Purdue Energizes Battery Technology
Author: | Amy Raley |
---|---|
Magazine Section: | Strategic Growth Initiative |
College or School: | CoE |
Article Type: | Article |
If Ralph Waldo Emerson were alive today, he’d likely say that a better battery — not a better mousetrap — would make the world beat a path to your door.
Lithium-ion batteries are hot — literally and figuratively. They’re in everything from smartphones, laptops and hoverboards to commercial airplanes and electric cars. They also store huge amounts of electricity on the power grid. But the batteries’ literal heat — which has caused explosions and fires ranging from minor mishaps to downed airplanes — is a big problem.
If that weren’t trouble enough, lithium’s steep price and limited supply make it unsustainable.
“The limited global availability of lithium resources and high cost of extraction hinder the application of lithium-ion batteries for large-scale energy storage,” says Vilas Pol, an associate professor of chemical engineering and associate professor of materials engineering by courtesy.
Pol, who is investigating potassium as a lithium alternative, has shown that potassium would work better than lithium using anodes made from carbon nanofibers. Batteries need electrodes — an anode and cathode — to function. Anodes in most lithium-ion batteries are made of graphite.
“Carbon nanofibers demonstrate great potential as an anode material for potassium-ion batteries,” Pol says. “We studied batteries for up to 1,900 charge-discharge cycles, which is pretty remarkable.” The 1,900 charge cycles compare with what Apple estimates as a 400-charge-cycle capacity for today’s iPhone lithium-ion batteries. That translates to about two years of average use.
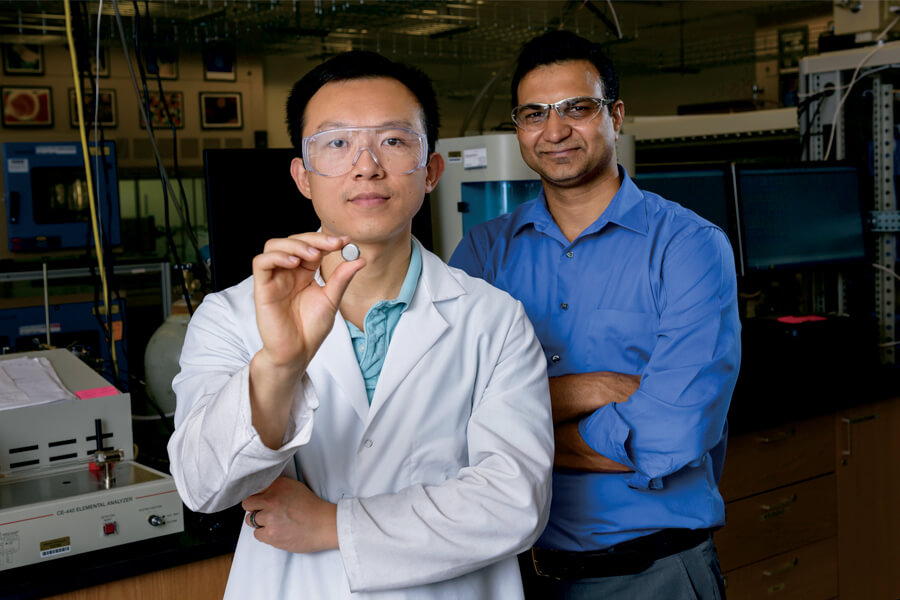
A Need for Speed
Pol’s research also shows potassium-ion batteries as vastly superior when it comes to charging time. After a mere six minutes of charging, their capacity was already at 110 milliamps — one-third a lithium-ion battery’s capacity after 10 hours of charging, Pol says.
“Carbon nanofibers allow the battery to be charged much faster because the ions have to travel a very short distance,” he says. “The typical cellphone battery contains particles that are 15 to 20 micrometers in diameter, which is a much greater distance than this fiber-like architecture. That’s why it takes two to three hours to charge your phone.”
Swift charging is a very big deal. Speedy charges are essential for any battery technology competing for use in electric cars because consumers will want cars they can refuel as fast as they pump gas.
Pol leads the Vilas Pol Energy Research (ViPER) Group and Laboratory. Since 2014, the ViPER laboratory has served as Purdue’s premier center for battery fabrication and testing.
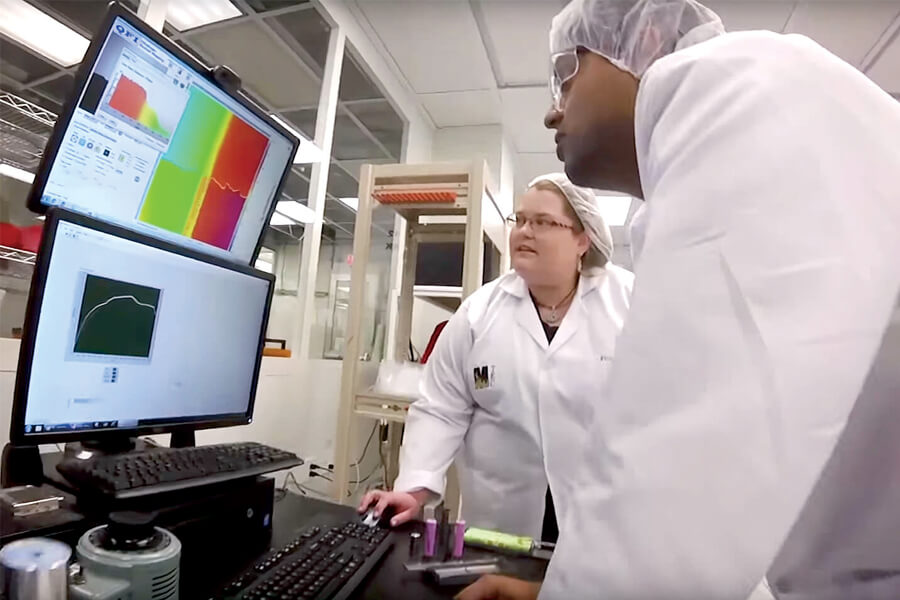
The Holy Grail of Batteries?
