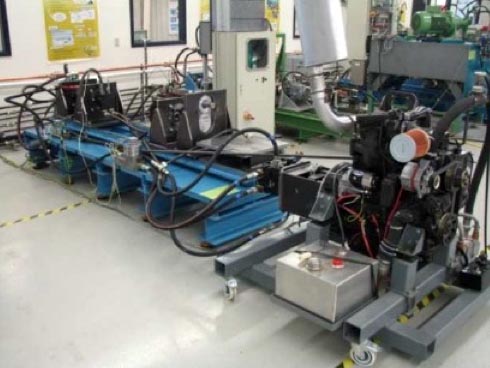
The HIL Transmission Test Rig is one of Maha’s more versatile dedicated test beds and serves as a demonstrator for hydrostatic, series hybrid, and Maha’s novel Mode Switching Hybrid (MSH) hydraulic transmissions for light duty automotive applications. It has been used to train and teach students the principles related to the operation and testing of hydraulic transmissions and has supported numerous theses. Due to its design, the HIL Transmission Test Rig can be used to study control strategies, thermal behavior, and pressure pulsations in the transmission lines for each of the three transmission architectures listed above.
Prius Transmission Test Rig

This is one of two HIL transmission test rigs in the Maha lab which has been designed for the purpose of testing powertrains and powertrain control concepts. This test rig uses two secondary controlled hydraulic units to simulate the engine and road loads enabling dynamic drive cycle testing of transmissions for vehicles up to a class 6 truck in size. Pictured is a series hydraulic hybrid power split transmission intended for use in a Toyota Prius.
Performance Characteristics
Engine simulator: 900 Nm @ 1800 rpm
Load simulator: 900 Nm @ 1800 rpm
Steady State Test Rigs

With a dedicated test rig platform including an electric motor and access to the Maha Hydraulic Power Supply, steady state and some dynamic characteristics for different pump and motor types can be directly measured. This test rig can be configured in multiple ways to support testing of a wide range of component sizes. Equipped with a torque meter rated to 1000 Nm, high pressure lines rated to 450 bar, various thermocouples and flow meters, the test rig can recreate a wide range of operating conditions up to a maximum speed over 3000 RPM. These measurement capabilities have been used in the past to develop in-house pump loss models for the validation of advanced pump models and the simulation of realistic system level performance.
Joint Integrated Rotary Actuator Test Rig
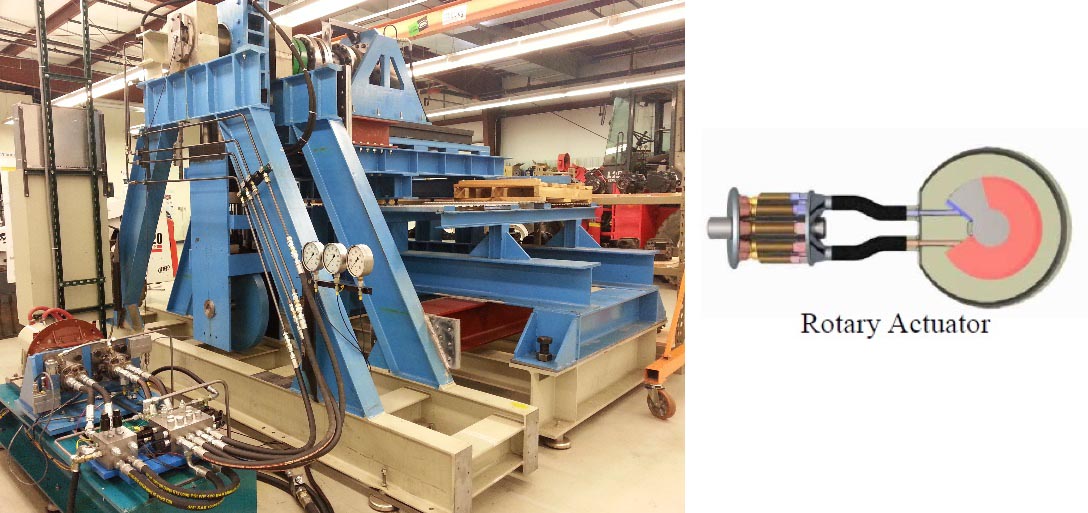
The joint integrated rotary actuator (JIRA) test rig was originally built for the experimental investigation of displacement controlled (DC) rotary actuators. The ideas and technologies developed for and implemented in this test rig have been utilized as end effector drives in mobile robots and large manipulators as well as for applications such as stabilizers in cars or ships. The test rig has also been used to investigate and demonstrate pump switching for the sequential operation of multiple actuators and has led to new control concepts focused on actuator operability. As a demonstrator, the JIRA has been utilized to show that DC actuation can be used for precise motion control with a variety of control law architectures.
