Research continues on an eventual 140-million-mile mission to Mars, developing the latest transportation as well as habitats necessary for the red planet.
But embarking on such a mission and safely living both during and afterward are differing ideas. The latter is the research focus of Alina Alexeenko.
“We know how to get to space, but that’s not the same as knowing how to survive there,” says Alexeenko, professor of aeronautics and astronautics. “If we are to do a colony on Mars, we’re not going to send pills or a pharmaceutical factory. There won’t be a CVS on Mars.”
To make sure astronauts have the nourishment and medication to survive such a yearlong venture into space, Alexeenko has taken on several research projects involving lyophilization, also called freeze drying.
Lyophilization uses a sterile, vacuum environment to remove water from products such as food and medicine after they are frozen. The process converts the frozen moisture in the items to a vapor, eliminating the liquid phase.
The results increase the stability and shelf life of medication and improve the ability to store and transport food while keeping its nutritional value. Lyophilization is used in almost half of biopharmaceutical medications created.
“We have to reinvent how medicines will be stored and carried and lyophilization will be involved because we will need to preserve medicines long term,” Alexeenko says.
Alexeenko is founding co-director of the Advanced Lyophilization Technology Hub, or LyoHub, based in the Birck Nanotechnology Center at Purdue’s Discovery Park. She is joined by Elizabeth Topp, fellow founding co-director and a professor of industrial and physical pharmacy.
Food and medicine aren’t the only items that can be submitted to lyophilization. Alexeenko says a biological water treatment system for space stations and space colonies focuses on keeping bacteria alive in a freeze-dried state. The bacteria can then be used to treat the water.
“I think it’s the least known of the most important technologies invented in the 20th century,” she says. “If you look at the impact, it’s quite significant. There are so many aspects of it beyond space, such as manufacturing and technology.”
Pharmaceuticals are a big recipient of the benefits of freeze drying. It was first used to stabilize blood plasma to treat childhood infections before vaccines were available, later allowed the use of blood banks during World War II and soon after allowed the mass production of penicillin. It is now part of the process for many new anti-cancer and anti-rheumatoid arthritis medicines and many vaccines.
Lyophilization research focuses more on the process itself than with how it can be used. New control methods and sensors are improving a less-than-efficient process that Alexeenko compared to making cookies in an oven, one batch at a time.
“You have the recipe, but you don’t necessarily know what’s going on until it’s done, and you pull them out,” she says. “But sensors can provide information in real time and controls can keep the process within a range that’s safe for the molecules that are impacted.”
Purdue’s LyoHub is made up of a consortium of more than 20 industry leaders in food medicine and other areas. Alexeenko said one of the projects has developed a numerical simulation for understanding probability of lyophilization, allowing for a computer test rather than a costly experimental run.
The industry-university partnership also has produced a first technology road map in lyophilization and is working on the first set of science-based standards for the technology.
Photo At Top:
“We know how to get to space, but that’s not the same as knowing how to survive there.”
— Alina Alexeenko
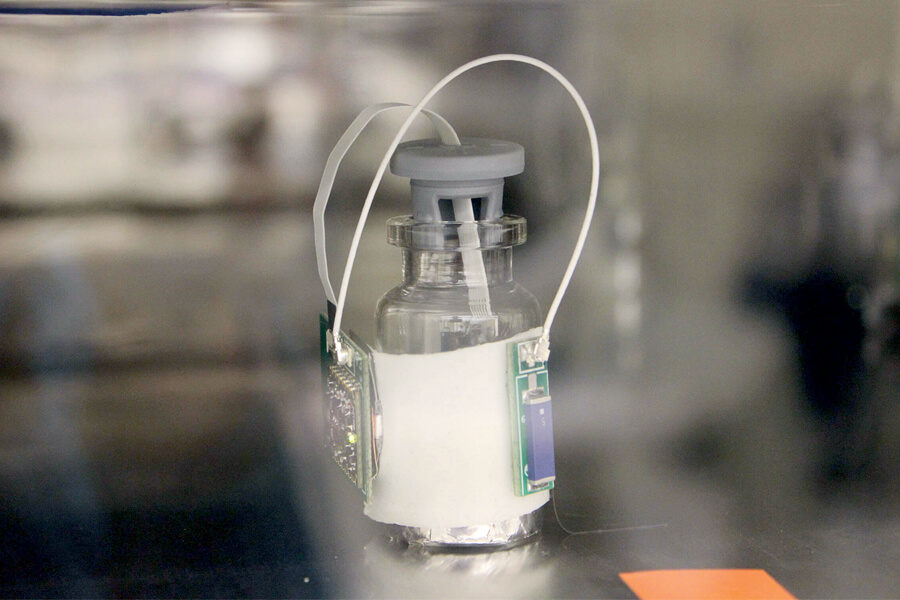
A wireless sensor developed to collect real-time date of the freeze-drying process.
Image provided by Jennifer Gray
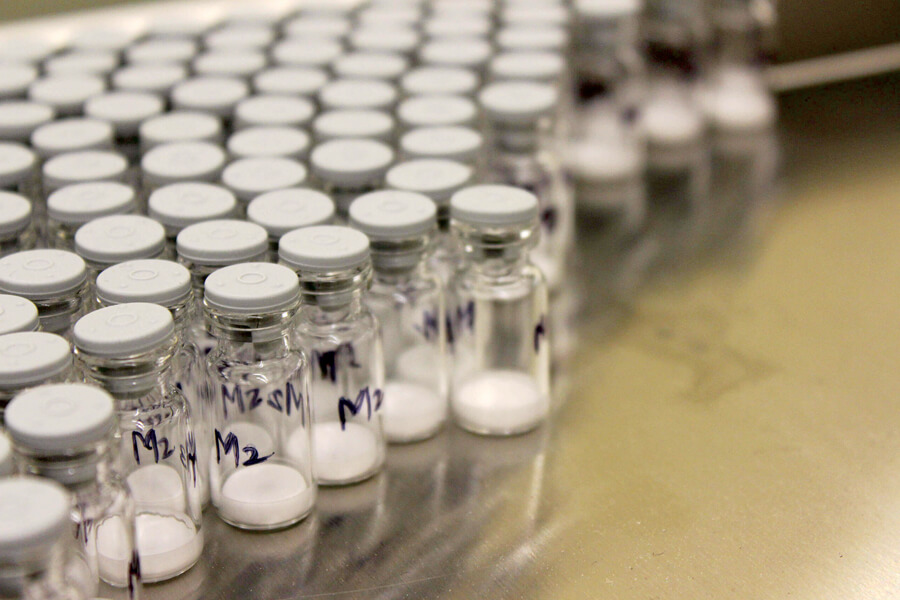
Vials of freeze-dried product.
Image provided by Jennifer Gray