Hybrid Vehicle Electronics Cooling
The automobile industry is presently witnessing unprecedented interest in development of new electric propulsion systems in an effort to transition from conventional engines to economical combustion engine hybrid vehicles in the near term and to fuel cell vehicles in the long term. Evidence of this transition can be found in the FreedomCAR and Fuel Partnership programs spearheaded by the US Department of Energy.
To successfully implement power electronics and electric machines into hybrid and fuel cell vehicles, various thermal characteristics and performance targets must be met. Thermal management will play a paramount role towards achieving those targets, but several barriers must first be overcome. For example, existing thermal management techniques in automobiles are not adequate for dissipating high heat fluxes while limiting the operation of silicon-based electronic components to a temperature of less than 125°C. Additionally, current components are generally both bulky and heavy, resulting in the need for additional structural support and increased use of parasitic power. Therefore, new cooling technologies are sought for power electronics (and also motors) that can tackle higher power densities and reduce volumes and weights.
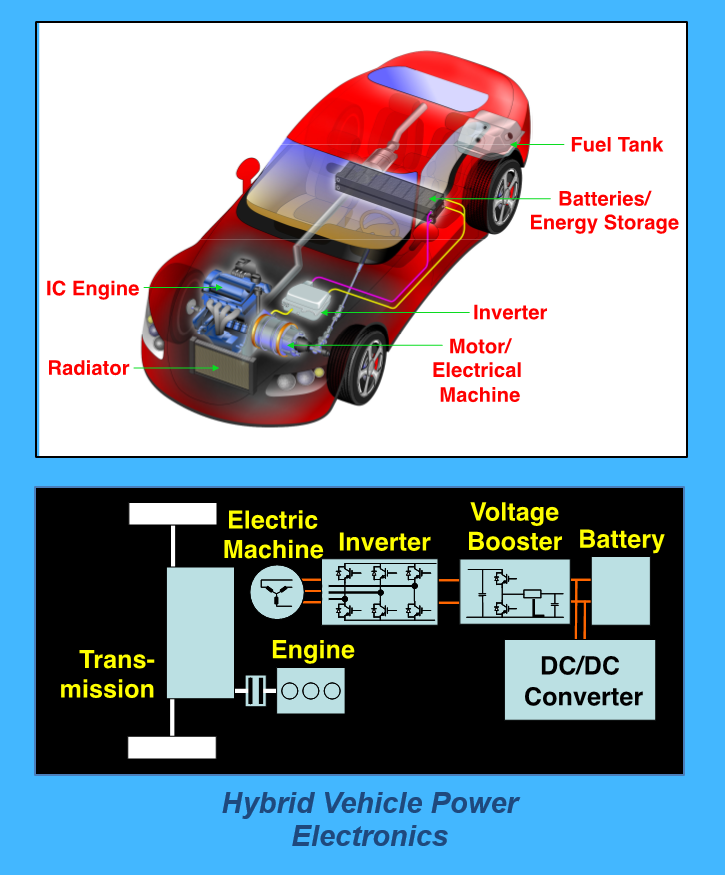
Cooling of the vehicle’s power electronics is achieved by channeling the heat from the chip through different layers of materials separating the chip from the liquid coolant. To achieve the aforementioned thermal goals, our team has developed several two-phase thermal solutions, including jet impingement, spray cooling, and micro-channel cooling. One possible type of coolant is refrigerant such as R134a that can be circulated in a pump-assisted sub-loop. The sub-loop would tap into the vehicle’s primary refrigeration loop and also reject the heat to the vehicle’s air-cooled condenser. Another possibility is to use dielectric coolant such as HFE 7100 with a separate cooling loop.
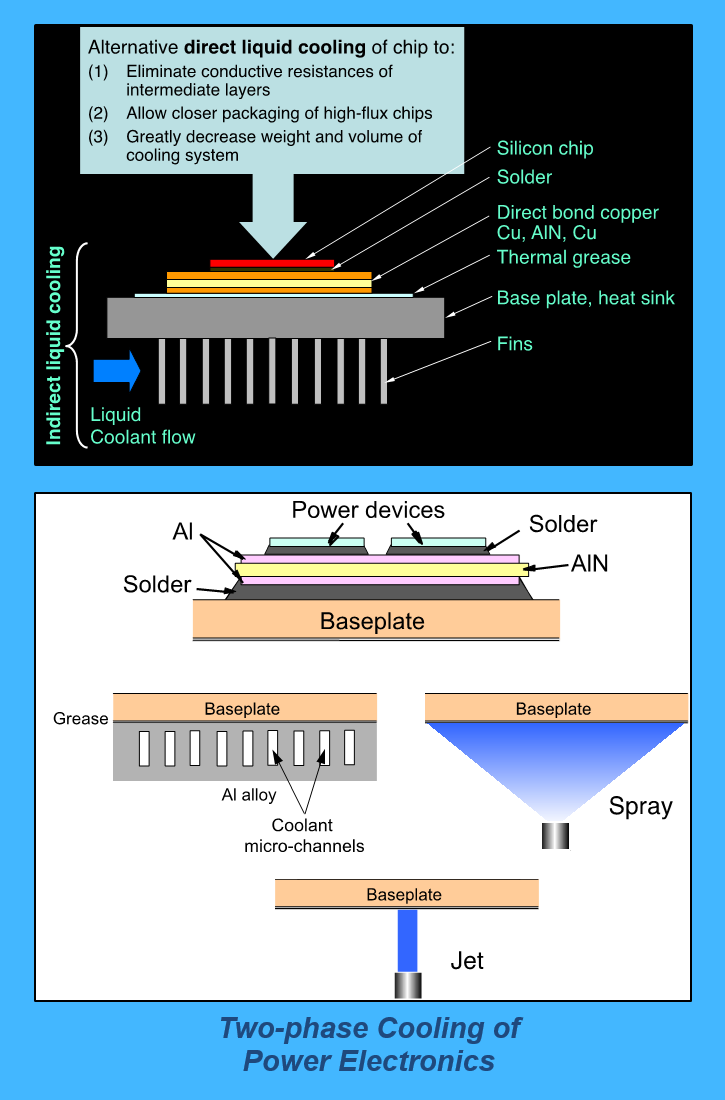