Max. Torque: 30000 Nm
Max. Pressure: 350 bar
Max. Power: 30 kW
Multi Purpose Test Rig
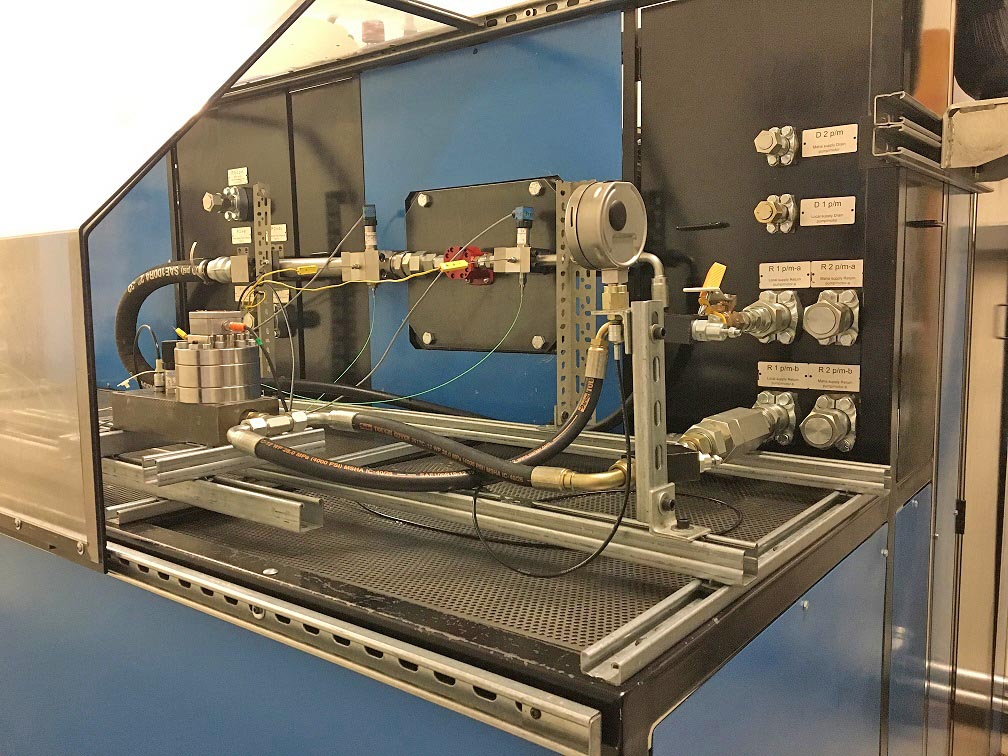
The Multi-Purpose Test Rig (MPTR) at Maha Fluid Power Research Center allows for testing a wide variety of fluid power components and systems at pressures up to 300 bar. A variable frequency servo motor can drive a pump at any speed for performance characterization. The pump mounting configuration is highly modular and can easily accommodate nearly any commercial unit. Another electric motor and pump incorporated in the test rig can be used to supply flow for testing hydraulic systems or components other than pumps. A fluid conditioning system in the MPTR actively controls the local oil temperature, and a fluid recovery system catches and recycles any oil that flows out of lines during circuit reconstruction. The data acquisition and control system has capabilities to record data from nearly any sensor type and to make fast online computations for electronic controller development. For pump testing, the MPTR has capabilities to measure speed, torque, flow, temperature, mean pressure, and small variations in pressure by using state-of-the-art piezoelectric pressure sensors.
Gerotor Test Rig
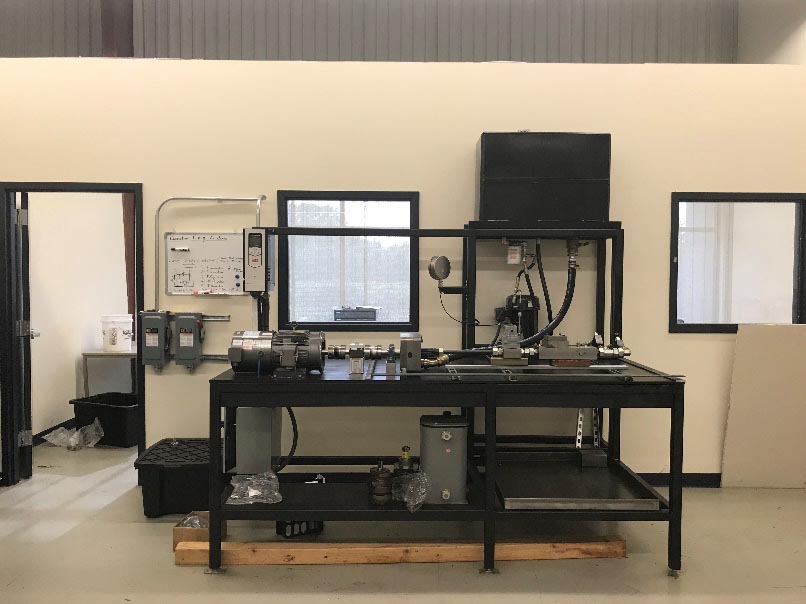
A test rig for testing low pressure circuits typical of automotive applications was created in 2018. A state-of-the-art data acquisition system was specifically designed to perform the Gerotor pump characterization in terms of dynamic and steady state measurements including pressure pulsation and pressure flow-rate pairs. These units are used for braking systems, engine lubrication, fuel injection. The installed power is 10 kW, and the maximum operating pressure of the test station is 250 bar, although most of the tests are run at pressure below 30 bar. The test rig is also equipped with a conditioning system, to filter and regulate the temperature of the working fluid.