Eric Nauman, professor of mechanical engineering and co-founder of IFBattery LLC (IF stands for immiscible fluids), has helped develop an “instantly rechargeable” battery that is not only fast charging, but has a long life. It’s also safe, affordable and environmentally friendly.
“It is simply much safer; it doesn’t really have any explosive potential like the lithium batteries,” he says. “It’s much safer but it still has a very high-power density, and that’s key.”
Nauman envisions future charging stations that would work much like today’s gas stations. He says they will require “massive infrastructure development. IFBattery is developing an energy storage system that would enable drivers to fill up their electric or hybrid vehicles with fluid electrolytes to re-energize spent battery fluids — much like refueling their gas tanks.”
He also says the technology would be safe for the environment because the spent battery fluids or electrolytes would be collected and taken to a solar farm, wind-turbine installation, or hydroelectric plant for recharging. “The electrolytes would then be reconstituted, so you don’t have to burn anything. You don’t have to add to greenhouse gasses.”
Yet another benefit of the IFBattery technology is its lack of a membrane. Membranes in current batteries are associated with higher costs, shortened lifespans and fires. The membrane-free batteries could be safely stored in homes and would be stable enough to meet major production and distribution requirements, the researchers say.
Current steps toward commercialization of the technology include building large-scale prototypes and seeking manufacturing partners. The researchers are pursuing funding to support those efforts.
IFBattery licensed part of the technology through the Purdue Research Foundation Office of Technology Commercialization and has developed patents of its own. The company is a member of the Purdue Startup Class of 2017.
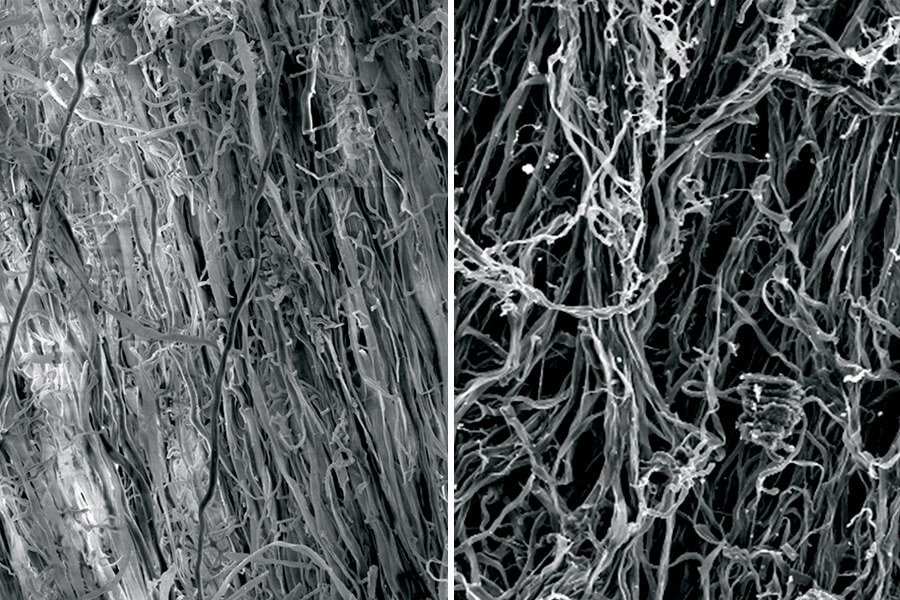
In the Meantime
Until new battery technology is market-ready, lithium-ion batteries will remain the industry standard. That’s where Amy Marconnet comes in. She and her team in Purdue’s Thermal and Energy Conversion Lab dissect batteries and test materials that make up electrodes and the critical component called a separator.
An assistant professor of mechanical engineering, Marconnet is working to fully understand, and ultimately solve, the lithium temperature safety problem. She has dissected the batteries’ inner “jelly roll” layers of positive electrode, separator and negative electrode.
She says that when the batteries start to overheat, the separator that keeps the positive and negative electrodes apart can melt and cause a short circuit that produces an explosion or fire.
“We have found the thermal conductivity of the separator layer, which is a very porous layer, to be fairly low compared to some of the values reported in literature,” Marconnet says. “That value is critical for predicting how hot the cell will get and whether the separator will ultimately fail.”
Marconnet says that the data she’s gathering will help improve the safety and reliability of lithium-ion batteries for a wide range of their uses from laptops to vehicles. “We can have higher capacity and larger battery cells that we aren’t worried about overheating anymore.