Active Vibration Damping Test Rig
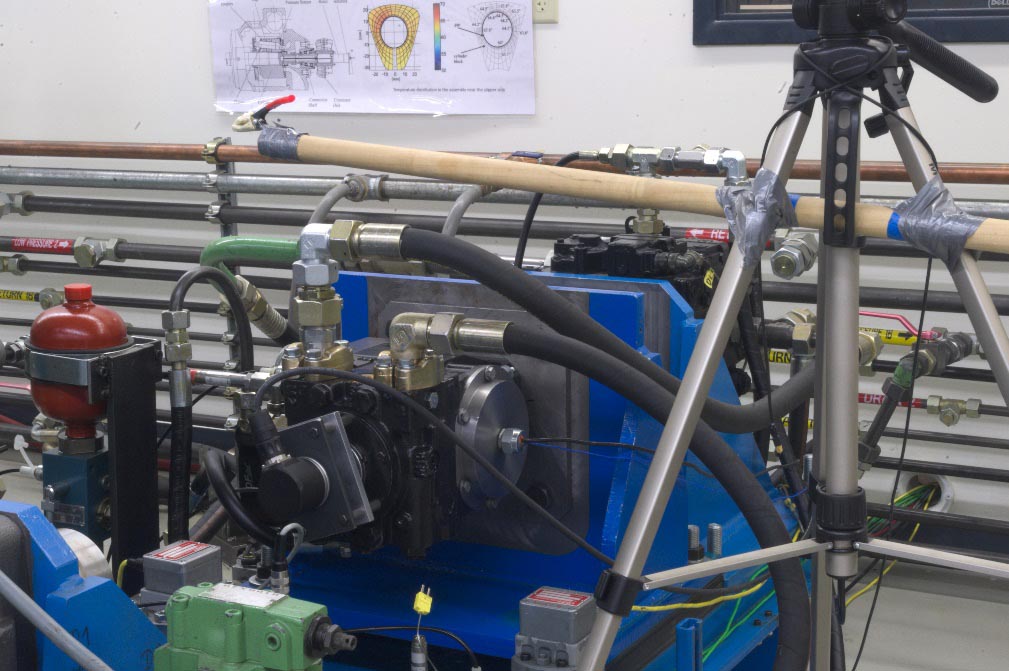
A 75 cm
3/rev pump is modified to implement active vibration control using the swash plate. One tri-axial acceleration sensor and one angle sensor is installed on the swash plate and a high speed servovalve is attached on the back of the pump case. The higher harmonic least mean square algorithm gives signal to the servovalve to generate destructive interference force for the swash plate moment. An experimental test is conducted using Labview FPGA interface via cRIO to investigate the performance of active vibration control.
Endurance Test Rig
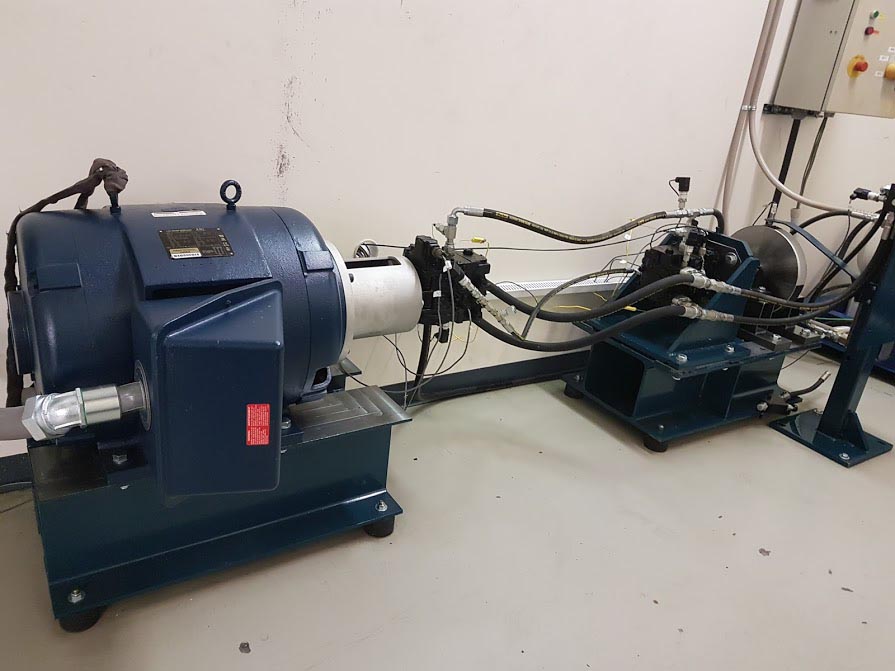
The Maha Endurance test rig is used to verify long term reliability of existing and newly designed hydraulic pumps and motors. Features include:
- Customizable pre-defined speed cycles and loading conditions
- Controllable temperature and pressure inlet conditions.
- Unsupervised long duration (1000+ hours) test.
- Online performance monitoring to prevent significant machine damage
- Automatic reporting of system alarms
- Modular and scalable Data Acquisition and Control interface
Water Hydraulic Test Rig
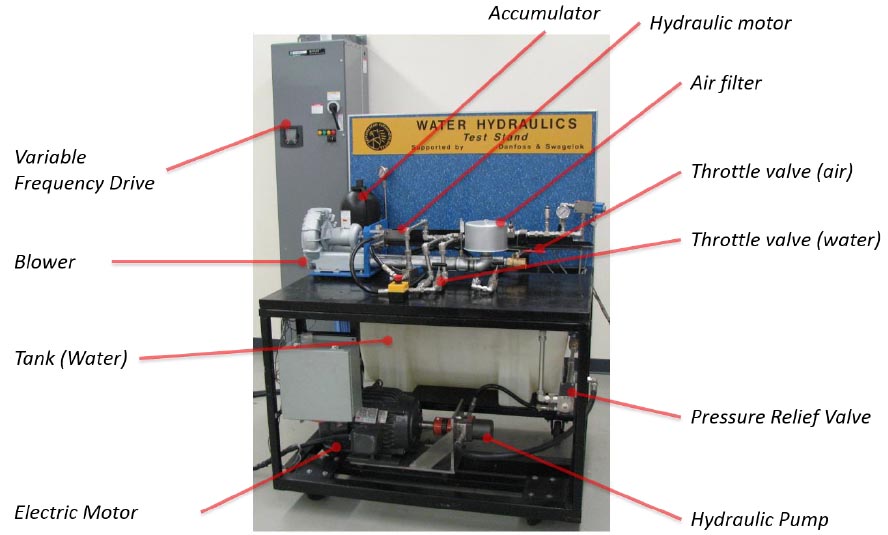
A test rig for testing and demonstrating the operation of high-pressure water hydraulic components and systems is present at Maha Lab. The test rig operates with distilled water and it is used for both educational and research purposes. For the educational component, the test rig is suitable to perform steady-state characterization of the hydraulic pump, of the hydraulic motor, and of the metering valves. The test rig can also demonstrate the operation of open center hydrostatic transmissions. For research purposes, the water hydraulic test rig supports USDA-funded research on novel water hydraulic components for fluid power systems.
Performance:
Max pressure: 150 bar
Max flow rate: 40 L/min
Load Sensing Test Rig

The main goal of this test rig is to visually and experimentally demonstrate the theoretical concepts of Load Sensing systems. These types of systems have been used in mobile machinery for decades and still are been utilized. Understanding this system will open a wide range of possibilities for the students. Load-sensing systems are used to improve hydraulic systems efficiency and controllability in either a single or multiple actuators present hydraulic circuit. With the aid of this rig, the students can visually and experimentally see the differences in pre-compensated and post compensated load sensing systems and the difference between a single and multiple user. Calculations of energy efficiency are also possible with the use of this rig. The student has a complete learning experience. The rig along with its NI hardware and LabVIEW software interface is versatile, safe and state of the art tool needed to better understand hydraulic load sensing.
Back to top <<<
Vehicles >>>
Agricultural Tractor

Hydraulics has an extensive application field, one of these branches being agriculture. The study of energy efficiency has always been a priority in the engineering field. Little or no information is known about hydraulic efficiency in agricultural tractors. With the help of the reference machine NH T8.390, we plan to understand the energy consumption distributions and propose new technologies to increase the hydraulic efficiency in these machines. Experimental testing and modeling done in this lab will help us reach this objective.
Wheel Loaders
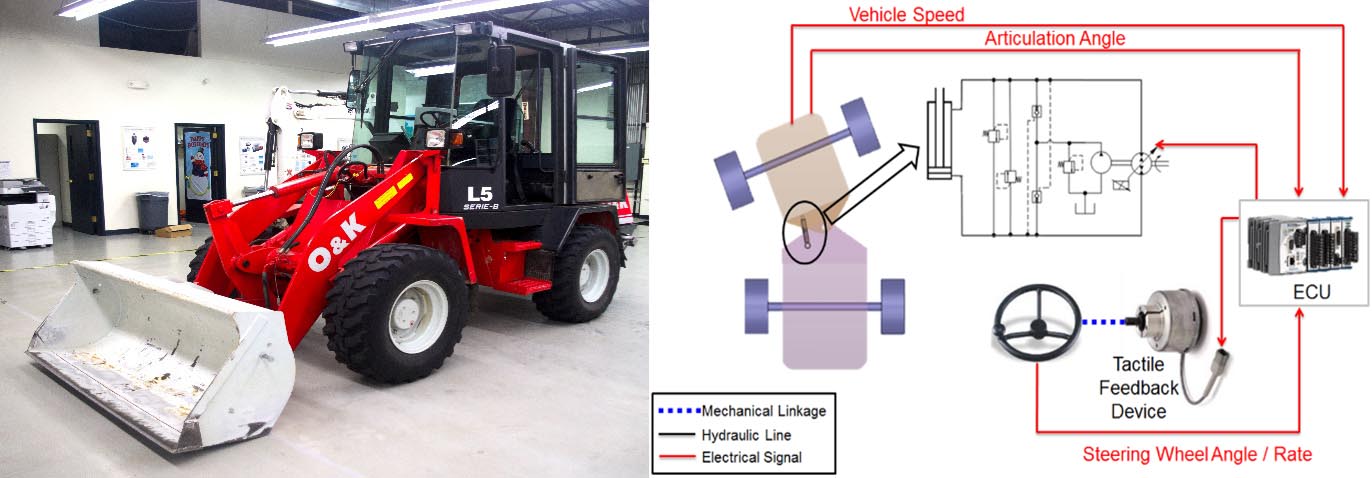
The system-level research done at Maha encompasses a wide variety of machines. A large wheel loader has been loaned to the lab for system modeling and controls development research work. This wheel loader is used as a resource for projects focusing on vehicle dynamics, active oscillation reduction, traction control, and others.
Multiple computer simulations have been developed to model various subsystems of the wheel loader. Furthermore, much work has been done in instrumenting and modifying this prototype vehicle in order to allow for these computer models to be validated and the corresponding control structures tested on real-world conditions.
A novel displacement controlled electrohydraulic steer-by-wire system has been implemented on a compact wheel loader with excellent results. A steer-by-wire system controls the steering of the machine through the use of electrical signals. A throttle-less displacement controlled system replaced the conventional valve controlled steering system. The vehicle speed, articulation angle, and the steering wheel angle/rate are fed into the ECU on board the machine, and then a command signal is sent to the pump control system to appropriately adjust the steering cylinder position. Additionally, a tactile feedback device provides resistance to the steering wheel for the operator, depending on the speed of the vehicle. These modifications have improved overall fuel efficiency by 14.5% and increased steering productivity by 22.6%. The steer-by-wire compact wheel loader is also equipped with a remote control to steer the vehicle at a distance. This opens the door for efficient and simple autonomous steering of off-highway mobile equipment.
Skid-Steer Loader
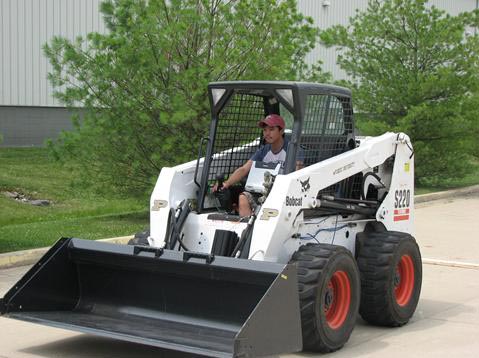
Pump-controlled technology has been demonstrated on compact machinery at the Maha Fluid Power Research Center. For the purpose of demonstrating different controls for the next generation of skid steer loaders through displacement control, a Bobcat skid-steer loader was modified. To improve the ride comfort and machine performance, advanced control strategies are currently being researched to improve our already existent active vibration damping algorithms. Along with vibration damping, a robust path planning algorithm for forklift function is being designed which will ensure that the bucket remains in horizontal position at every boom position so that it does not spill its contents. In addition to this, control algorithms are also being developed to achieve smooth speed shift between the two displacement modes of the drive motors. The skid-steer loader has been equipped with new electronics to add data acquisition and control capabilities.
Displacement Controlled Hydraulic Hybrid Excavator
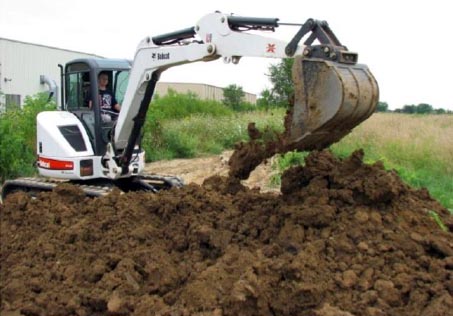
A Bobcat mini-excavator has been used at Maha for studies on displacement controlled technology, pumps switching and engine power management concepts, to improve fuel economy. The hydraulic system of the excavator was completely renewed, with respect to the commercial machine, to implement a hydraulic system based on a “valve-less” technology. Recently, the excavator was tested by professional operators by an independent company, demonstrating advantages of fuel consumption and productivity gains near to 50%. In the recent years, the hydraulic system was modified to include hydraulic accumulators, to implement a hydraulic hybrid solution which is able to recover energy during dissipative phases of operation. The hybrid system also permits to lower the power request at the combustion engine as well as the need of oil cooling.
Hydraulic Crane
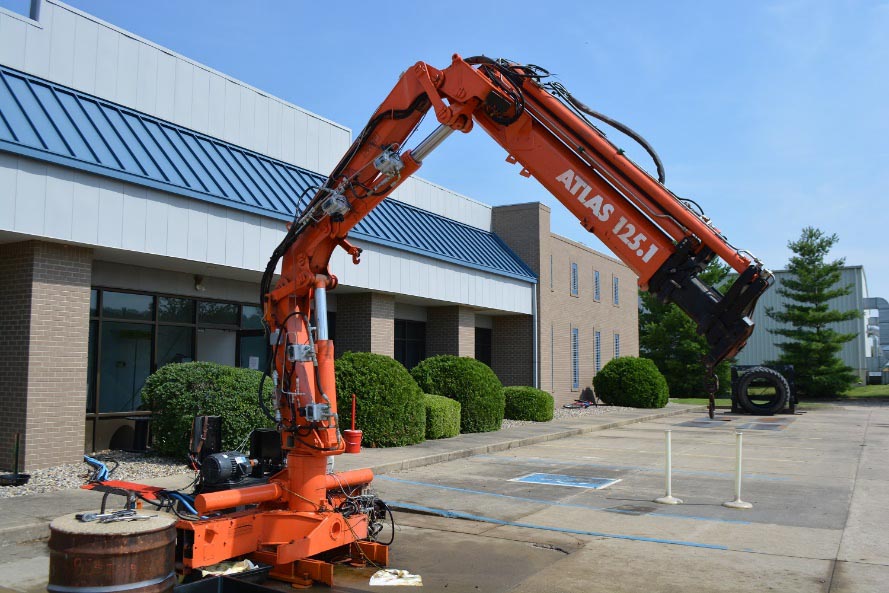
In 2012, a mid-size hydraulic crane (ATLAS 125.1, max extension: 20 m) was installed at Maha fluid power research center. These machines are characterized by an oscillatory behavior and high energy consumption. Therefore, new control strategies and new configurations for valve-controlled hydraulic systems are proposed to improve the controllability, productivity of the machine and safety of the operator. Novel oscillation damping techniques are tested on this machine showing high margin (>30%) of potential for vibration reduction without changing state-of-art technology of hydraulics components. Numerical models of different valves are created to improve the energy consumption related to the load holding machine. These numerical models are also validated successfully with the experimental results obtained from the crane.
Hydraulic Hybrid SUV
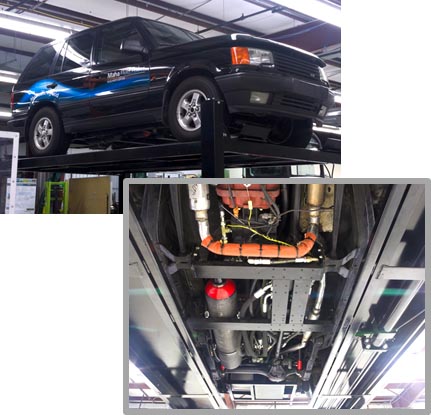
The Maha Hydraulic Hybrid SUV is a demonstration vehicle developed in the lab to enable real world testing of hydraulic hybrid transmission architectures and control strategies. Among the most valuable tests is the ability to explore the impact of various control strategies on drivability and driver perception, which is extremely difficult to do in simulations and on HIL test beds. The vehicle is also equipped to allow for direct measurement of fuel consumption and a throttle-by-wire gasoline engine to allow the exploration of new power management strategies. The Maha Hydraulic Hybrid SUV has been featured in three MS theses and two PhD theses since it was first completed and put into commission in 2015. Current research topics, in addition to ongoing development of efficient control strategies for the novel Mode-Switching Hybrid (MSH) architecture, include engine speed control, power management supervisory controls, and drivability assessments.
Performance data:
Engine: 142 kW gasoline
Unit 1: 100 cc/rev
Units 2,3: 75 cc/rev
High pressure accumulator: 32 l
Maximum system pressure: 450 bar
Back to top <<<
Infrastructure >>>
Main Hydraulic Power Supply
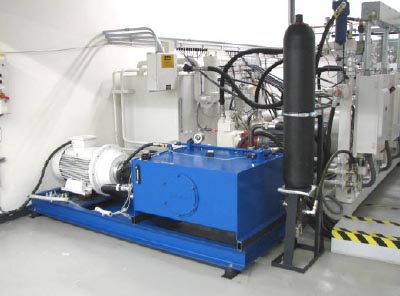
The Maha hydraulic power supply is equipped with a 2000 L reservoir and several large electric motor driven pumps for a 300 kW capacity. This system currently provides hydraulic power to eight dedicated test beds supporting a variety of research topics and capabilities in the lab via supply pipes running along the walls of the main lab area. The temperature of the oil supplied in these lines can be controlled using heat exchangers installed on the power supply so that experimental investigations can be conducted at specific oil viscosities. This capability, in combination with the various test beds that use the supply, has resulted in the creation of accurate hydraulic loss models for selected axial-piston pumps, the validation of various properties of tribological interfaces in these pumps, and the development and demonstration of new hydraulic transmission concepts using these pumps.
Semi-Anechoic Chamber
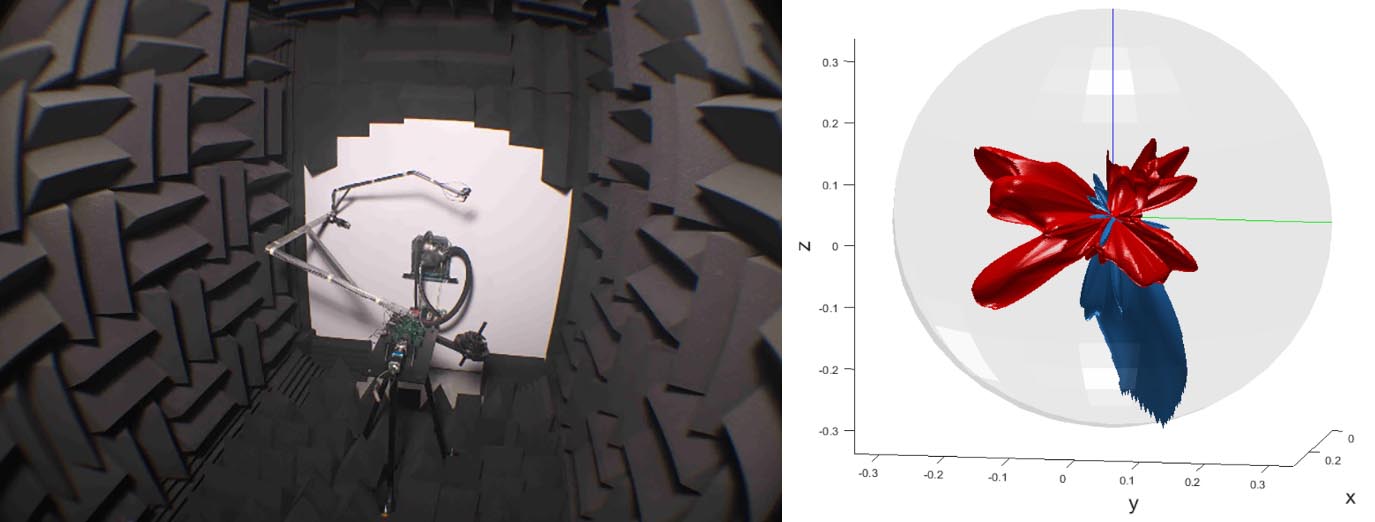
Maha's Noise, vibration, and Harshness (NVH) research focuses on a "Quiet by Design" philosophy. Through the use of our in-house semi-anechoic environment, Maha pioneers are experimentally diagnosing the noise emitted by positive displacement machines. The combination of state-of-the-art experimental techniques and a strong history of pump modeling provides the crucial information required for the development and verification of advanced NVH predictive tools for the design of quieter machines.
Surface Profilometer for Investigating Micro-surface Waviness and Wear

The Maha lab in 2011 acquired a Mitutoyo stylus surface profilometer to allow for further investigation on the impact of micro-surface shaping and wear inside hydraulic pumps and motors. The profilometer is able to measure the change in height of a specimen with excellent resolution (~0.01 µm) as the stylus slowly traverses in a straight line along the surface. The profilometer is very useful in determining accurate inputs for our numerical pump modeling efforts. Many lubricating surfaces have been measured so that the effects of their unique wear profile or manufacturing-based curvature can be investigated.
High Performance Computing Cluster

Researchers at Purdue have access to the
supercomputing facilities available at Purdue University. Additionally, a cluster of 31 computers and 274 computational cores linked with a private 1 Gbps Ethernet network. A Dell PowerEdge R815 server with Quad AMD Opteron processors and 128 GB ram is also installed into the computing cluster. All job scheduling and resource allocation is handled automatically by the
HTCondor software suite running on a Debian Linux job scheduling server. Users log in to the job scheduling server to submit simulations to the cluster. Once submitted, a job is assigned to a computer that has enough available processor cores and memory to accommodate the job's requirements. A single computer may simultaneously run multiple jobs. Once a job is complete, its output and log files are returned to the job scheduling server where the user can retrieve them.
Conference Rooms and Offices
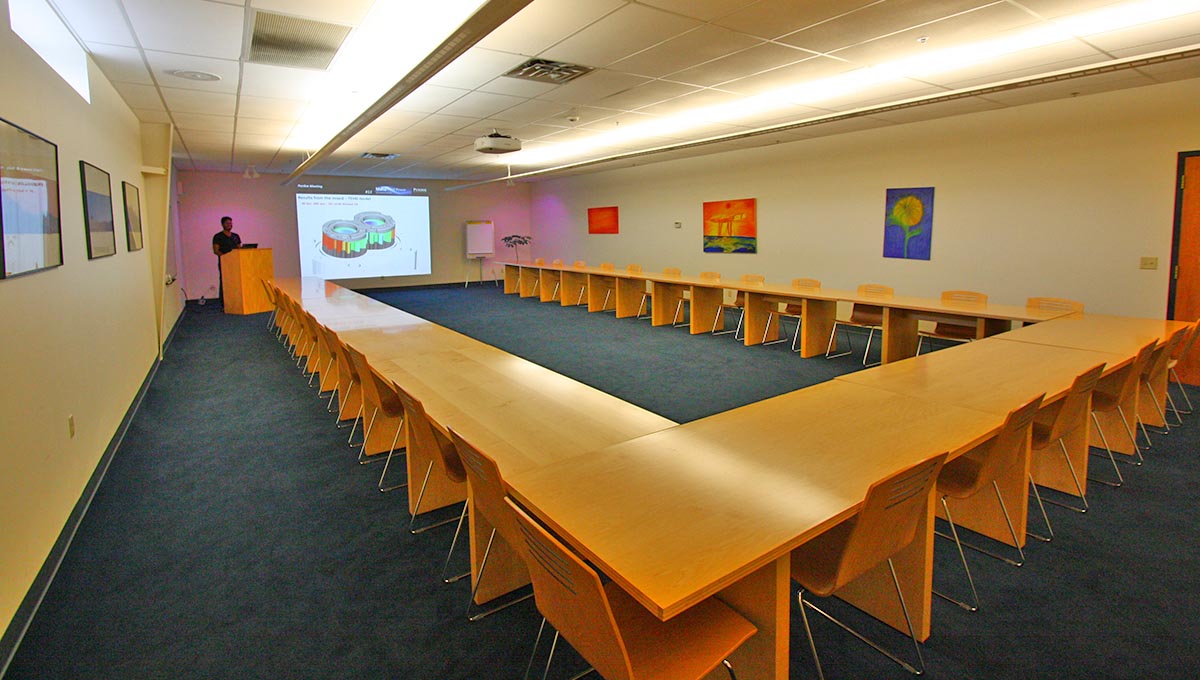
Maha Fluid Power Research Center is part of a large office complex, capable of hosting conferences, symposiums, and other events. Several conference rooms can accommodate large groups, and Maha offers lots of modular office space for your team. Free wi-fi is provided by Purdue University. And large parking lots around the building offer plenty of space to demonstrate heavy equipment.
Back to top <<<